In the world of manufacturing, the terms cast and die hold significant importance. They are integral to creating a vast array of components used in industries ranging from automotive to aerospace. Understanding their distinct processes, applications, and the latest innovations can significantly boost a product-focused website's SEO, catering to users looking to deepen their knowledge or make informed purchasing decisions.
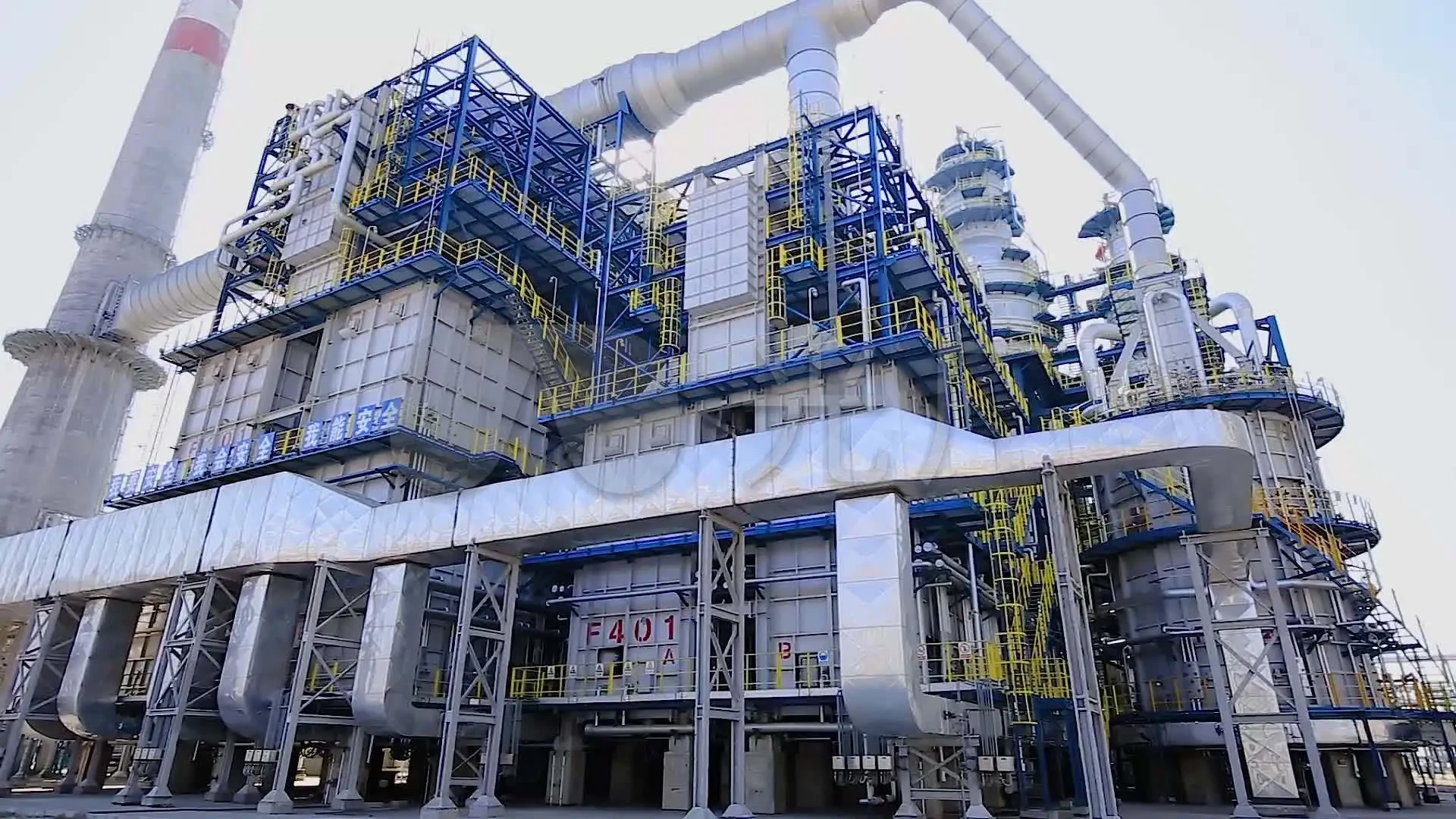
Casting, a process entrenched in historical significance, involves pouring molten metal or other materials into a mold to create a desired shape. This technique, prized for its versatility, can produce complex geometries that would be impossible or uneconomical to achieve with other manufacturing methods. From aluminum to stainless steel, casting can accommodate a wide range of materials, enhancing its utility across various sectors.
One of the critical advantages of casting is its ability to produce large components with intricate details. Industries such as automotive and construction often favor this process because it allows for the fabrication of parts like engine blocks and structural elements with precision and efficiency. Moreover, new advancements in casting technology, such as 3D sand printing for mold creation and rapid prototyping, are pushing the boundaries of traditional capabilities, enabling quicker turnaround times and reducing costs.
