Plaster sand casting is a sophisticated manufacturing process widely utilized across various industries for its precision and adaptability when creating complex metal components. Recognized for its unique ability to produce high-quality and intricate parts, this technique fundamentally relies on a refined mix of plaster molds filled with molten metal. The distinctive properties of plaster make it an ideal medium for achieving precise dimensional accuracy and high surface finish in castings, distinguishing plaster sand casting in the realm of metal forming technologies.
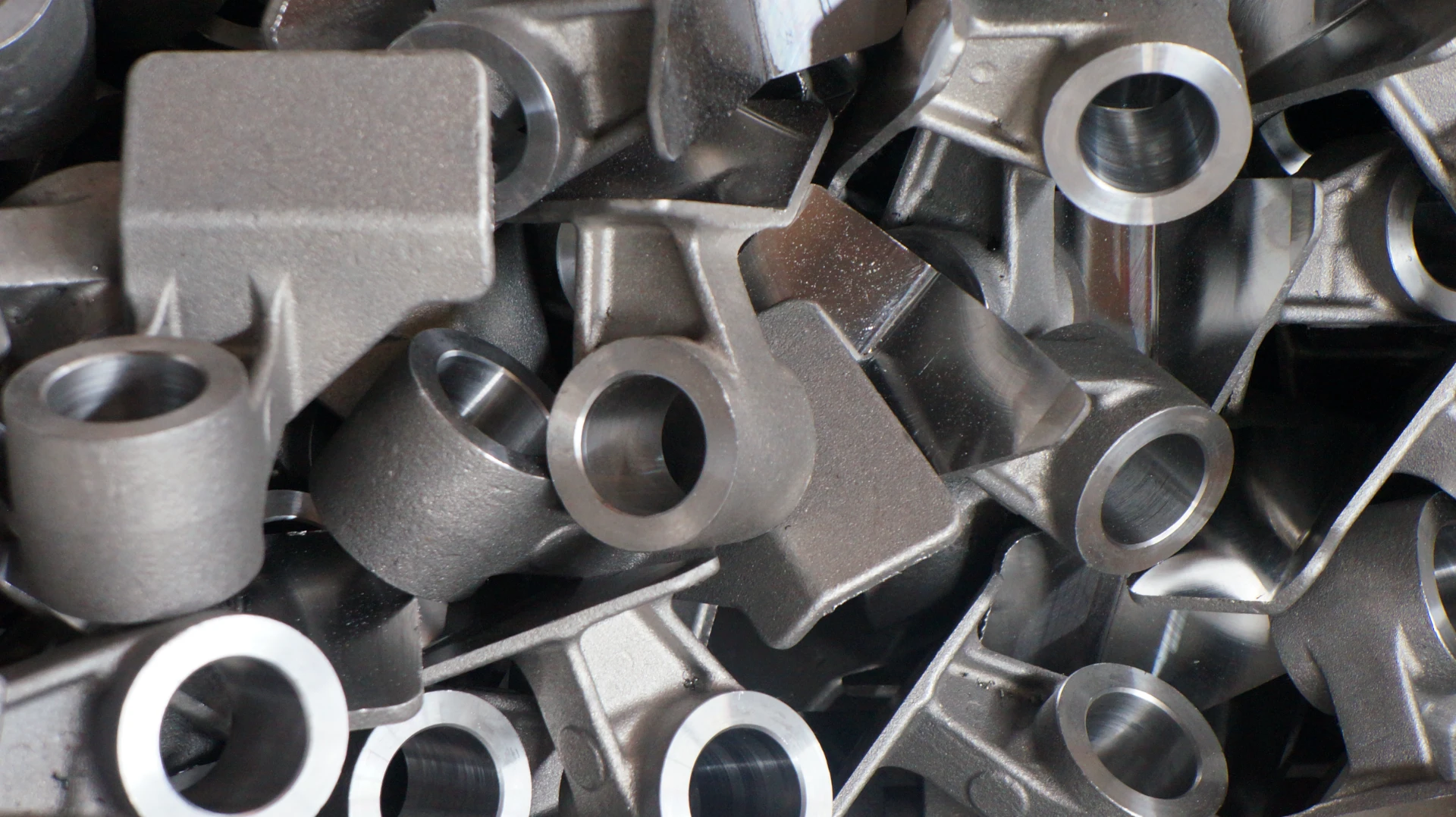
The process begins with the preparation of a pattern, typically crafted from metal or plastic, which defines the geometry of the final product. This pattern is used to form a mold cavity within a plaster mixture. Composed of gypsum, water, and various strengthening additives, the plaster slurry envelops the pattern within a mold box. Once the plaster solidifies and cures, the pattern is carefully removed, leaving a detailed cavity ready for the casting process. This precise methodology ensures a high degree of repeatability and accuracy, crucial for industries demanding exacting standards, such as aerospace or automotive sectors.
Upon completing the mold preparation, metallurgy comes into play, demonstrating the technical expertise inherent in plaster sand casting. Skilled foundry professionals select appropriate metal alloys—aluminum, bronze, or steel—best suited for the intended application.
The molten metal is then meticulously poured into the plaster cavity under controlled conditions. The slow rate of cooling in plaster molds allows for the formation of a refined microstructure within the cast metal, reducing internal stresses and enhancing the mechanical properties of the component.
