Metal stamping is a transformative process in the manufacturing realm that goes beyond the simplistic view of shaping metal sheets. It's a meticulous orchestration of precision, expertise, and technology which collectively forge components integral to countless industries.
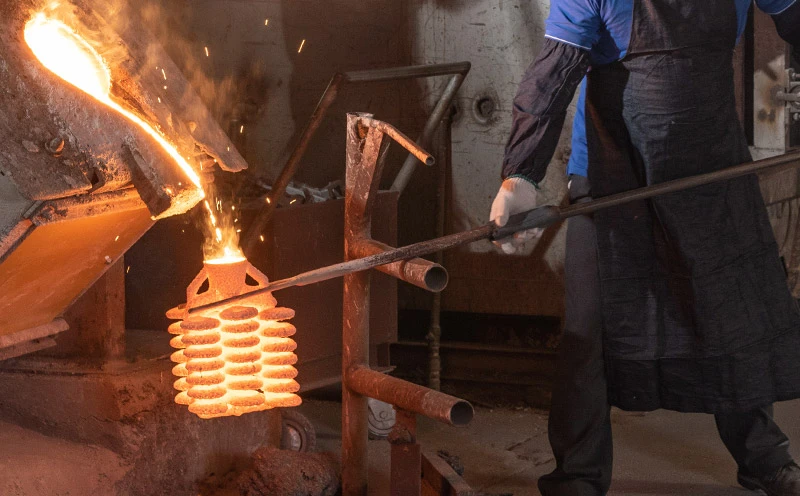
The journey of metal stamping begins with the selection of a suitable metal sheet. This choice is critical, as the material must align with the specific attributes needed for the final product, such as strength, conductivity, or malleability. Metals like steel, copper, aluminum, and brass are renowned for their diverse properties, making them prevalent choices in various stamping applications.
Once the raw material is chosen, the spotlight shifts to the design phase. This involves Computer-Aided Design (CAD) software, which allows for intricate blueprints tailored to meet stringent specifications. CAD not only enhances precision but also provides simulations to foresee potential challenges. Such foresight reduces trial-and-error iterations and ensures the end product aligns perfectly with the intended application.
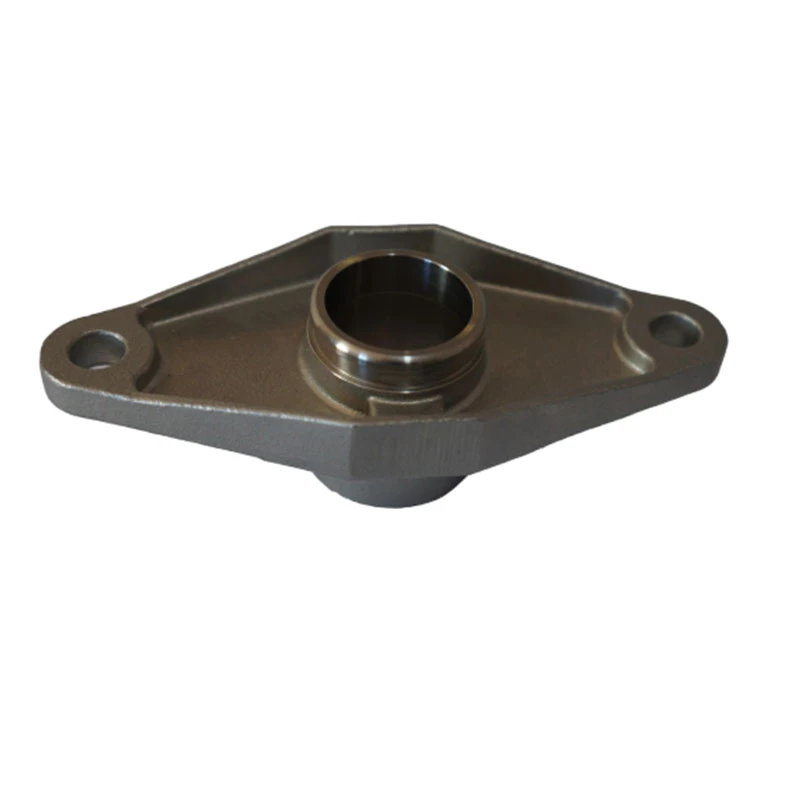
Tooling is the next vital component, where the tools involved in shaping, cutting, and forming the metal sheets are meticulously crafted. These tools, often made from hardened steel, must withstand significant pressure and repetitive use. Tooling involves the creation of die sets, which consist of male and female components that shape the metal as needed. The design and precision of these dies are crucial, as even minor errors can lead to significant deviations in mass production.
The actual stamping process can be executed through several techniques, each providing unique benefits based on the project's needs. Progressive die stamping, which is lauded for its efficiency, is ideal for high-volume production. In this method, a strip of metal moves incrementally through multiple stations, each designed to perform a specific operation such as bending, punching, or cutting. Transfer die stamping, on the other hand, involves transferring the parts from one station to another, suitable for larger or more complex parts. Fourslide stamping offers versatility, using four sliding tools to manipulate the metal from different angles, making it perfect for intricate components.
what is metal stamping process
Adherence to precision throughout the entire process is non-negotiable. Variables such as pressure, speed, and alignment must be meticulously controlled. Advanced machinery equipped with sensors and feedback systems has revolutionized this aspect, allowing for real-time adjustments and minimizing human error. Quality control doesn't stop at real-time adjustments, however. Post-production inspections involve using sophisticated measuring equipment to ensure that all specifications are met and any irregularities are swiftly addressed.
The expertise involved in metal stamping also extends to understanding the nuances of thermal and mechanical properties of metals, knowledge of stress-strain relationships, and mastering the art of die maintenance and troubleshooting. It's a discipline that continuously evolves, with innovations in materials science and digital technologies paving the way for more efficient and precise stamping methods.
The authority of metal stamping is evidenced by its omnipresence. From automotive to electronics, aerospace to healthcare, stamped metal components are indispensable. Car engines, circuit boards, medical devices, and countless everyday items rely on the reliability and durability afforded by this process. The trustworthiness of metal stamping is borne from a legacy of delivering consistent, high-quality components in industries where precision is paramount.
In essence, metal stamping is not merely a manufacturing process; it's a testament to human ingenuity and mastery over materials and machines. For businesses reliant on precise metal components, partnering with a proficient metal stamping provider is crucial. Such collaboration ensures that products are not only crafted to perfection but are also equipped to meet the rigorous demands of modern engineering marvels.