Die casting porosity is a prevalent challenge in the manufacturing industry, particularly impacting the production of high-integrity components. As a critical concern, understanding its implications and mitigation strategies is vital for manufacturers aiming to produce high-grade products. This article delves into the nature of porosity in die casting, drawing on expert insights and experience to provide a comprehensive overview.
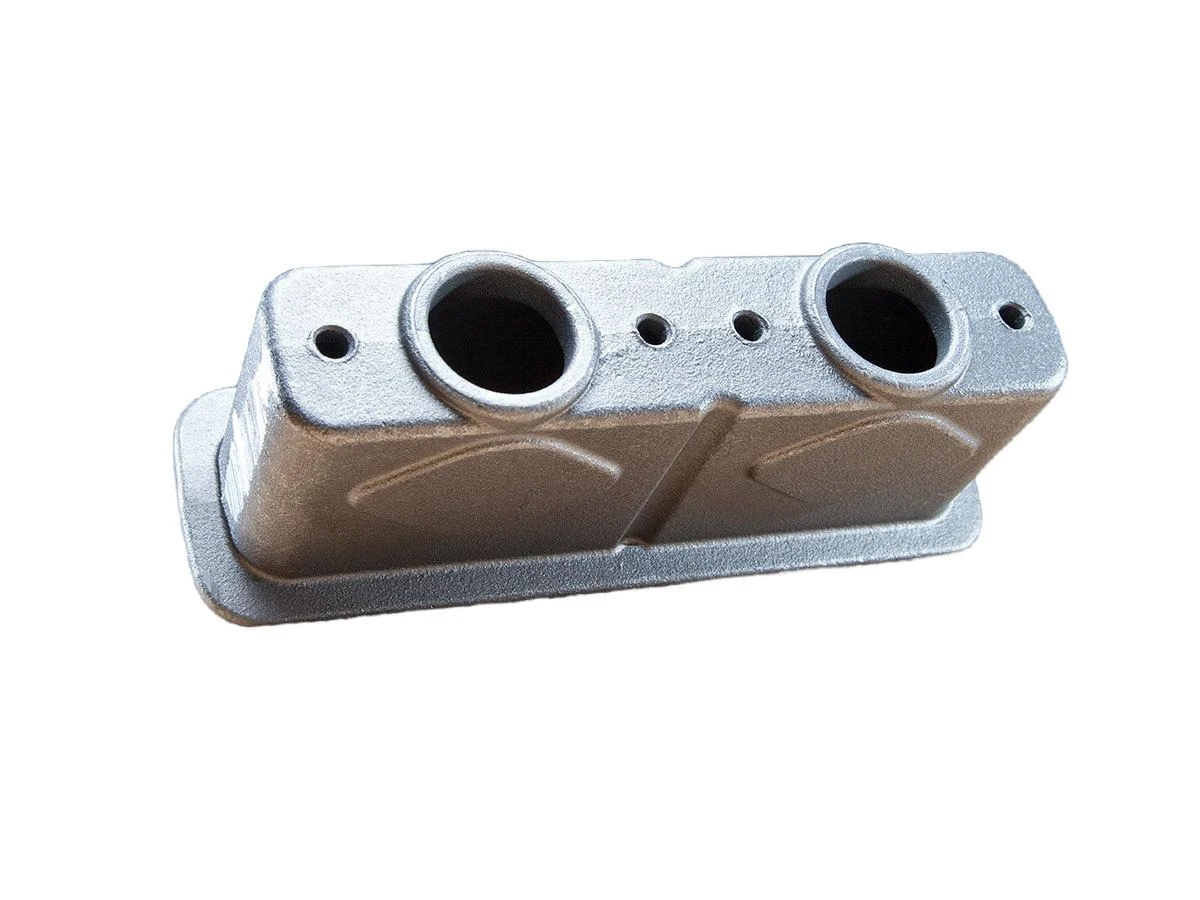
Porosity in die casting manifests as small voids or holes within the metal, often resulting from air entrapment, gas evolution, or shrinkage during the cooling process. These imperfections can compromise the mechanical properties of the final product, such as its strength, ductility, and even its aesthetic appearance. The presence of porosity is particularly detrimental to components in demanding sectors like automotive and aerospace, where material integrity is non-negotiable.
Experts in the field emphasize the importance of precise mold design and maintenance as foundational to reducing porosity. A well-designed mold ensures even flow of molten metal, minimizing turbulence which can introduce air bubbles. Furthermore, maintaining optimal temperature control is critical. Inconsistent cooling rates often lead to differential shrinkage, creating voids within the structure. Advanced computational fluid dynamics (CFD) tools are increasingly employed to model and predict these thermal behaviors, allowing for proactive adjustments in the casting process.

Professional die casters underscore the role of venting systems in combating gas porosity. Adequate venting allows trapped gases to escape during the filling process, preventing void formation. Regular inspection and maintenance of these systems are crucial. Furthermore, utilizing vacuum-assisted die casting techniques can significantly reduce gas porosity by removing air from the cavity before the metal is introduced, thus ensuring a denser and more uniform structure.
die casting porosity
Material selection also plays a pivotal role. Choosing alloys with low tendencies for gas absorption or implementing degassing treatments prior to casting can mitigate porosity. Innovative alloy development focuses on compositions that enhance fluidity and reduce gas entrapment, aligning material advancements with process optimizations for superior outcomes.
In pursuit of further reducing porosity, manufacturers increasingly turn to non-destructive testing (NDT) methods, such as X-ray and ultrasound, to detect and analyze subsurface porosity without compromising the component. This proactive approach allows quality control teams to address potential issues before products reach consumers, enhancing reliability and credibility.
Emphasizing trust through transparency, industry leaders advocate for open communication regarding the limitations and capabilities of current technologies. By setting realistic expectations and continuously striving for improvements, manufacturers can foster trust with clients and stakeholders, reinforcing their reputation as authorities in the field.
In conclusion, addressing die casting porosity requires a multifaceted approach, integrating cutting-edge technology with established expertise and rigorous process control. By prioritizing quality at every stage of production, manufacturers can ensure their products not only meet but exceed industry standards, maintaining their competitive edge in a challenging market landscape.