Sand in Cast Products Innovating Beyond the Ordinary
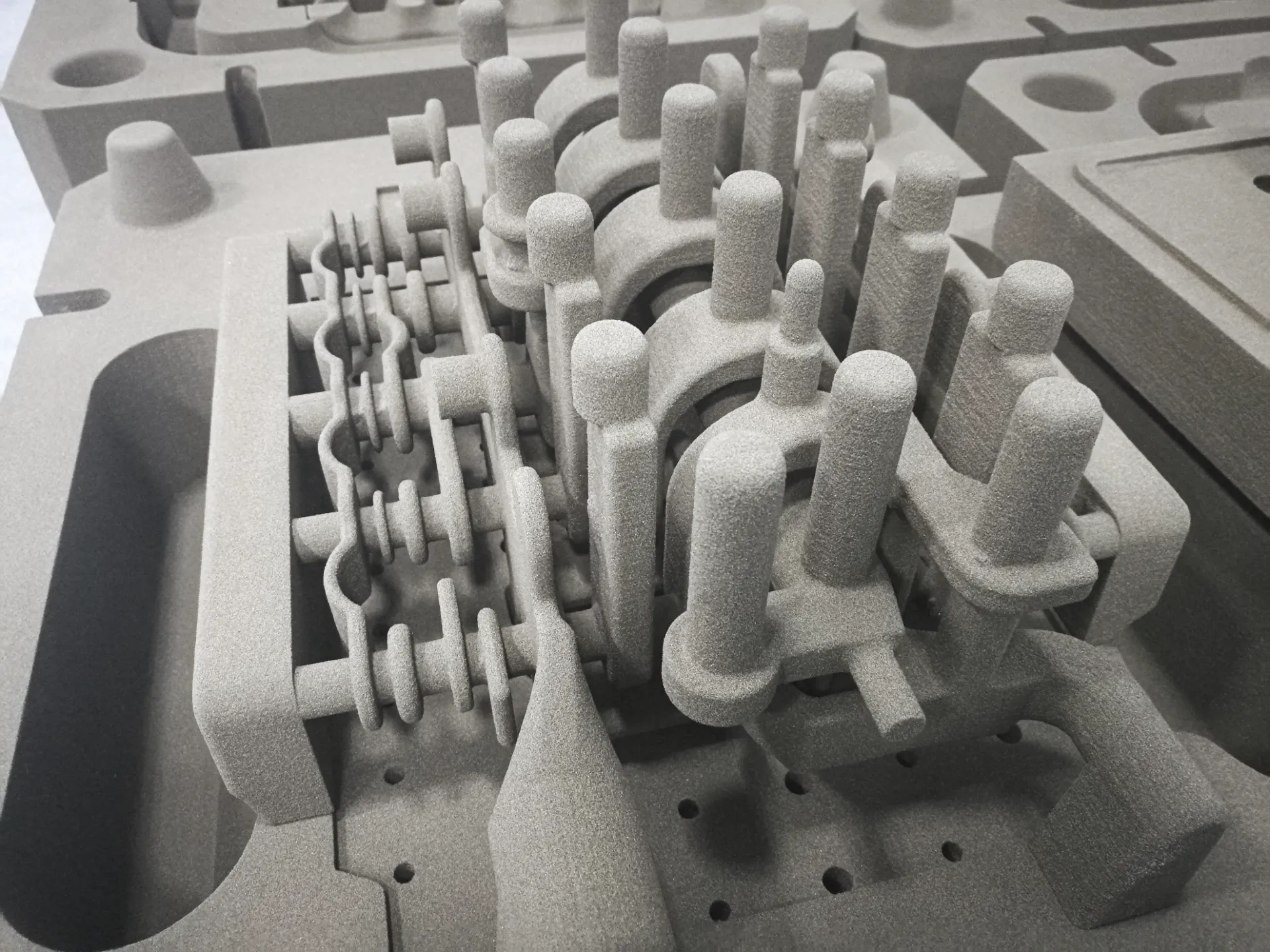
In the multifaceted world of construction and manufacturing, sand in cast represents a cornerstone in precision and innovation.
As an essential aspect of casting, sand assists in creating molds that bring complex designs to life. This topic, though seemingly traditional, embodies a blend of Experience, Expertise, Authority, and Trustworthiness, making it indispensable in various industries.
Sand casting remains a go-to methodology for manufacturers due to its cost-effectiveness and versatility in producing complex geometries. In industries requiring precision, whether automotive, aerospace, or art, mastering sand in cast is both a skill and an art.
