The process of stamping plastic parts is an intricate and essential aspect of modern manufacturing, often overlooked despite its ubiquitous presence in various industries. This precision-driven technique involves creating components through the use of dedicated tooling and high-pressure equipment, and its influence extends from the automotive industry to consumer electronics. The expertise involved in stamping plastic is not simply about applying force to a material; it's about understanding the delicate balance between efficiency, precision, and material properties.
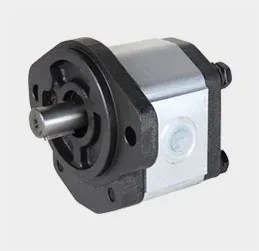
In the world of manufacturing, the crafting of plastic parts through stamping stands as a testament to engineering prowess. It is a domain where precision marries efficiency to produce consistent, high-quality components. The process begins with an in-depth understanding of the material's characteristics—polyamide, polycarbonate, and acrylonitrile butadiene styrene, for example, each present unique challenges and opportunities. The choice of material directly affects the durability, flexibility, and thermal resistance of the final product.
Expertise in this field is marked by the selection of appropriate tooling, which must be meticulously designed to handle the rigors of high-pressure applications. The dies used in the stamping process must be crafted with an accuracy that anticipates the complex shapes and intricate details required by modern designs. The interplay between the die and the plastic material is foundational, as the interaction determines not only the part's structural integrity but also its visual appeal—a critical factor in consumer satisfaction.
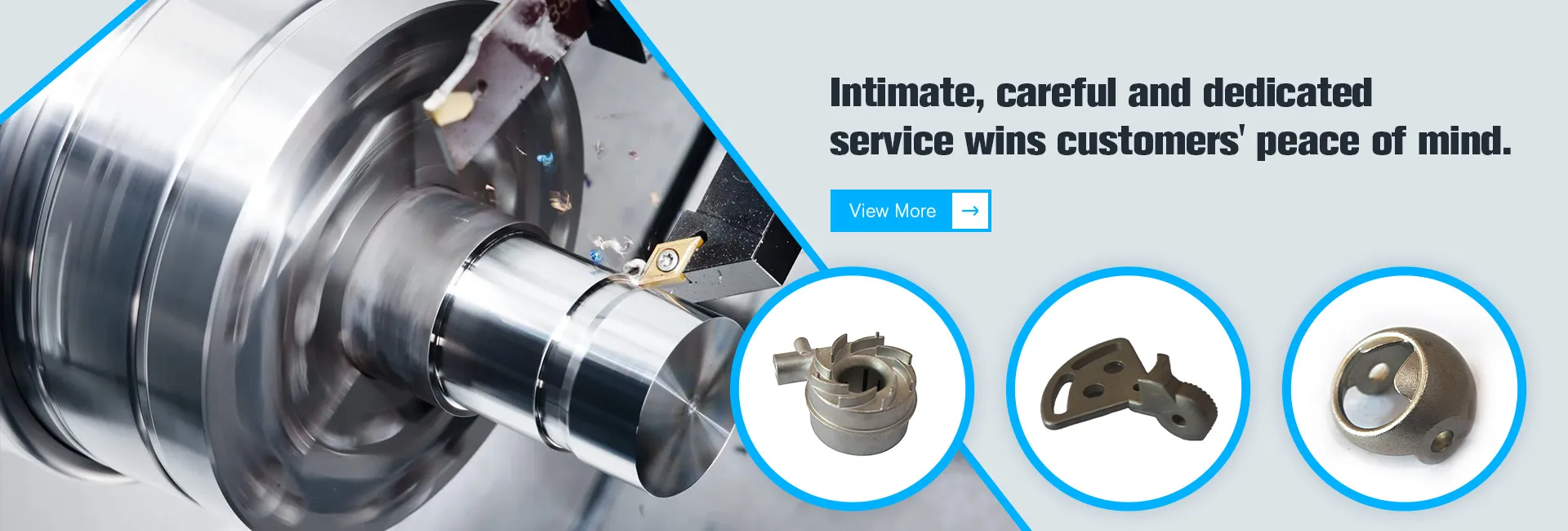
The authority of a manufacturing entity involved in stamping plastic parts is reinforced by its capacity to innovate and adapt. In an industry where consumer needs rapidly evolve, maintaining a competitive edge necessitates a commitment to ongoing research and development. This involves the integration of cutting-edge technology, such as computer-aided design (CAD) and computer-aided manufacturing (CAM) systems, which facilitate precise simulations and adjustments before any physical prototype is created. These tools not only expedite the development process but also significantly reduce the risk of defects and inefficiencies.
stamping plastic parts
Trust in the quality of stamped plastic parts is established through rigorous testing and adherence to international standards. Manufacturers must implement comprehensive quality control measures, which often include the inspection of dimensional accuracy, strength testing, and analysis of the surface finish. Certifications from recognized industry bodies further enhance trustworthiness, providing assurance to clients that the components will perform reliably in their intended applications.
Experience plays a pivotal role in refining the stamping process. Seasoned professionals bring invaluable insights gained over years of hands-on practice, enabling them to troubleshoot issues with a keen eye and swift adaptability. Their expertise often drives the development of custom solutions tailored to specific industry needs, from automotive components requiring high impact resistance to lightweight parts crucial for consumer electronics.
In conclusion, the stamping of plastic parts is much more than an industrial process; it embodies the fusion of experience, expertise, authority, and trust. These pillars uphold the reputation of manufacturers committed to delivering excellence in every component forged. As industries continue to push the boundaries of innovation, the role of stamping in shaping plastic parts remains as crucial as ever, serving as both a backbone of production and a beacon of engineering excellence.