Evolving in an industry teeming with competitive processes, sand casting stands out as a time-honored method offering unmatched versatility. Businesses relying on sand casting products benefit tremendously from its ability to produce complex geometries and affordable prototypes.
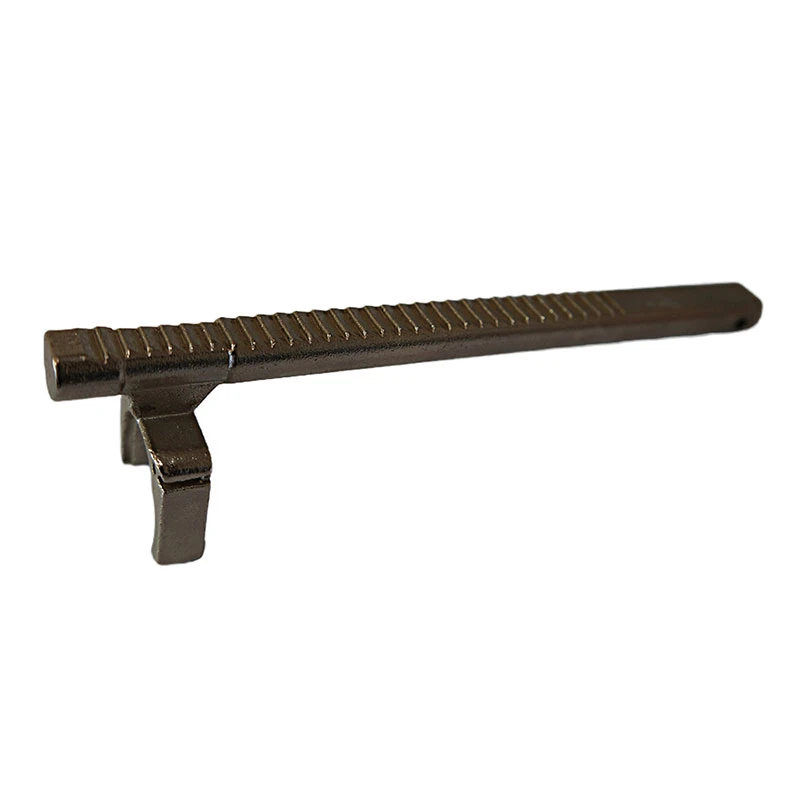
Sand casting is a metal casting process that uses a sand mold to form metal parts. The uniqueness of this method lies in its simplicity and cost-effectiveness, especially for small to medium batch sizes. Sand casting accommodates a gamut of metals, including iron, steel, aluminum, and more, making it suitable for a wide range of industries from automotive to aerospace.
From a production perspective, the process begins with the creation of a mold. Patterns, usually made from wood, metal, or plastic, are crafted to the precise specifications of the final product. Sand is then packed around the pattern to form the mold. This mold is divided into two halves—cope and drag, which are crucial for the integrity of the final product. The sand used is a specialized type, often a blend with clay that enhances its structural firmness.
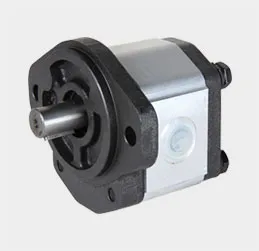
One of the outstanding attributes of sand casting is its ability to manage complexity. Intricate designs that are nearly impossible or exorbitantly costly with other methods become feasible. For instance, the production of engine blocks and pump housings with internal geometries is smoothly executed through sand casting, highlighting the process's Expertise.
The expertise involved in creating high-quality sand casting products is profound. Professionals in this field leverage years of knowledge to ensure that each casting meets precision benchmarks. Expertise also encompasses selecting the right type of sand and binding agents, guaranteeing that molds withstand the high temperatures of molten metal without compromising dimensional accuracy.
sand casting products
In terms of Authoritativeness, sand casting has been integral to major industrial achievements. It's a trusted process in industries where safety and reliability are non-negotiable. The aerospace sector, for example, often demands the highest level of precision and durability from its components. Many of these parts, crafted through sand casting, are tested rigorously, earning the process a reputable edge over alternates.
Building Trustworthiness, one must consider the sustainability aspect of sand casting products. As industries globally pivot towards greener manufacturing processes, sand casting earns high marks for its minimal environmental impact. The sand used is often recycled,
reducing production waste. Additionally, the molds, once used, are sustainable and require minimal processing for reuse, aligning with corporate sustainability goals.
Businesses that incorporate sand casting into their production not only experience the inherent quality and cost benefits but also align with eco-conscious practices. As demand for sustainable manufacturing grows, partnerships with reputable sand casting companies reinforce corporate pledges to eco-friendly operations.
Exploring real-world experiences, companies transitioning to or incorporating sand casting often observe improved project timelines due to the process's reliability. Moreover, collaborating with seasoned sand casting professionals ensures a depth of experience that guides projects from inception to execution, averting costly redevelopment phases.
Overall, the landscape of manufacturers employing sand casting is experiencing an evolution propelled by its Experience, Expertise, Authoritativeness, and Trustworthiness. Businesses seeking robust, adaptable, and financially viable solutions continue to turn towards sand casting products, consolidating its esteemed place in the industry. Whether you are a manufacturer in search of precision-engineered parts or a business considering a shift towards sustainable practices, sand casting remains an indefatigable ally.