In the realm of metal casting, where precision and quality are paramount, resin sand casting emerges as a standout methodology. This process, an intricate blend of art and science, offers solutions that cater to industries demanding high-grade components with intricate designs and exacting production standards.
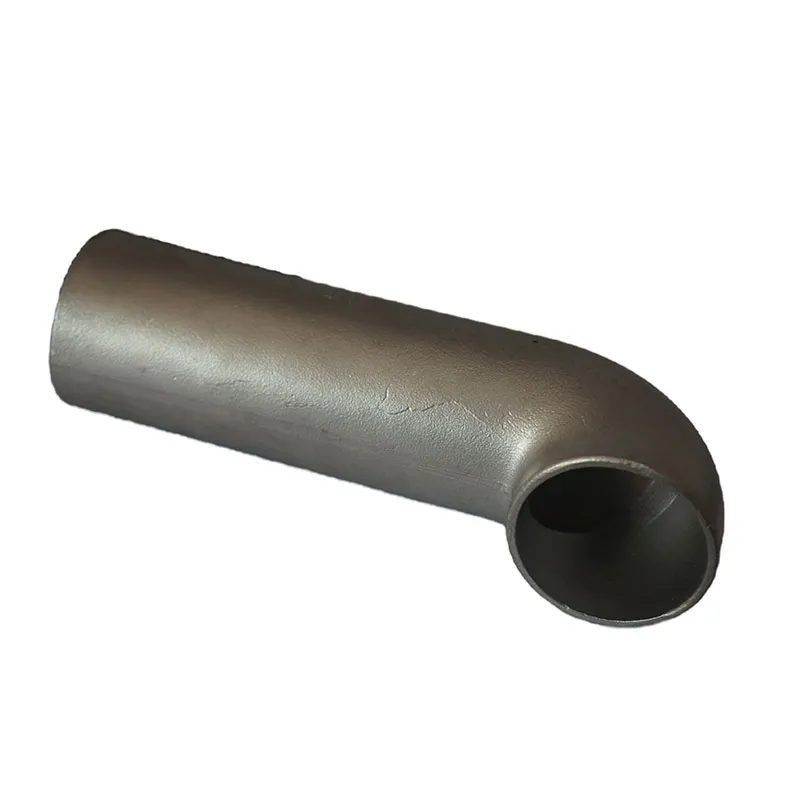
Experience with resin sand casting begins with understanding its distinctive flexibility and durability. Unlike traditional sand casting, which employs green sand, the resin sand casting process uses a synthetic resin binder along with sand. This combination provides a mold that can withstand high temperatures and pressures during metal pouring, resulting in parts with superior surface finishes and dimensional accuracy. Manufacturers deploying this technique often note a significant reduction in the errors caused by mold imperfections, ensuring a higher yield of quality products.
One of the most notable experiences shared by industry veterans is the process's adaptability. Resin sand casting is not limited by part complexity, allowing for the creation of complex geometries and fine detail that other methods might struggle to produce efficiently. Experience reveals that this method is particularly beneficial in automotive, aerospace, and heavy machinery sectors, where precision-engineered components are essential.
