Aluminum billet casting is a pivotal phase in aluminum production, and grasping its nuances can provide a competitive advantage for manufacturers seeking efficiency and quality assurance. The process, integrated with technological advancement and expertise, emphasizes the production of high-grade materials that meet industry demands and innovative material engineering. In this regard, let's explore the operational experiences, technical expertise, and authoritative practices surrounding the aluminum billet casting process.
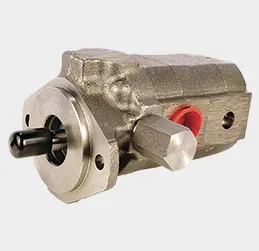
Aluminum's widespread application in construction, automotive, aerospace, and consumer electronics underscores the importance of skilled billet casting. The procedure begins with melting aluminum scrap or pure primary aluminum in a furnace. Experience in handling the furnace temperature precisely is paramount, as this dictates the aluminum's purity and quality. Professionals in the field, utilizing advanced furnaces, often achieve a flawless melt through consistent temperature regulation, ensuring that the molten aluminum reaches optimum viscosity for casting without structural deficiencies.
Casting begins once the aluminum reaches the designated temperature range, approximately between 700°C and 750°C. This stage calls for the adept handling of casting molds, typically cylindrical, intended to shape the molten aluminum into billets. The expertise of the operators is crucial here; they employ continuous or semi-continuous casting methods, leveraging automation to enhance precision while reducing human error. The ongoing computerization in casting parlors facilitates real-time monitoring and adjustments, reflecting an advanced level of technological integration that underscores the industry's expertise.
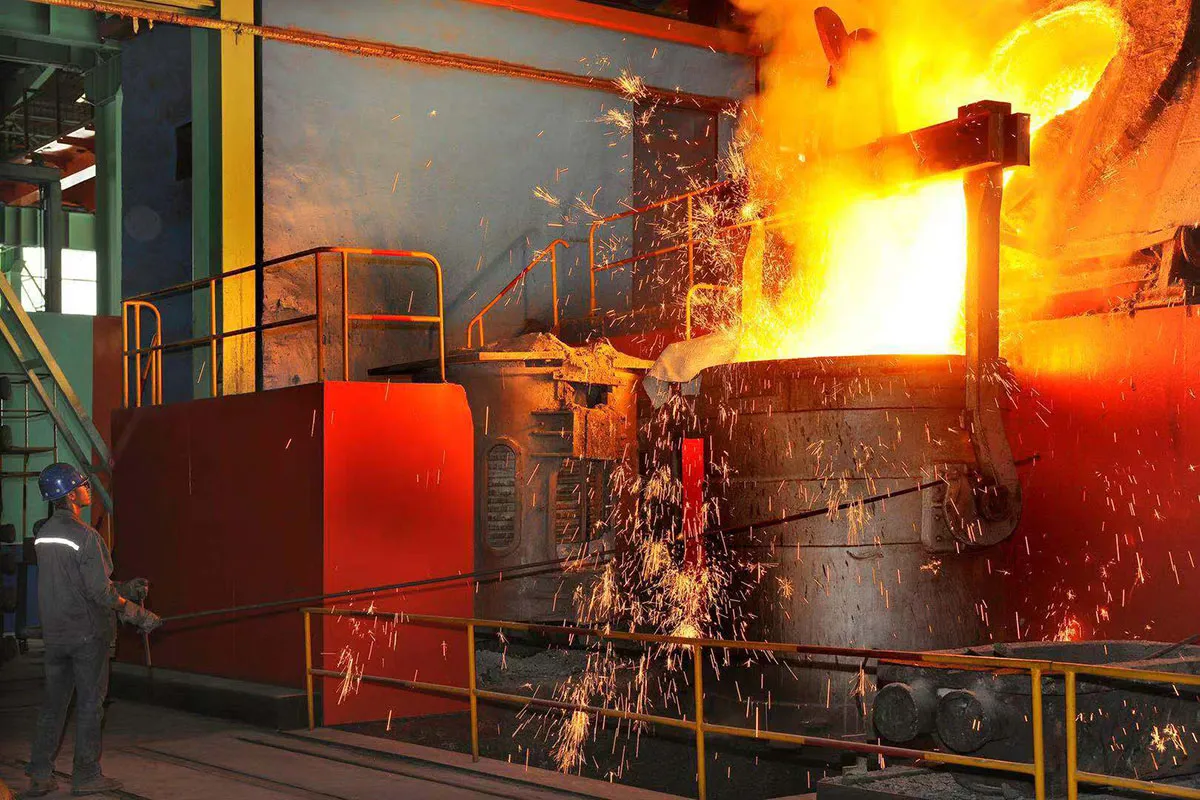
The next phase emphasizes the cooling of the cast aluminum, and it’s in this cooling area that experienced operators demonstrate their ability to judge the perfect solidification rate. Trustworthiness in this stage stems from the meticulous precision and control required to prevent deformations. Utilizing water jets or air-mist cooling techniques, trusted operators ensure even cooling, which is fundamental to preventing internal stresses and material weaknesses that could compromise billet integrity during subsequent manufacturing processes.
aluminum billet casting process
Another significant factor in the billet casting process is addressing undesirable impurities and inclusions. Through the influential use of degassing units and filtration technology, experts within the industry instill an authoritative stance on quality control. Rotating nozzles dispense inert gases, such as argon, to reduce hydrogen concentrations, while ceramic filters sieving the aluminum melt ensure that only the highest quality billets are produced. Adopting these cutting-edge filtration and degassing technologies significantly enhances the material’s purity and performance.
From an authoritative perspective, compliance with international standards like the ISO 9001 reinforces reliability and trust in the production process. Regular audits and certifications from recognized bodies ensure that every billet produced meets stringent quality requirements. Manufacturers demonstrating their commitment to these standards through consistent quality assurance measures establish themselves as reputable players in the aluminum industry.
It is crucial for businesses to align with sustainability trends, recognizing environmental impacts, which have led to innovations such as energy-efficient furnaces and advanced recycling processes. The industry’s shift toward reducing carbon footprints by improving operational efficiency and waste management is both a testament to environmental responsibility and an economic imperative, aligning with both customer expectations and regulatory requirements.
In conclusion, aluminum billet casting is a sophisticated process demanding a blend of technology, expertise, and stringent quality control. It’s the dedication to precision, integrated systems use, and the commitment to international standards that establishes manufacturers as leaders in the field. By fostering innovation and upholding sustainability, the aluminum industry can continue to evolve, meeting the ever-expanding needs of global markets while upholding absolute trust in the quality and reliability of their products.