Aluminum die casting stands at the forefront of modern manufacturing techniques, highly revered for its efficiency in producing complex, durable, and lightweight components with exceptional precision. As a seasoned professional in the realm of die casting, this article delves deep into the intricacies that make aluminum die casting a premier choice for industries across the globe, highlighting not just its technical aspects but also its unmistakable benefits in real-world applications.
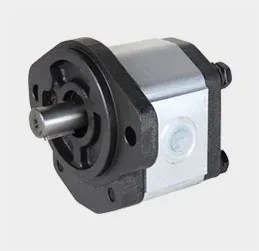
Throughout years of industry experience, aluminum die casting has proven itself as an unparalleled method in the production of high-volume parts. At its core, the process involves forcing molten aluminum into a mold cavity under high pressure. Once cooled, the result is a robust component that requires minimal post-production work. The beauty of this technique lies in its ability to produce intricate shapes with those thin walls and tight tolerances that are often unattainable through alternative manufacturing methods.
From the perspective of expertise, the advantages of aluminum as a material are numerous. Its lightweight nature does not come at the expense of strength, providing an ideal solution for industries where weight reduction is crucial without compromising structural integrity, such as automotive and aerospace. Moreover, aluminum's excellent thermal and electrical conductivity makes it a favorite in electronics and telecommunications.
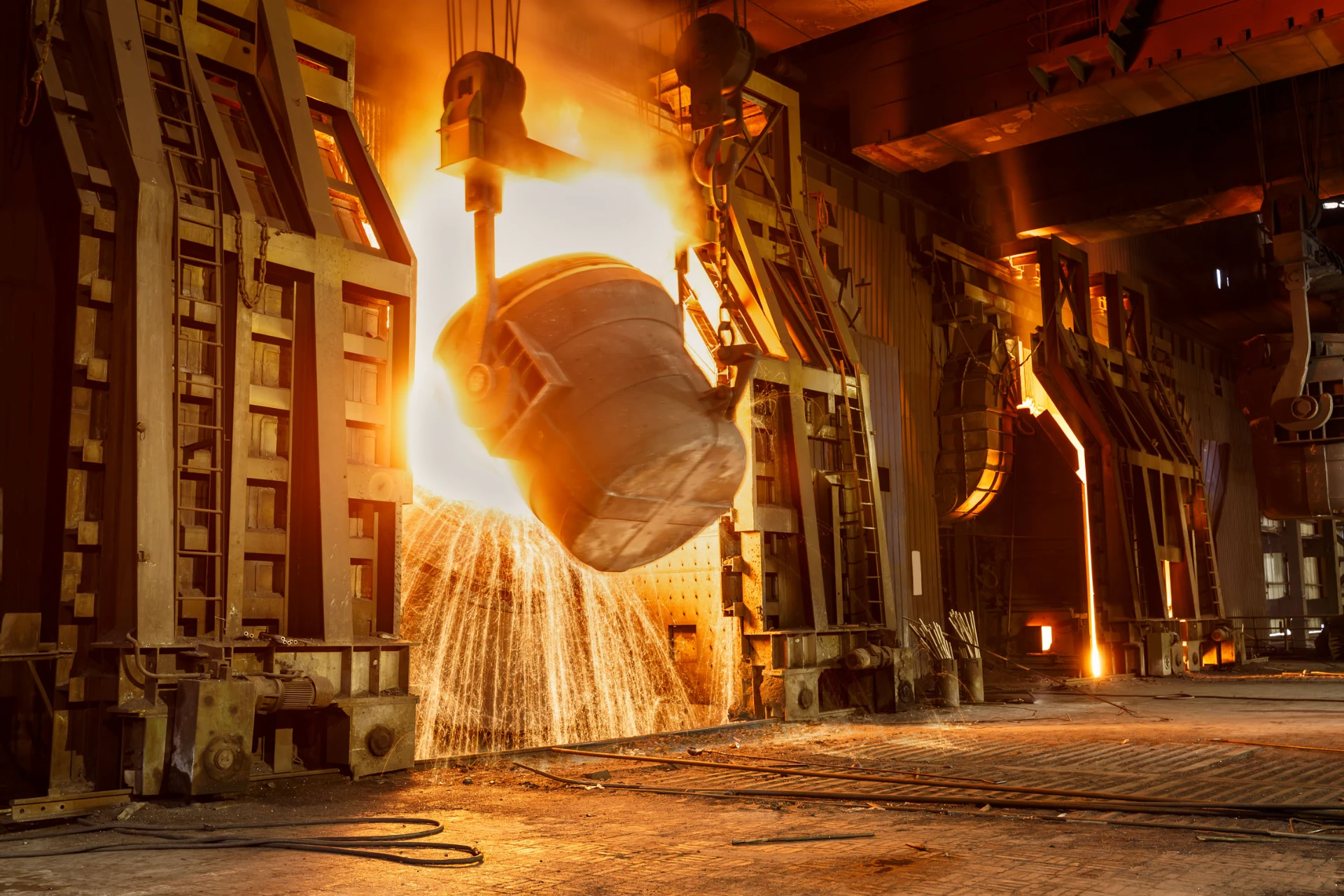
One cannot overlook the authoritative data supporting aluminum die casting's superiority in cost-effectiveness. The process's high repeatability minimizes waste, while the durability of aluminum moldings extends the lifespan of each component produced. From an economic standpoint, these factors significantly reduce manufacturing costs, offering a competitive edge to companies leveraging this technology.
Trustworthiness in aluminum die casting is largely built upon its reputation for delivering consistent results in fast-paced production environments. High-level quality assurance protocols ensure each casting meets stringent standards, backed by years of empirical evidence demonstrating the technique's reliability. For industries that thrive on timely deliveries and consistent product quality, aluminum die casting is an unmatched solution, offering a balance of efficiency and durability.
al die casting
Emphasizing real-world experiences, let us consider the automotive industry, where aluminum die casting plays a pivotal role. Here, aluminum components are utilized in various parts, including engine blocks, transmission cases, and structural components. Experienced professionals in automotive engineering testify to significant improvements in fuel efficiency and vehicle performance as a direct result of utilizing aluminum die-cast parts. Similarly, the aerospace sector leans heavily on the method for its ability to maintain structural strength while drastically reducing component weight — a critical factor in fuel consumption and range in aircraft.
Simultaneously, the consumer electronics industry has witnessed transformative impacts due to die casting, using it extensively to create compact, lightweight casing solutions that ensure durability and heat dissipation. Expert engineers in electronics manufacturing often point out the versatility and adaptability of aluminum die casting, which allows for rapid prototyping and seamless transitions to mass production, greatly enhancing time-to-market strategies.
Industry studies repeatedly underscore aluminum die casting's status as a change agent in sustainable manufacturing practices. The aluminum used is highly recyclable, making it an environmentally friendly option. Manufacturers with sustainability commitments find aligning their practices with green initiatives easier with aluminum die casting at their disposal. Furthermore, the long-lasting nature of die-cast components means reduced frequency in the replacement of parts, which translates to decreased environmental impact over the product's lifecycle.
In conclusion, aluminum die casting remains a critical technology in the manufacturing sector, praised for its combination of efficiency, reliability, and economic viability. Its continued evolution promises even greater adaptability and precision, as advancements in tooling and automation open new horizons. For industries seeking innovative, sustainable solutions that do not compromise on quality or performance, aluminum die casting emerges as an invaluable asset, reinforcing its position as an essential pillar in modern manufacturing.