Sand casting is a time-honored technique that has been the backbone of manufacturing in various industries for centuries. At its core, a sand casting set provides the essential tools and materials needed to create intricate metal components with precision and craftsmanship. This article delves deep into the nuances of using a sand casting set, drawing on expertise and first-hand experiences to underscore its value and application.
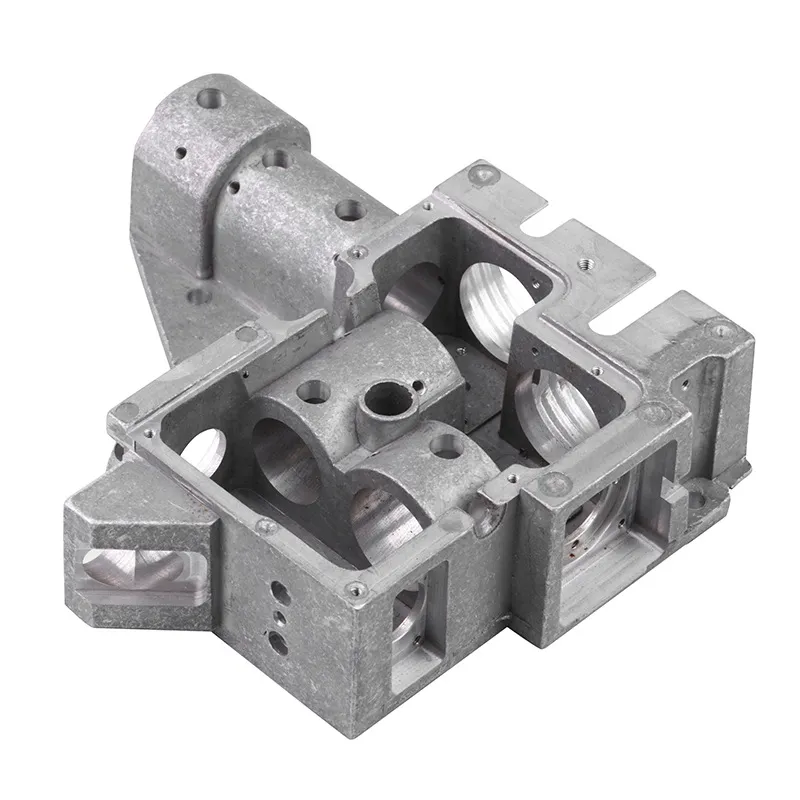
A well-equipped sand casting set typically includes a few key components a sand mold, pouring basin, gating system, and venting apparatus. At the foundational level, the sand used is usually a mix of silica sand, clay, and water, each playing a vital role in ensuring the mold's integrity and strength. Selecting the right sand is crucial, as it influences the surface finish, dimensional accuracy, and overall quality of the cast product. Premium kits often feature refined sand variations suitable for different metals and detail levels in the final product.
From an expertise standpoint, successfully using a sand casting set requires an understanding of metallurgy and thermodynamics. Each metal, whether aluminum, brass, or iron, has distinct thermal profiles and cooling rates, which affect the casting process. An expert user knows to adjust the sand composition or mold design according to these properties to prevent common defects like shrinkage or warping. For instance, aluminum's lower melting point compared to iron necessitates quicker mold transfers post-pour to maintain structural integrity.
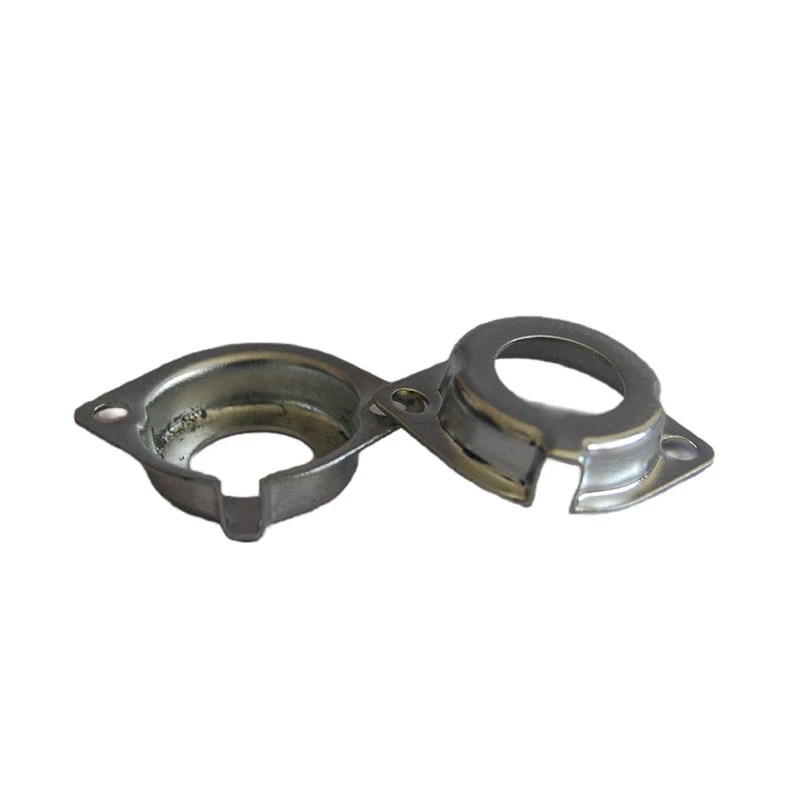
The process of sand casting begins with creating a pattern, usually made of wood or plastic, which defines the shape of the final component. This pattern is placed in a flask filled with moistened sand, which hardens around the pattern. Removing the pattern leaves a cavity mimicking its shape. Crafting this pattern requires precision and a deep understanding of the product's application to ensure it withstands operational stresses once cast.
Trust in sand casting also stems from its long-standing reliability and adaptability. Clients in the automotive, aerospace, and construction industries have consistently turned to sand casting because it balances cost-effectiveness and output quality. Large batch productions can benefit significantly from this method as multiple molds can be produced rapidly and with a high degree of repeatability.
sand casting set
Safety is another critical aspect often addressed by seasoned professionals working with sand casting sets. Handling molten metal poses inherent risks, which makes understanding safety protocols paramount. Appropriate personal protective equipment, like gloves and face shields, coupled with a comprehensive knowledge of first aid, forms the bedrock of a trustworthy casting operation. Experts often stress the importance of a clean and organized workspace to prevent accidents and maintain high operational standards.
While basic sand casting sets are suitable for beginners, professionals seeking expertise might invest in advanced setups featuring automated mold-making machinery and induction furnaces. Such equipment minimizes human error and optimizes the production process, although it requires a significant initial investment. The trade-off is a quicker production cycle and enhanced consistency in cast products, which, for many industries, translates into a competitive edge.
Authoritativeness in this field can be demonstrated through certifications and affiliations with industry groups such as the American Foundry Society (AFS). Membership in such organizations signals a commitment to upholding industry standards and staying abreast of technological advancements. Many experienced sand casters often contribute to workshops and seminars, sharing insights and fostering a community of continuous improvement and innovation.
In conclusion, utilizing a sand casting set effectively hinges on a blend of experience, technical knowledge, authority in the craft, and a steadfast commitment to quality and safety. As industries evolve, the timeless technique of sand casting adapts, offering consistent, reliable solutions for manufacturing challenges that demand both artistry and precision.