Sand casting is a time-honored technique that has been utilized for centuries to create intricate metal components. This method relies heavily on the cornerstone element known as sand casting sand. Despite technological advances, the quality and type of sand chosen can significantly influence the final product's fidelity and finish. Understanding the nuances of sand casting sand can prove invaluable for businesses and artisans aiming to achieve precision and excellence in their metalworks.

In the sand casting realm, experience dictates that the initial step of choosing the right sand is paramount. Not all sands are created equal. A seasoned metallurgist might point out that the optimal sand should have a balanced grain size, which provides the mould with the necessary stability while also allowing gases to escape during the casting process. The granularity affects the surface finish of the cast product; finer grains typically yield a smoother surface, a factor that cannot be overlooked in high-precision manufacturing industries.
The expertise in selecting sand also extends to its composition. Traditionally, silica sand has been the most prevalent choice due to its high melting point and availability. However, in recent years, the conversation among professionals has shifted towards utilizing alternatives like chromite or zircon sand, especially in cases where thermal expansion and refractoriness are concerns. For dense alloys requiring fine detailing, opting for sands with higher thermal conductivity is advantageous.
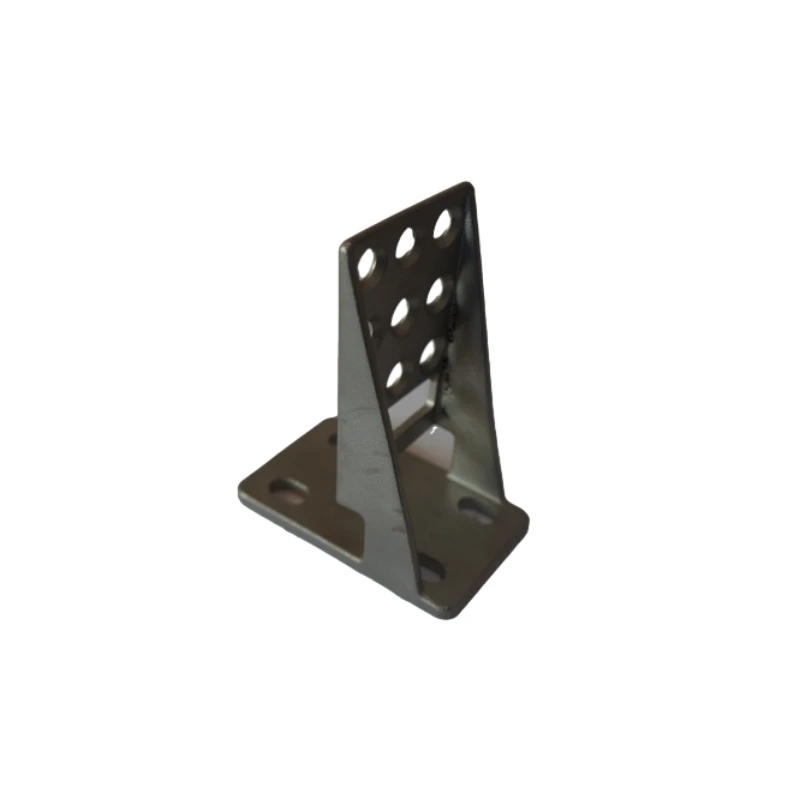
sand casting sand
An authoritative stance in the industry would emphasize the importance of binder systems used with sand. There are two predominant types, namely clay-based green sand and chemically bonded sand. Green sand, a mixture of silica sand, clay, and water, is renowned for its reusability and cost-effectiveness. On the other hand, chemically bonded sands provide superior precision due to their rigidity and stability during casting, which is critical for achieving complex geometrical designs and minimizing defects.
Trustworthiness in the production process comes not only from materials but also from adherence to environmental standards and safety protocols. As health and environmental concerns rise globally, the shift towards eco-friendly sand options and processes, such as the development of synthetic sand and reduced waste sand recycling techniques, showcases a commitment to sustainable practices. Organizations that openly communicate their adherence to these standards proactively demonstrate their reliability and gain consumer trust.
In conclusion, a knowledgeable approach to selecting and using sand casting sand, backed by substantial experience and expertise, is crucial for any enterprise seeking to excel in the metal casting domain. By prioritizing the appropriate type of sand, understanding the implications of binder selection, and committing to environmentally sustainable practices, companies can ensure the production of superior cast products. These factors not only enhance product quality but also position a company as an authoritative and trustworthy player in the industry, meeting the demands of a discerning global market.