In the intricate realm of OEM enclosures, navigating through a landscape defined by precision and specificity, manufacturers have the formidable task of providing bespoke solutions that are innovative yet reliable. OEM, short for Original Equipment Manufacturer, plays a pivotal role in various industries, from telecommunications to medical devices, often striving for enclosures that meet the dual demands of functionality and aesthetics. Drawing from years of industry experience and technical expertise, this article delves into the nuances that define the effectiveness and success of OEM enclosures in today’s competitive market.
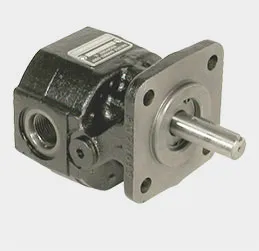
The importance of OEM enclosures cannot be understated when considering the pivotal role they play in protecting sensitive electronic components. Designed to encapsulate and safeguard, these enclosures must be crafted with meticulous attention to the environment in which they operate. For instance, an enclosure used in an outdoor weather station must be resistant to both UV radiation and moisture, whereas one used within a manufacturing plant may need to be robust enough to withstand chemical exposure and vibrations.
Expertise in material selection is a cornerstone of developing superior OEM enclosures. Advanced polymers like polycarbonate, ABS, and fiberglass-reinforced plastics are frequently leveraged due to their superior resilience and adaptability. Each material offers distinct advantages; for example, polycarbonate is revered for its toughness and transparency, making it ideal for enclosures requiring visibility of the internal components. In contrast, ABS plastic provides a perfect blend of strength and cost-efficacy, widely used across industries for its thermal stability and impact resistance.
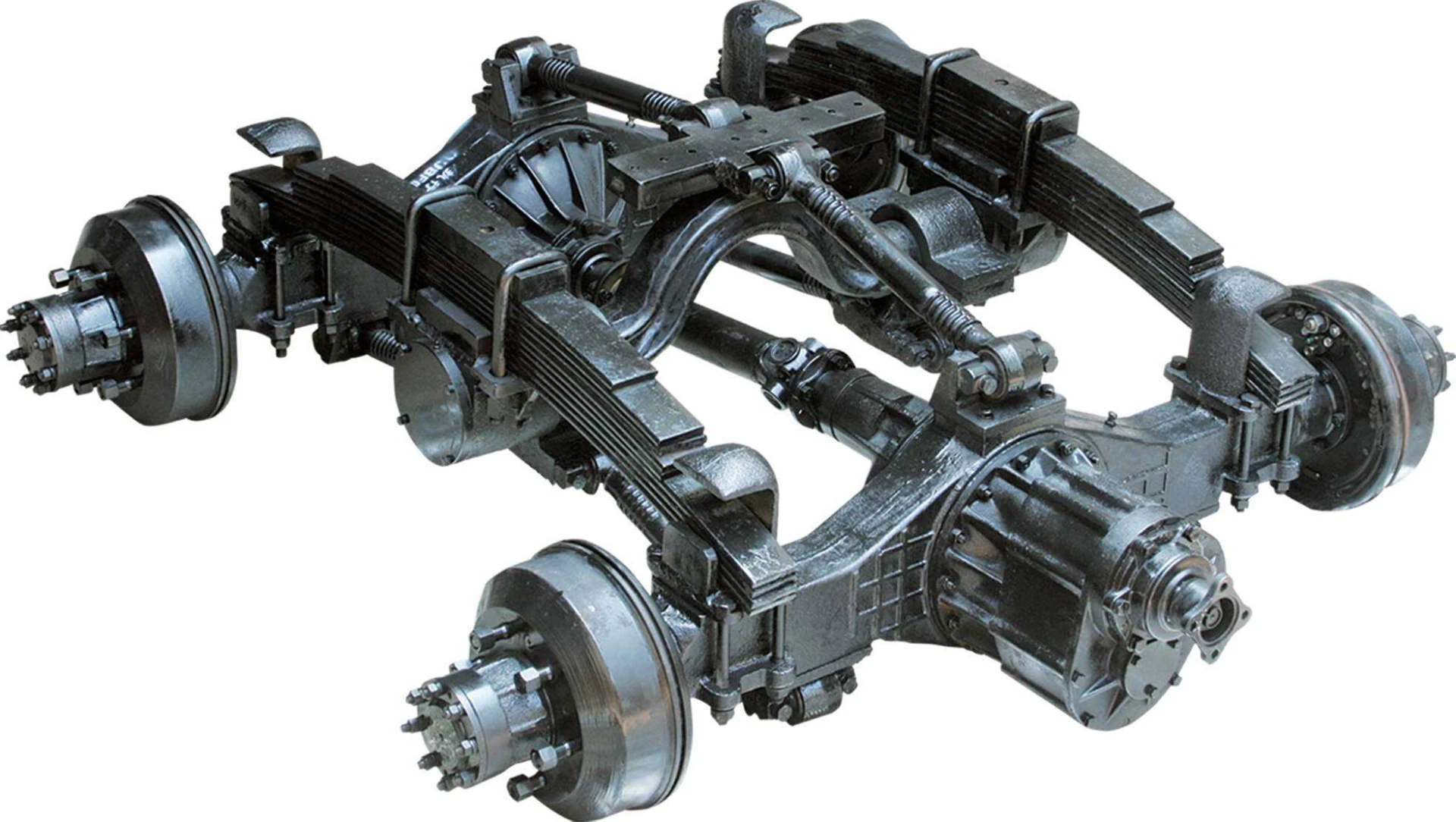
The intricate design features embedded in OEM enclosures are indispensable in ensuring operational efficiency and user-friendly interfaces. Ventilation requirements, for example, must be adeptly integrated to prevent overheating without compromising the integrity of the enclosure against external elements. Moreover, customization through precision machining and molding technologies allows for intricate designs encompassing features like EMI/RFI shielding, which are critical in maintaining device functionality in environments with significant electronic interference.
