The aluminium die casting process is a critical manufacturing method that has revolutionized numerous industries worldwide. With its roots tracing back to the early 20th century, this highly specialized technique has grown to embody precision, efficiency, and innovation. Delving into the nuances of this process reveals its pivotal role in producing complex and high-quality components, instrumental for various sectors such as automotive, aerospace, and electronics.
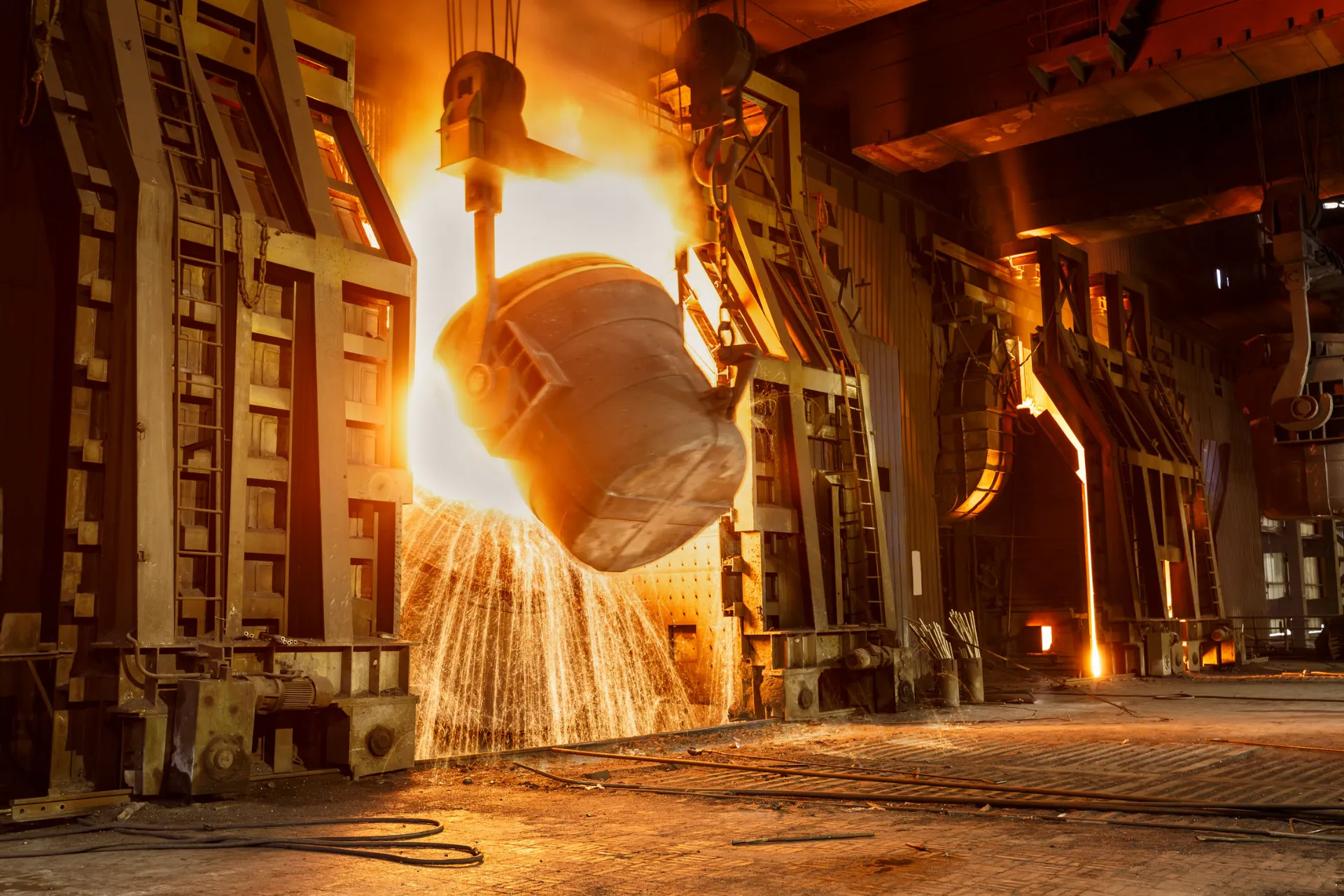
A hallmark of the aluminium die casting process is its ability to create intricate parts that boast exceptional dimensional accuracy.
This process involves injecting molten aluminium into steel molds under high pressure. The precision with which these molds are crafted determines the accuracy of the final product, ensuring that the components produced exhibit near-net-shape characteristics, thus minimizing the need for further machining.
One of the critical aspects that demonstrate expertise in this field is the understanding of the alloy properties used in die casting. Aluminium alloys are favored for their excellent strength-to-weight ratios, corrosion resistance, and thermal and electrical conductivity. An expert approach involves selecting the appropriate aluminium alloy tailored to the specific requirements of the part, thereby optimizing performance and longevity.
