When exploring manufacturing techniques, sand casting stands as one of the most traditional yet versatile methods, used for producing complex metal components across various industries. This method involves creating a mold from a sand mixture, into which molten metal is poured, allowing it to cool and form the desired part. To make informed decisions about employing sand casting for your product needs, it's imperative to weigh its advantages and disadvantages.
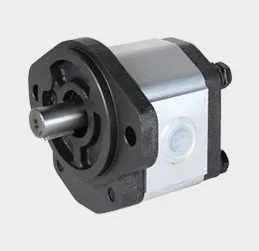
One of the primary pros of sand casting is its cost-effectiveness. Unlike other metal casting techniques that require expensive tooling, sand casting utilizes sand molds that are relatively inexpensive to produce. These molds can be reused or easily created for each new production, making it ideal for both small and large batch sizes. This significantly reduces the initial investment and overhead costs, making it accessible for startups and businesses focusing on custom production.
Furthermore, sand casting offers high versatility in terms of material selection. It accommodates a wide range of metals, including aluminum, iron, bronze, and brass, providing flexibility for manufacturers to choose the appropriate material based on the mechanical properties needed for the end product. The technique also allows for the production of both simple and complex geometries, including intricate designs that might be challenging for other manufacturing processes.
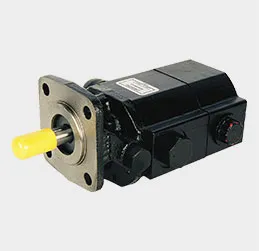
Another notable advantage is the adaptability of sand casting in size and weight production. From small parts like gears and pulleys to large components such as engine blocks and ship propellers, sand casting can handle sizeable variations in part dimensions and weights. The method provides opportunities for engineers to create prototypes and test new designs without committing to full-scale production immediately.
Despite these advantages, sand casting also has several limitations. One significant con is its surface finish quality. Sand casting typically renders a rougher surface compared to other methods like die casting or investment casting. This may necessitate additional machining or finishing processes, increasing time and costs for achieving the desired surface texture and dimensional accuracy.
pros and cons of sand casting
Another limitation is the tolerances sand casting can achieve. Generally, the dimensional accuracy of sand-cast parts is lower, with tolerances being wider than those attainable through precision casting methods. This can pose a challenge when producing parts where high precision is critical, possibly resulting in increased post-processing work or the need for alternative methods to achieve tighter tolerances.
Furthermore, the mechanical properties of sand-cast components can sometimes be inferior, especially if the cooling process is not optimally controlled. The cooling rate affects the metal's microstructure, influencing properties like strength and ductility, which could be less desirable in comparison to parts made via other casting methods.
For manufacturers contemplating sand casting, it's crucial to leverage the method's strengths by selecting it for projects where design flexibility, initial cost savings, and large-scale production are priorities. Care must be taken to assess whether the potential drawbacks in surface finish and precision are manageable within the product's design specifications or if supplementary processes are necessary.
In summary, sand casting is a pragmatic choice for a wide range of manufacturing needs, balancing cost, flexibility, and functionality against some compromises in finish and precision. Its suitability is best evaluated based on specific project requirements, allowing you to effectively harness its benefits while mitigating its limitations through strategic planning and execution.