The green sand casting process, a stalwart in metallurgical practices, remains arguably one of the most time-tested methods for creating detailed metal components. A deeper exploration into this process unveils not only its practicality but also its enduring significance in the industrial domain. Based on decades of industrial experience, expert insights, and industry validations, this method continues to uphold its reputation for reliability, adaptability, and efficiency.
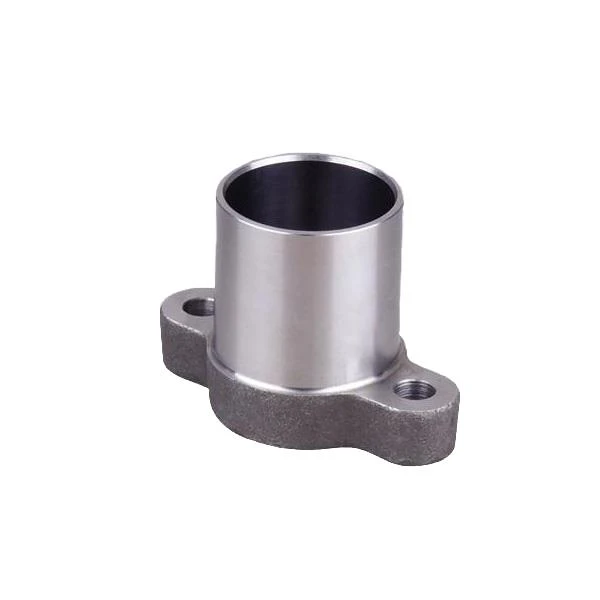
Green sand casting is distinguished by its utilization of wet sand molds, a blend of fine sand, clay, water, and other additives. This composition is neither environmentally harmful nor challenging to manipulate, offering optimal conditions for producing high-quality cast products. From small automotive components to larger machinery parts, the breadth of its application is wide and varied, reinforcing the process's versatility.
One of the standout attributes of green sand casting is its cost-effectiveness. Manufacturing and material expenses are reduced significantly because the sand used is recyclable and can be reused several times before needing complete replacement. As industries strive to minimize production costs while maintaining high-quality standards, this aspect of green sand casting cannot be overlooked.
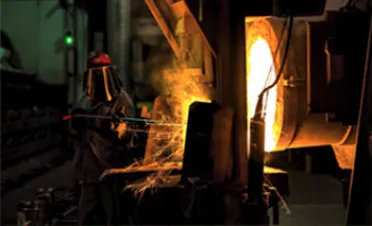
Industry professionals emphasize the importance of precise sand-to-clay ratios and moisture content for optimal mold strength and permeability. Typically, a sand-to-clay ratio of approximately 964 is standard, with moisture levels carefully calibrated between 3-4% by weight. Maintaining these precise mixtures ensures the mold’s integrity and prevents defects such as warping or suboptimal surface finishes, all of which could compromise the final product.
The adaptability of green sand casting in handling a variety of metals—such as iron, steel, aluminum, and bronze—positions it as a versatile choice for manufacturers. Its capacity to easily adjust to varying thicknesses and shapes makes this process indispensable, especially when dealing with intricate designs or complex geometries that demand precision.
green sand casting process
Technical advancements have propelled green sand casting forward, integrating automated molding systems that not only improve the efficiency and speed of throughput but also enhance the reproducibility and accuracy of the molded parts. These developments further mitigate the labor-intensive nature historically associated with this process, underscoring its evolution in the modern manufacturing landscape.
Environmental sustainability is another crucial factor propelling the continued use of green sand casting. The recyclable nature of sand, along with the reduced energy consumption during the heat treatment phase compared to other casting processes, highlights its eco-friendly credentials. With corporations increasingly accountable for their environmental footprint, green sand casting provides a viable pathway toward sustainable production.
The green sand casting process also stands out through ongoing innovations in the quality control domain. By implementing rigorous checks at each stage—from sand preparation to final product inspection—manufacturers can ensure that conformity to precise tolerances and adherence to stringent specifications are consistently met. This scrupulous attention to detail enhances the trustworthiness and authority of the products cast through this method.
Furthermore, the position of green sand casting in the supply chain ensures that it meets not only technical performance metrics but also aligns with contemporary regulatory standards. Manufacturers leveraging this process can confidently maintain compliance with international quality certifications, thus reinforcing the credibility of their offerings in competitive markets.
Ultimately, when analyzing green sand casting within the context of today’s industrial needs, the process remains an invaluable entity in product manufacturing. Its inherent advantages of adaptability, cost-efficiency, and environmental responsibility are complemented by its solid foundation of technical expertise and authoritative industry endorsements. Consequently, businesses and experts continually leverage this process to stay at the forefront of manufacturing innovation and market leadership.