Sand casting is a versatile and cost-effective manufacturing process used to create metal parts with intricate shapes. Its utility spans across numerous industries, from automotive to aerospace. Understanding the materials used in sand casting can significantly enhance production efficiency and product quality. In this article, we delve into the essential materials for sand casting, focusing on experience, expertise, authoritativeness, and trustworthiness.
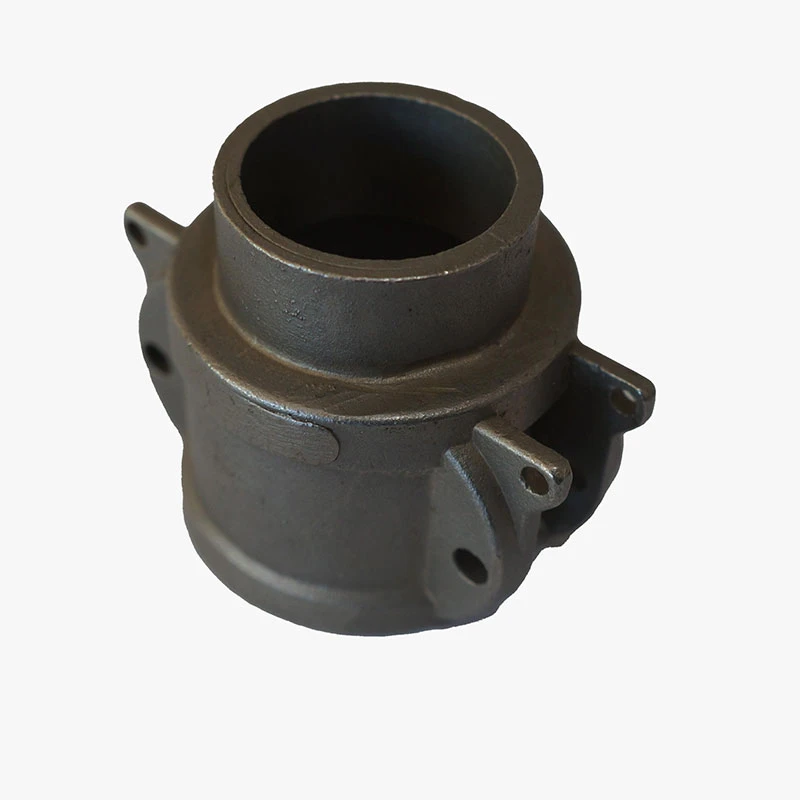
The primary material used in sand casting is sand, serving as the mold material. There are various types of sand, but the most commonly used are silica, olivine, chromite, and zircon sands. Silica sand is highly favored due to its excellent refractory properties, abundance, and cost-effectiveness. It can withstand the high temperatures of molten metal without breaking down. However, its primary concern is the health hazard in the form of respirable crystalline silica, making safety a crucial concern.
Olivine sand, with its high thermal stability and low thermal expansion, offers better dimensional accuracy and surface finish, albeit at a higher cost. Chromite and zircon sands provide exceptional thermal conductivity and refractory properties. Chromite, being heavy and expensive, is often used in conjunction with other sands to improve the casting process's efficiency and output. Zircon sand, though costly, provides superior finish quality and is highly resistant to metal penetration, making it ideal for high-precision castings.
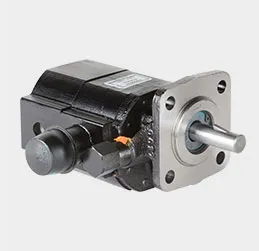
Binders play a pivotal role in the sand casting process, ensuring that sand grains adhere together, creating a solid mold. Traditionally, clay binders like bentonite are used in green sand molds. Bentonite, mixed with water, creates a strong, reusable, and easily recyclable mold. For more complex shapes or higher dimensional accuracy, chemical binders such as phenolic-urethane, sodium silicate, or furan are employed. These chemical binders offer enhanced precision and are pivotal in industries where intricate castings are necessary.
The choice of metal is crucial in sand casting and is contingent upon the intended application of the final product. Common metals include iron, aluminum, steel, brass, and bronze. Iron, particularly gray and ductile iron, is prevalent due to its excellent machinability, wear resistance, and cost-effectiveness. Aluminum, known for its lightweight properties and corrosion resistance, is extensively used in the automotive and aerospace sectors. Steel casting, while more expensive, provides superior strength, making it ideal for high-stress applications. Brass and bronze are used when corrosion resistance, electrical conductivity, and aesthetic appeal are priorities.
what materials are used for sand casting
Additives and coatings are also integral to the sand casting process, enhancing the mold's performance and the product's surface quality. Additives like coal dust, sea coal, and wood flour improve the collapsibility and surface finish of sand molds. They are carefully chosen based on the metal being cast and the casting process requirements. Coatings, typically a refractory slurry, are applied to the mold's surface to reduce metal penetration and improve the casting's surface finish. Graphite or other carbon-based coatings can be used to ensure a smooth product surface, reducing post-casting machining work.
Refractory materials, including ceramic linings, are vital for maintaining mold integrity under high temperatures. These materials protect the mold from thermal shock and erosion during the pouring of molten metal, ensuring that the castings maintain their dimensional accuracy and surface quality.
In the realm of sand casting, advancements in material science and engineering continuously influence the selection of materials and methods. 3D printing technologies are now being used to create sand molds and cores with complex geometries that were previously challenging to achieve, pushing the boundaries of design and efficiency.
For businesses looking to optimize their sand casting operations, an in-depth understanding of these materials and their interactions is critical. This knowledge ensures not only the production of high-quality products but also the efficiency and sustainability of the manufacturing process. The material choices in sand casting can significantly impact the overall success of a project, dictating the strength, accuracy, and cost of the final cast product.
In conclusion, the sand casting process relies on a symbiosis of sand, binder, metal, additives, and coatings, each selected for its unique properties and suitability for the desired application. Staying informed about the latest developments in these materials and methodologies can lead to improved product outcomes and maintain a competitive edge in the manufacturing industry.