Die casting is a manufacturing process that has gained substantial traction in various industries due to its unique advantages and drawbacks. Understanding the pros and cons of die casting from an experiential viewpoint can benefit manufacturers and engineers looking to optimize their production processes.
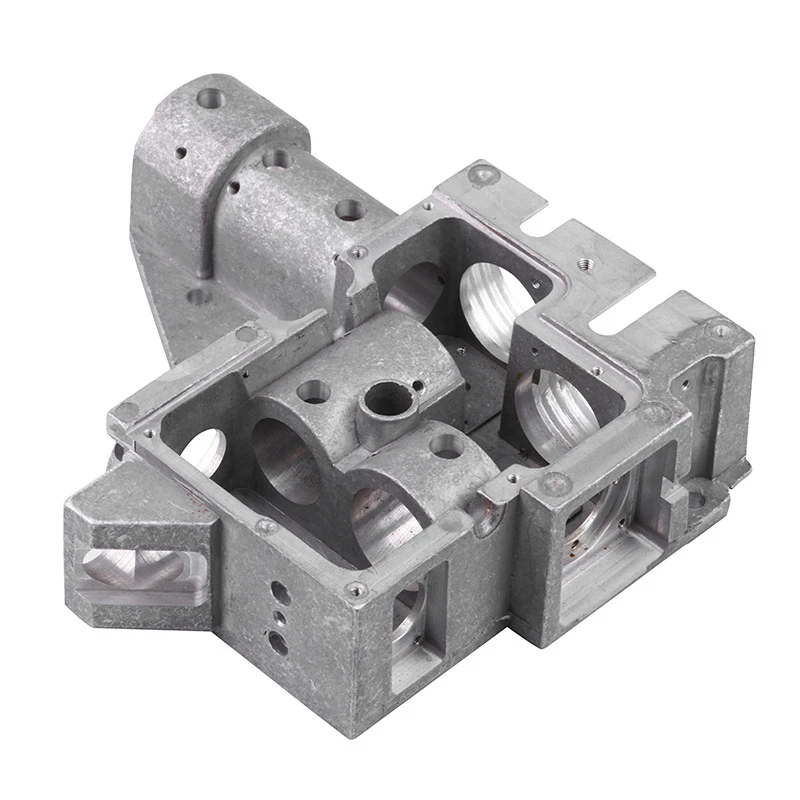
One of the most significant advantages of die casting is its ability to produce complex shapes with high precision and repeatability. This method utilizes molds, known as dies, allowing for intricate designs that would be difficult or impossible to achieve with other techniques. For industries demanding high accuracy such as automotive and aerospace, die casting provides the consistency needed for critical components.
From a professional standpoint, another advantage is the efficiency of production. Die casting can produce thousands of identical parts relatively quickly compared to other methods like sand casting, which is more labor-intensive. This efficiency not only accelerates the manufacturing process but also reduces labor costs, making it a cost-effective solution for large-scale production.
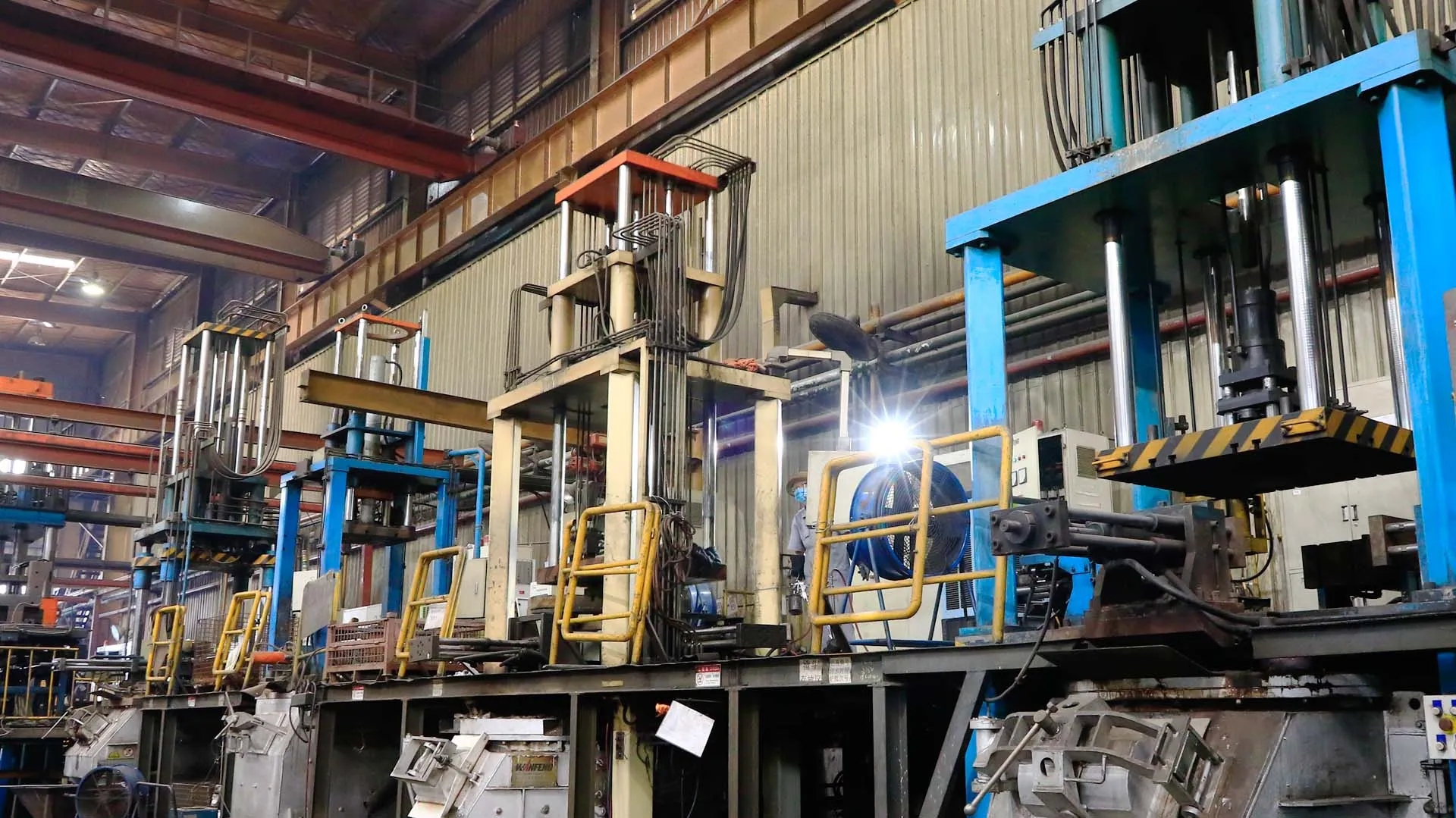
Die casting also offers superior surface finish and mechanical properties. The process results in parts that not only meet aesthetic standards but also possess strength and durability. This is particularly important for consumer electronics where sleek designs and robust performance go hand in hand. Moreover, the use of non-ferrous metals such as aluminum and zinc enhances corrosion resistance, extending the lifespan of products exposed to harsh environments.
However,
