Die casting is a precision manufacturing process that is pivotal in producing high-quality metal components for a variety of industries. One critical parameter that engineers and designers must rigorously consider is wall thickness. Achieving the optimal wall thickness in die casting is not only an engineering challenge but also a determinant of the durability, functionality, and cost-effectiveness of the final product.
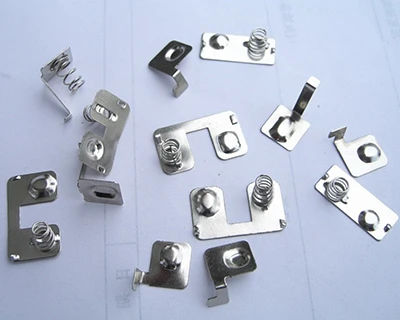
The significance of wall thickness in die casting cannot be overstated. It directly impacts several critical aspects of the manufacturing process and the product itself. Thinner walls can substantially reduce the material cost, resulting in lighter components without sacrificing strength when executed correctly. Conversely, thicker walls often offer more structural integrity and can withstand more significant stress but can increase the weight and material usage unnecessarily. Therefore, finding the balance between weight and strength begins with understanding the project's requirements and the material's characteristics.
Material selection plays a fundamental role in determining the appropriate wall thickness. Different metals and alloys offer varying levels of strength, ductility, and heat conductivity. Aluminum, for instance, is renowned for its strength-to-weight ratio, making it a preferred choice in automotive and aerospace applications. Manufacturers often aim to minimize wall thickness to leverage aluminum's lightweight properties while maintaining robustness. Similarly, zinc alloys provide excellent fluidity and strength, allowing engineers to design ultra-thin walls for intricate components.

However, designing with thinner walls involves more than material choice; it requires a deep understanding of die casting dynamics and advanced simulation software. Thin walls cool rapidly, which can lead to incomplete fillings or cold shuts if the parameters are not meticulously controlled. Engineers use sophisticated computational tools to simulate the flow of molten metal, optimizing the gate design and placement to ensure even distribution and minimal flow turbulence.
Machine specifications and tool design further influence achievable wall thicknesses. High-precision machines capable of substantial injection pressures are essential for consistent results with fine-tolerance specifications. The tooling itself, typically crafted from hardened steel, must be meticulously crafted and maintained, considering the potential for erosion and thermal expansion during repeated cycles.
die casting wall thickness
Experience has shown that design complexity often impedes achieving optimal wall thickness. Complex geometries can inadvertently lead to sections with varying thickness, creating potential weak points. A streamlined design approach, emphasizing uniform wall thickness and simple shapes, often yields the best results, enhancing manufacturability and structural performance.
Professional expertise is crucial in navigating these considerations. Expert collaboration across disciplines – involving material scientists, mechanical engineers, and tooling specialists – ensures that thickness specifications are realistic and achievable. This interdisciplinary approach is often best exemplified in industries like automotive, where safety and performance standards demand exceptional accuracy and consistency.
For stakeholders aiming to leverage die casting's advantages, trusting an experienced manufacturer with a proven track record is essential. Look for partners with certifications that validate their processes and quality assurance systems, underlining their commitment to precision and reliability.
In conclusion, the art and science of determining the optimal wall thickness in die casting is a critical element that significantly affects the success of a product. A comprehensive approach that considers material capabilities, innovative design practices, and expert execution not only enhances the component's performance but also aligns with economic goals. As industries evolve and the quest for stronger, lighter, and more efficient products continues, mastering wall thickness in die casting remains an indispensable asset for engineers and manufacturing specialists.