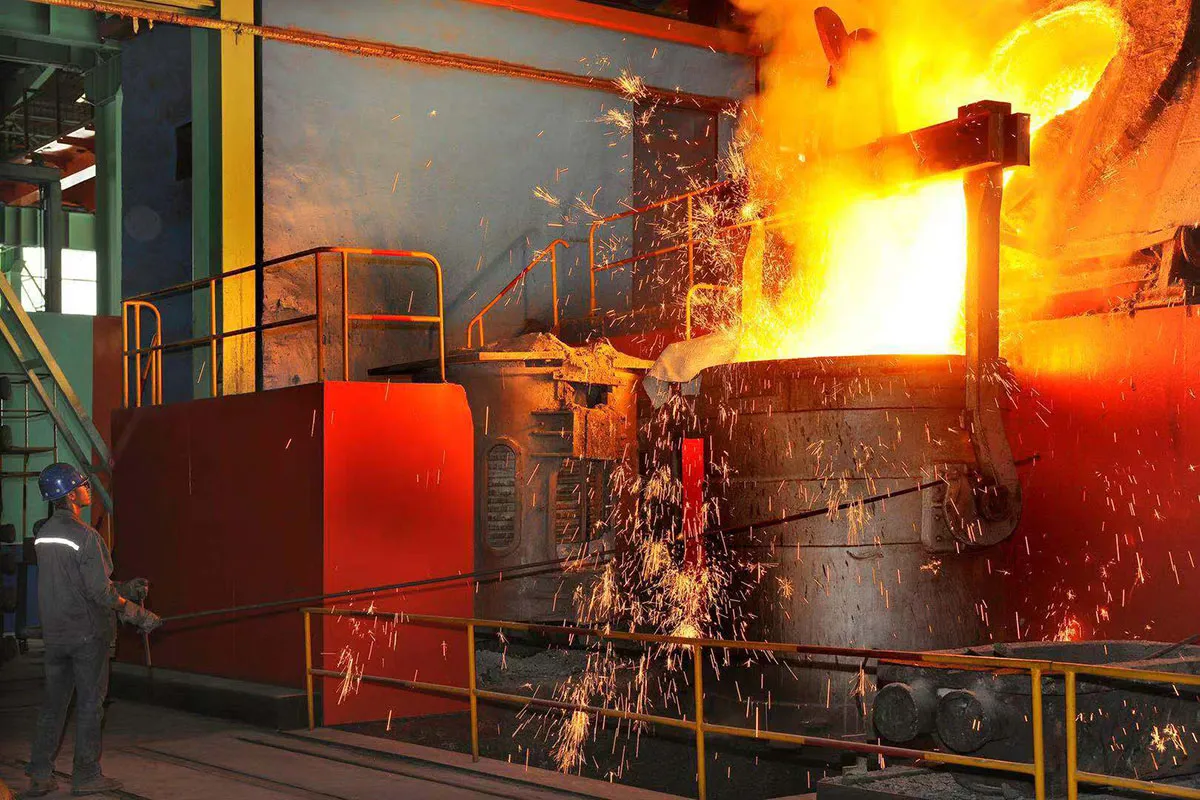
In parallel, die casting is a specialized form of casting that utilizes high-pressure techniques to force molten metal into reusable steel molds or dies. This method is typically reserved for high-volume production due to its ability to produce consistent and high-quality parts with tight tolerances. Materials like aluminum, zinc, and magnesium are commonplace in die casting, attributes that make it invaluable for producing components in high-demand industries such as electronics and automotive.
Die casting stands out for its capability to produce parts that require minimal post-processing, thanks to the precision of the molds used. The resultant components often boast excellent surface finishes, reducing the need for additional machining or finishing operations. Recent developments in die-casting technology include the use of simulation software to predict potential defects and optimize the die design. This reduction in trial-and-error not only saves cost but also enhances the reliability of the produced parts.
cast and die
The convergence of casting and die casting in modern manufacturing environments highlights their complementariness. Companies are increasingly adopting hybrid techniques, leveraging the strengths of each method to optimize production processes. For instance, casting may be used to produce the base form of a component, which can then be refined through die casting to achieve the desired detail and precision.
For businesses and industry stakeholders, the importance of choosing between casting and die casting cannot be overstated. Factors such as production volume, material selection, and component requirements must be scrutinized to determine the best approach. Engaging with suppliers who demonstrate expertise and innovation in these processes is crucial for ensuring quality and cost-efficiency.
Establishing a product-focused website that delves deeply into the intricacies of casting and die casting can provide substantial SEO advantages. By offering exclusive insights and real-world examples, such content not only elevates the site's authority but also enhances its trustworthiness among potential customers. Publishing case studies, expert interviews, and detailed process explanations can further bolster the website's reputation, capturing the attention of both industry insiders and curious consumers.
Ultimately, the casting and die casting industries are poised for continued growth and innovation. As environmental considerations shape manufacturing practices, both processes are evolving to incorporate sustainable materials and methods, aligning with global efforts towards greener production solutions. This ongoing transformation undoubtedly presents exciting opportunities for businesses willing to invest in cutting-edge technologies and practices.
For those aspiring to become leaders in the casting and die casting domains, staying informed about the latest trends, technological advancements, and industry best practices is imperative. A forward-thinking approach will not only fortify product development strategies but also enhance the overall competitiveness of the business in an increasingly dynamic market landscape.