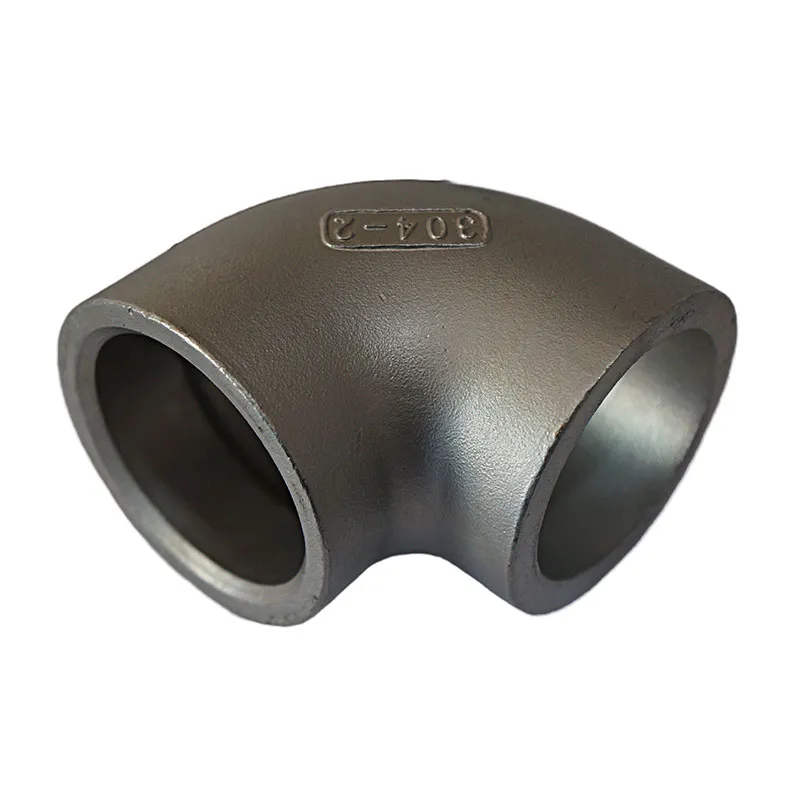
Experience Crafting Perfection with Sand
Practitioners of sand casting understand that it's not merely about pouring metal into a mold; it's about the intricate planning that precedes this process. Using sand in cast involves selecting the right type of sand—usually silica—combined with binders to hold the shape. This mixture's experience-driven formula ensures that the mold withstands the molten metal's heat and pressure.
Operators who’ve dedicated years to craft know that moisture content and sand grain size significantly influence the final product’s integrity and finish. Every manufacturer develops a unique recipe tailored to specific projects, reflecting deep-seated expertise accrued over countless cycles of trial and refinement.
Expertise Engineering Precision with Sand Choices
Choosing the correct sand type and processing method requires an understanding inherent to experts. For instance, Green Sand, a combination of silica sand, clay, and water, is favored for its adaptability and recyclability. Conversely, Resin Sand Casting, involving pre-coated sand, offers superior surface finish and detail, vital for more intricate designs.
sand in cast
Experts employ techniques such as compactibility testing and permeability measurement to optimize sand performance, ensuring minimal defects like air pockets or fractures. Using technology, like computer-aided design (CAD) and 3D printing, experts simulate and adjust parameters to achieve perfection in products ranging from engine blocks to artistic sculptures.
Authoritativeness The Keystone of Reliable Productions
The authority in using sand in casting is evident in industries where precision dictates performance and safety. Automotive manufacturing, reliant on high-quality engine components, trusts sand casting for its ability to reproduce precise dimensions consistently. Furthermore, reputable casting facilities frequently undergo rigorous certifications and adhere strictly to standards like ISO quality management, bolstering their authoritative status in the industry.
Similarly, partnerships with institutions for research and development drive innovations that perpetuate the authority of sand casting professionals. These collaborations have produced significant advancements, such as reduced emission binders, showcasing the influential role of authority in sustainable production.
Trustworthiness Building Confidence in Every Cast
The trustworthiness of sand casting arises from its proven track record over centuries. Companies that master this technique consistently deliver components that meet or exceed quality expectations, establishing long-term client relationships. Transparency in process and open communication with clients about expectations and limitations reinforce this trust.
Moreover, the use of environmentally friendly practices, including the recycling of sand and the reduction of waste, aligns the industry with contemporary ecological standards, enhancing its reputation among eco-conscious consumers.
In sum, the utilization of sand in cast processes not only aligns excellence with practicality but also underscores a lineage of innovation and reliability. From the experienced hands crafting each mold to the authoritative standards guiding every prototype, sand casting remains a trusted mainstay of modern production. Those who delve into this arena do not merely manufacture products—they forge enduring legacies in metal and sand.