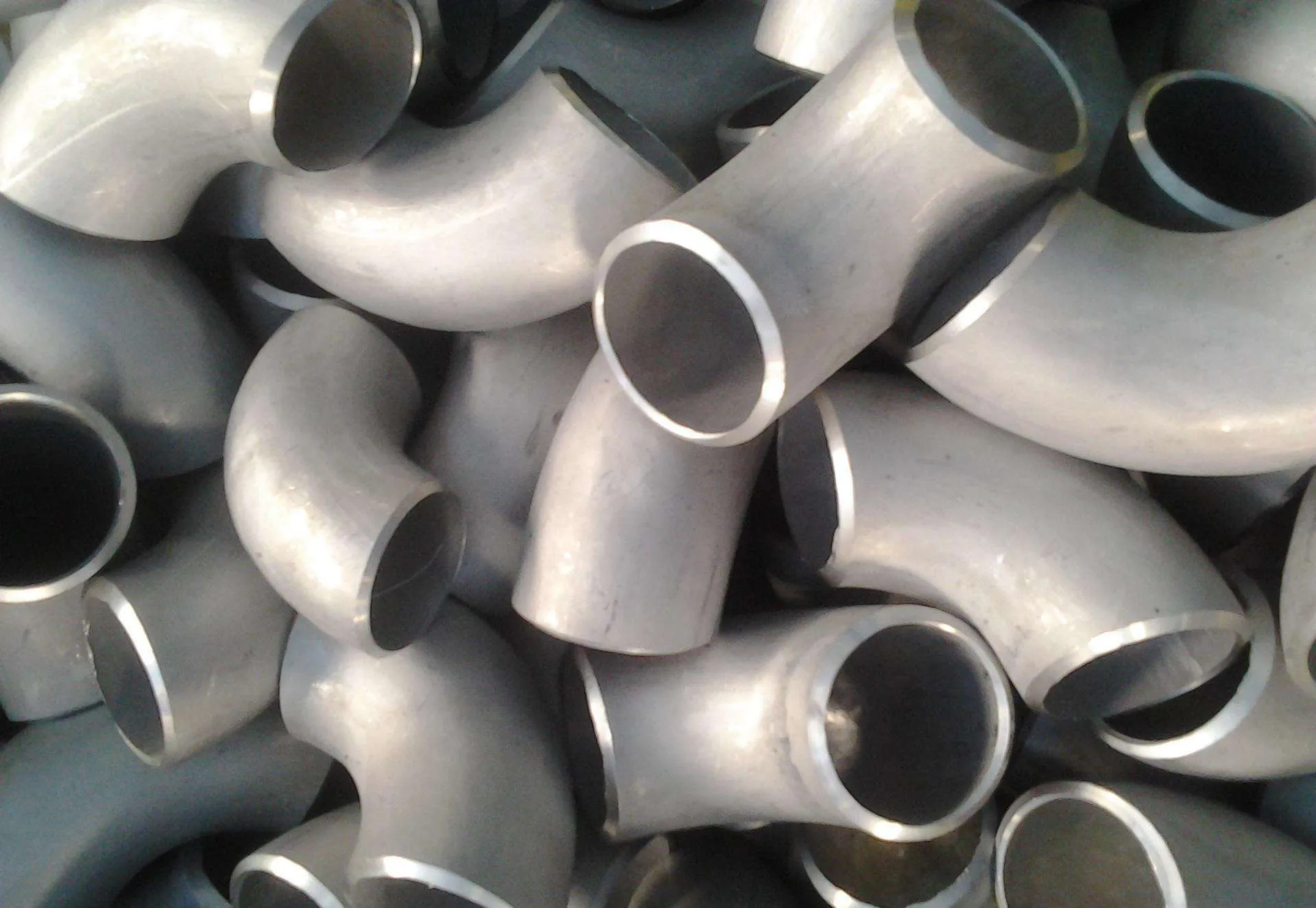
The expertise involved in plaster sand casting extends to post-casting processes as well. Once the metal cools and solidifies, the plaster shell is broken away to reveal the cast part. From here, additional steps like heat treatment, machining, and finishing may be employed to refine the component to its final form. Each phase of the plaster sand casting process requires a high degree of technical knowledge and experience to ensure the dimensional fidelity and quality of the final product.
plaster sand casting
This sophisticated method of casting proves its authoritativeness in the industry through its versatility and efficiency. Plaster sand casting caters specifically to the production of items with intricate geometries, thin walls, and precise dimensions, transcending the limitations of other casting methods. It is particularly valued for producing prototypes and short production runs where traditional methods may fall short.
Trustworthiness in the plaster sand casting process is affirmed through rigorous quality control measures. Foundries employ advanced testing and inspection techniques, such as X-ray radiography and ultrasonic testing, to examine cast products for internal defects, ensuring they meet stringent industry standards and customer specifications. These rigorous evaluations not only validate the integrity of the product but also build confidence in the reliability of the casting process.
In the evolving landscape of manufacturing, plaster sand casting stands out for its ability to offer superior precision, material efficiency, and adaptability. Its capacity to integrate traditional craftsmanship with modern technology ensures it remains a valuable player in producing complex components that adhere to the highest quality and performance expectations. By leveraging these strengths, companies continue to trust plaster sand casting as a pivotal technique that meets the ever-changing demands of the modern industrial market.