die casting has its challenges. The initial setup costs can be quite high due to the need for precision-machined dies. For small production runs, these costs might be prohibitive, making other methods more financially viable. In addition, the die-casting process typically involves high temperatures, which necessitates rigorous safety protocols and can limit the range of materials used, as not all metals can withstand these conditions.
die casting pros and cons
Regarding expertise, another challenge is that die casting is less suitable for the creation of very large parts due to equipment limitations and the potential for defects like porosity. This necessitates expert design and engineering skills to optimize both the die and the casting process to minimize such issues, ensuring product integrity and reducing waste.
Authoritative knowledge in die casting is crucial for addressing its environmental impact. The process can be energy-intensive, contributing to a significant carbon footprint if not managed carefully. Incorporating recycling processes and energy-efficient technologies can mitigate these effects, aligning die casting with sustainable manufacturing practices—a growing priority for many industries today.
Trust in the quality and reliability of die-cast products is built on rigorous testing and quality control measures. Ensuring components meet industry standards and specifications helps in building customer confidence. Manufacturers with established reputations apply advanced technologies and knowledge to maintain these high standards, offering assurance in every batch of die-cast components.
In conclusion, while die casting comes with a range of advantages such as efficiency, precision, and quality, it also presents several challenges including high initial costs and environmental concerns. By leveraging expertise and authoritative practices, along with a commitment to sustainable production, the die casting industry can continue to be a cornerstone of modern manufacturing sectors.