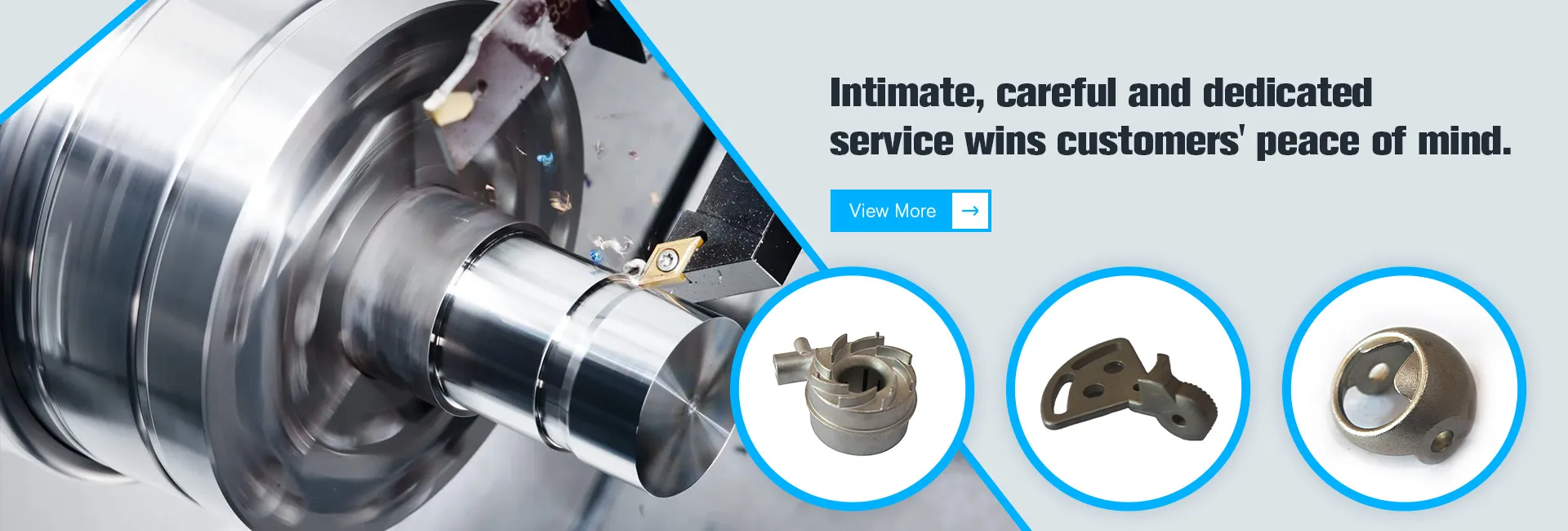
Expertise in resin sand casting is underpinned by a comprehensive understanding of the binder systems used. The type of resin and its curing mechanism can dramatically affect the mold's performance and the resulting cast. The choice between no-bake, cold box, or hot box systems, each having its distinct curing process and strengths, must align with the production requirements and the properties desired in the final product. Mastery over these options ensures that the castings produced meet rigorous industry standards, crucial for safety-critical applications.
Furthermore, expertise extends to the meticulous control of process parameters. Factors such as sand grain size, binder ratio, and mold curing time are meticulously managed to ensure optimal results. Advanced simulation technologies are often employed by experts to preemptively address potential casting defects, such as voids or incomplete filling, which could compromise the integrity of the final product. The ability to predict and mitigate these issues underscores the level of proficiency required to succeed with resin sand casting on a large scale.
resin sand casting
Authoritativeness in resin sand casting is often demonstrated by those who continuously push the boundaries of this age-old technique. Innovative uses of resin sand casting are seen in the integration of new alloys, which bring enhanced properties such as increased strength or thermal resistance, addressing the ever-evolving demands of modern industries. Collaboration with research institutions and continuous investment in R&D are hallmarks of authoritative entities in this field, who not only employ the process but also contribute to its evolution.
The authoritative voices in resin sand casting often emerge from longstanding partnerships with leading global manufacturers, providing consistent, high-quality outputs and pioneering industry standards. These leaders influence market trends and establish benchmarks, offering insights and technological advancements that other entities in the field aspire to emulate.
Their influence extends beyond mere production; it shapes the very future of casting technology.
Trustworthiness is an attribute that resin sand casting naturally confers when executed with precision and expertise. The trust placed in this casting method is rooted in its ability to consistently deliver high-caliber components that meet the rigorous demands of operational use. Certifications and adherence to international quality standards serve as testaments to a provider's commitment to excellence. Testimonials from satisfied clients, showcasing the performance and reliability of components produced through resin sand casting, further accentuate its dependability.
For businesses seeking to implement resin sand casting, trust is also reflected in the transparency of the process. Clear communication regarding material selection, process stages, and expected outcomes fosters a collaborative relationship between the casting provider and client. An open exchange of information and feedback ensures that any issues are swiftly addressed and that the final product aligns with or surpasses client expectations.
In conclusion, resin sand casting remains an eminent choice for industries requiring precision, complexity, and reliability. By leveraging the rich experience, in-depth expertise, authoritative advancements, and the foundational trustworthiness associated with resin sand casting, manufacturers gain access to a process that not only meets but exceeds the high standards of modern engineering requirements. For those navigating the competitive landscape of metal casting, embracing the potential of resin sand casting can translate to significant advantages, securing their position as leaders in innovation and quality.