Aluminum die casting has become a cornerstone in the manufacturing domain, especially when cost is a crucial factor. The economic impact, combined with its efficiency, makes it an industry favorite. Yet, what exactly goes into the cost structure of aluminum die casting, and how can businesses optimize for the best results? Here, we delve into the granular details that paint a holistic picture of the costs involved and provide actionable insights to refine your approach.
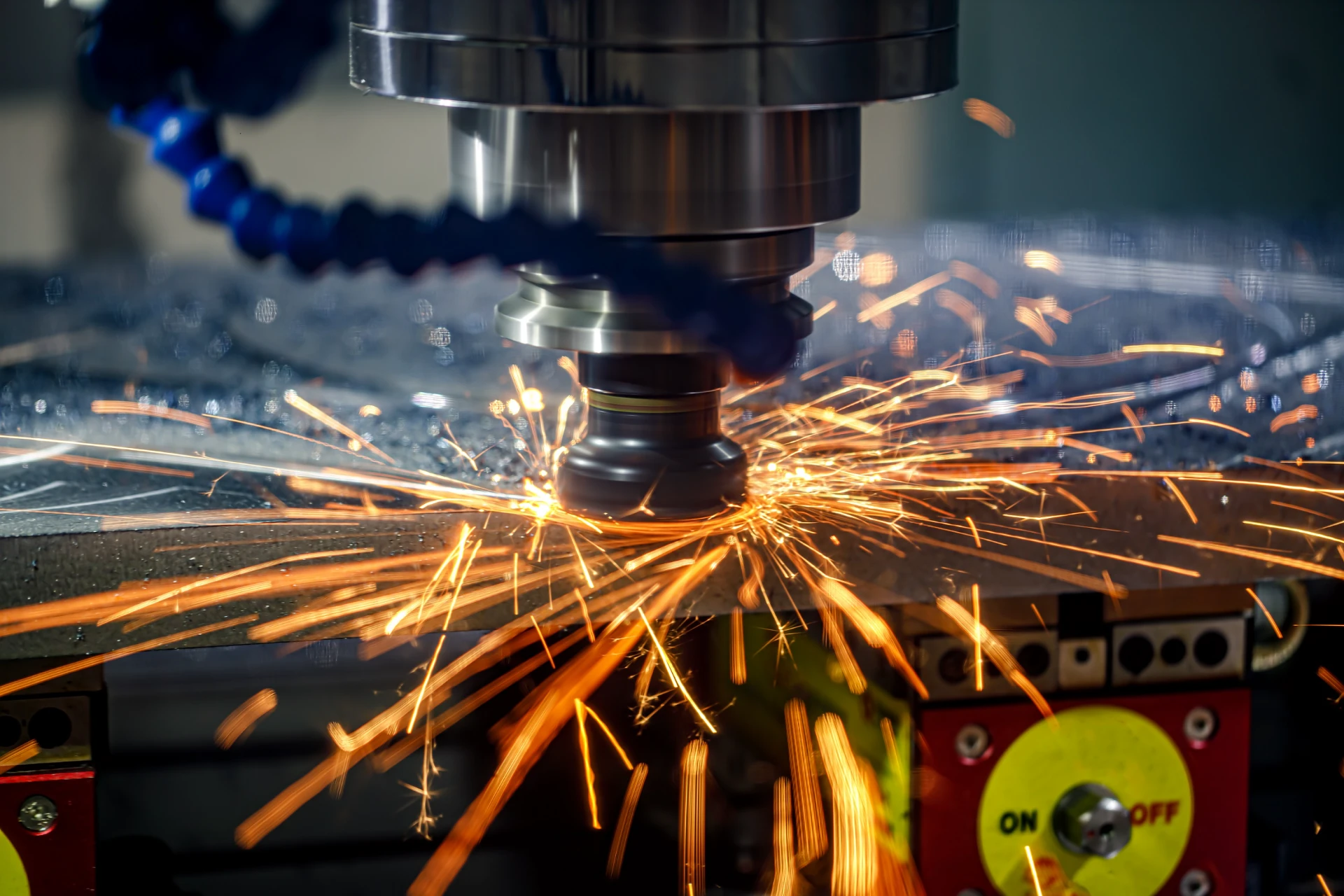
Costs in aluminum die casting are multifaceted, influenced by factors that range from raw materials to the complexities involved in the design and fabrication processes. To begin with, raw material costs for aluminum, while generally competitive, can fluctuate based on market conditions. Understanding these trends requires a keen eye on the commodity markets as well as forecasting future demands in related industries, such as automotive and aerospace, which are significant consumers of aluminum.