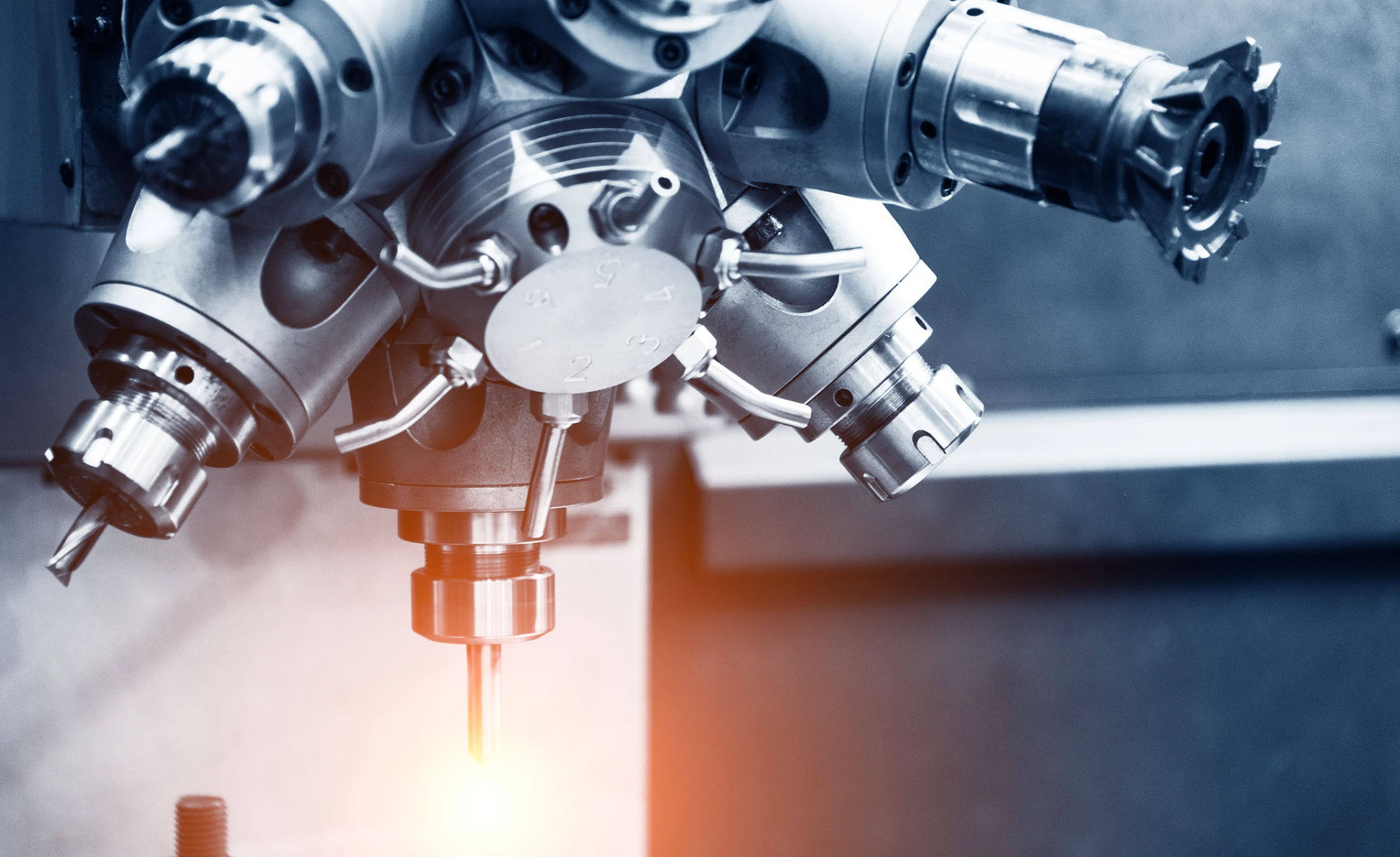
Authority in the aluminium die casting domain is underpinned by an intricate knowledge of the equipment and tooling involved. Die casting machines, ranging from hot chamber to cold chamber types, play a significant role in determining the efficiency and quality of the casting process. A firm grasp of the operational parameters — such as temperature settings, injection pressure, and cycle times — is essential for producing consistent, high-quality outputs.
Moreover, advancements in die casting technology have introduced automation and computer-aided systems, enhancing precision and reducing human error. Incorporating such sophisticated technologies demonstrates not only authority but a commitment to maintaining a cutting-edge position within the industry.
aluminium die casting process
Trustworthiness in aluminium die casting is further cemented by adherence to stringent quality control measures. Implementing rigorous inspection routines, employing non-destructive testing methods, and adhering to international standards such as ISO 9001 are paramount to ensuring the reliability of the components produced. This dedication to quality underscores a manufacturer’s reliability, engendering trust with clients and stakeholders.
Additionally, from an experiential viewpoint, understanding the nuances of the entire value chain in die casting — from raw material procurement to final product delivery — is crucial. This holistic understanding allows for optimization at every step, ensuring cost-effectiveness and sustainability, two factors increasingly prioritized by global markets.
Sustainability is also addressed through the recyclability of aluminium, making die casting a more eco-friendly manufacturing option. Drawing from personal experience in the industry, leveraging closed-loop recycling programs not only reduces costs but also aligns with global environmental goals, an increasingly critical consideration.
In conclusion, the aluminium die casting process embodies a blend of art and science, requiring a profound grasp of materials, equipment, and technology to excel. As a domain characterized by rapid technological advances, staying informed and adaptable is key. By consistently striving for excellence, embracing innovation, and committing to quality and sustainability, practitioners within this field solidify their standing as not just manufacturers, but trusted partners in industrial advancement.