Customizing enclosures to meet specific OEM requirements involves a multi-faceted approach, employing cutting-edge technology and adhering to industry best practices to ensure compliance with international standards. Manufacturing processes now heavily rely on advanced computer-aided design (CAD), facilitating a nuanced approach to creating prototypes and eventually, the final product that can withstand rigorous testing for durability, regulatory adherence, and user safety.
oem enclosure
Authoritativeness in the production of OEM enclosures is engendered through a commitment to innovation and customization, ensuring that these components not only meet but exceed industry benchmarks. Enclosures are now frequently integrated with smart technology features, such as IoT capabilities allowing remote diagnostics and monitoring. These smart applications enhance functionality, enabling users to respond proactively to system alerts, thereby reducing downtime and maintenance costs.
Establishing trustworthiness in OEM enclosures hinges on rigorous testing protocols that diminish the margin for error. Enclosures are subjected to a range of tests, including drop, vibration, and thermal cycling tests, ensuring that they can withstand operational stresses they might encounter in real-world applications. Furthermore, environmental considerations are gaining significant traction, with manufacturers pursuing eco-friendly materials and processes to meet increasing societal and regulatory demands for sustainability.
Real-world application of knowledge in OEM enclosures comes from firsthand feedback and collaborative partnerships with end-users, ensuring that each product is a testament to quality and practicality. For example, engaging with telecommunications companies enables manufacturers to comprehend the specific challenges faced, such as the need for enclosures that can adequately dissipate heat generated by continuous operation of network equipment. Utilizing feedback and user experiences, manufacturers adapt and innovate, ensuring their enclosures are at the forefront of technological and practical advancements.
In conclusion, the intricate world of OEM enclosures is defined by industry knowledge, technical precision, and a steadfast commitment to quality. Through a synthesis of advanced materials, cutting-edge technology, and robust testing, OEMs deliver products that demonstrate their capacity to adapt and evolve with the ever-changing demands of the industries they serve. For decision-makers and engineers, selecting the right OEM enclosure is not merely a matter of preference, but an investment into reliability, safety, and performance, thereby embodying the pinnacle of expertise in product craftsmanship.