One hidden aspect that businesses often overlook is the design complexity of the die.
The intricacy of the design directly impacts the manufacturing cost. For customized components, engineering expertise becomes invaluable. Experienced engineers can optimize die designs to reduce excess material use and simplify production techniques, ultimately reducing costs. This process not only enhances efficiency but also extends the lifespan of the die, offering long-term savings.
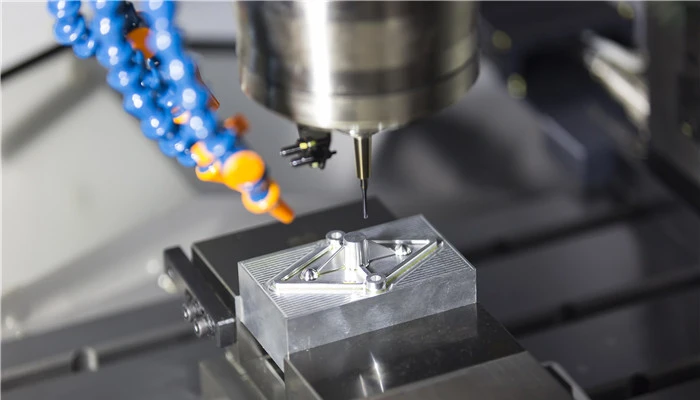
When considering operational costs, efficiency in production lines cannot be overstated. Automation and the adoption of advanced technologies, such as real-time monitoring systems, can drastically cut down on production time and reduce labor expenses. Implementing lean manufacturing principles helps in streamlining operations, thereby minimizing waste and boosting productivity. Companies investing in modern technological solutions often see a reduction in costs associated with errors and downtime, creating an immediate positive impact on overall expenditure.
Quality control is another pivotal factor that influences the cost-effectiveness of aluminum die casting. Modern casting processes benefit from rigorous quality checks at various stages, ensuring defect-free products and reducing costs related to rework. Quality assurance techniques like 3D scanning and non-destructive testing can pinpoint issues early in the manufacturing phase, allowing for quick adjustments and maintaining product integrity. This proactive approach not only secures customer satisfaction but also avoids potential financial losses from defective batches.
aluminum die casting cost
Furthermore, the environmental impact and associated costs are becoming increasingly relevant. With stricter environmental regulations, companies are encouraged to adopt more sustainable practices. Recycling aluminum scrap from the casting process can significantly mitigate costs and reduce environmental impact. Implementing an effective recycling program ensures that materials are reused efficiently and sourcing costs for new materials are kept to a minimum.
The cost of energy is an area that cannot be ignored. Die casting is energy-intensive, and fluctuations in energy prices can affect overall costs. Investing in energy-efficient machinery and technology can lead to substantial long-term savings. Moreover, companies can explore partnerships with energy providers to secure favorable rates, ensuring stability in production costs over time.
For any company involved in aluminum die casting, a strategic partnership with suppliers is indispensable. Building strong relationships with material suppliers can offer stability in raw material costs and lead to beneficial agreements, such as bulk purchasing discounts. Experienced players in the industry often recognize the value of these relationships and leverage them to secure competitive pricing.
Lastly, investment in workforce training cannot be underestimated. Skilled workers who are adept at handling modern machinery and adapting to new processes contribute significantly to reducing costs associated with errors and inefficiencies. Comprehensive training programs ensure that staff remain knowledgeable about the latest industry trends and technologies, fostering a culture of continuous improvement.
Optimizing aluminum die casting costs hinges on a balanced approach that addresses design intricacies, leverages technological advancements, enhances quality control, and fosters sustainable practices. By focusing on these areas, businesses can not only minimize expenses but also ensure high-quality production that meets industry demands.