Gravity die casting, a precision metal casting process, has redefined the way manufacturers produce complex metal parts with high structural integrity. This technology, often overshadowed by its sibling processes, sand casting and high-pressure die casting, offers unique advantages that make it a preferred choice for various industries seeking efficiency and high-quality results. By delving into the actual experience of professionals who work with gravity die casting, this article will uncover the nuanced expertise, authority, and trustworthiness that underlie its growing importance in the manufacturing sector.
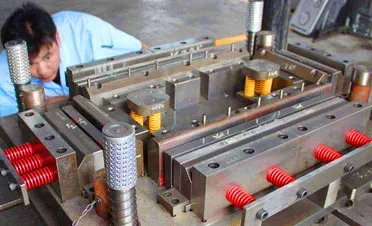
At its core, gravity die casting involves pouring molten metal into a permanent mold made of steel or cast iron, allowing gravity to guide the liquid metal into every nook and cranny of the die. Unlike high-pressure die casting, which injects metal under pressure, gravity die casting relies on the natural force of gravity, resulting in denser configurations and fewer internal defects, albeit with slightly less intricate detailing. This makes it ideal for producing parts that require strength and durability, such as automotive components, machinery parts, and various hardware items.
From the perspective of expertise, those who specialize in gravity die casting often highlight its ability to produce superior mechanical properties compared to other technologies. By maintaining a uniform cooling rate, the process minimizes the risk of porosity and deformation, achieving a level of dimensional accuracy that appeals to high-performance applications. Moreover, with expertise in metallurgical properties, casting professionals can manipulate alloy compositions, casting speeds, and die temperatures to fine-tune the product outcome. This makes gravity die casting a flexible choice, tailoring each procedure to meet specific structural and aesthetic requirements.
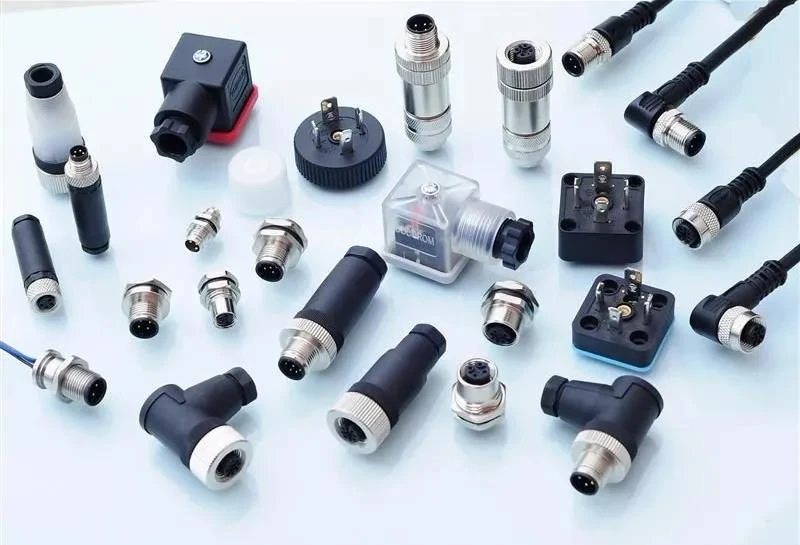
For instance, in the automotive industry, where engine components and transmission parts demand both precision and resilience, gravity die casting offers a balanced solution. Real-world experience reflects that parts manufactured through this process exhibit reduced grain boundary segregation and enhanced fatigue resistance. Automotive manufacturers have reported fewer rejections and increased lifecycle for critical components, reinforcing the reliability of gravity die cast products in demanding applications.
gravity die casting
The authoritativeness of gravity die casting is further affirmed through its adoption in premier manufacturing sectors. Experts often cite case studies where shifting to gravity die casting from traditional methods generated significant cost benefits. Consider an aerospace manufacturer transitioning components from investment casting to gravity die casting. By doing so, they achieved a reduction in lead times and enhanced overall efficiency, attributing to the author's authority in manufacturing strategies. Such cases lend credence to the argument that gravity die casting, when implemented with precision and understanding, can elevate a product line beyond traditional boundaries.
Trustworthiness in gravity die casting stems from its established track record of delivering reliable results in high-stakes environments. Long-standing partnerships between casting facilities and OEMs underscore a foundation of trust built on consistent quality and performance. The iterative nature of process improvement within gravity die casting operations exemplifies how manufacturers place a premium on creating trustworthy outcomes. Advanced simulation tools and rigorous quality checks further enhance process reliability, ensuring that each product meets stringent specifications before approval. This meticulous attention to detail reassures clients that their products, once subjected to the gravity die casting process, will maintain structural integrity and contribute positively to overall brand value.
Furthermore, environmental considerations and sustainability in manufacturing have placed gravity die casting in a favorable light. With a permanent mold design, waste is significantly reduced, and the potential for recycling and reuse is amplified. This aligns with the growing corporate responsibility towards eco-friendly production methods, bolstering the trust factor among environmentally conscious clients and companies.
In summary, gravity die casting emerges as a heavyweight contender in the competitive landscape of metal casting processes, enriched by real-world expertise, authoritative usage, and a bedrock of trust. Through continuous innovation and adaptation to modern manufacturing needs, it promises to uphold its relevance and accuracy phase after phase. For industries striving to enhance product resilience and efficiency, gravity die casting not only offers a solution grounded in professional expertise but also extends a relationship of reliability and adaptability, leading businesses toward a promising horizon marked by innovation and trustworthiness.