Die casting with magnesium and aluminium alloys has become integral to modern manufacturing, offering unique benefits to industries ranging from automotive to electronics. The fusion of these lightweight materials through precision casting processes improves product performance, durability, and production efficiency.
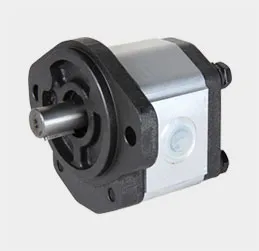
Magnesium alloys are revered for being the lightest structural materials available. Despite being silvery-white and lightweight, magnesium alloys exhibit excellent strength-to-weight ratios, which makes them suitable for applications requiring durability without added bulk. They are ideal for automotive and transport industries where every kilogram saved can contribute significantly to energy efficiency and cost reductions. Adding to their appeal, magnesium alloys offer excellent damping capacities, shielding components from vibrational damage. This characteristic enhances the lifespan of products, particularly those subject to high-stress environments.
Aluminium alloys, on the other hand, are cherished for their corrosion resistance and excellent thermal and electrical conductivity. These characteristics make aluminium die cast components particularly attractive to industries such as telecommunications and electronic devices, where reliability and performance are paramount. Furthermore, aluminium's superior thermal conductivity helps in heat dissipation, maintaining optimal temperatures in electronic device casings and thereby enhancing performance.
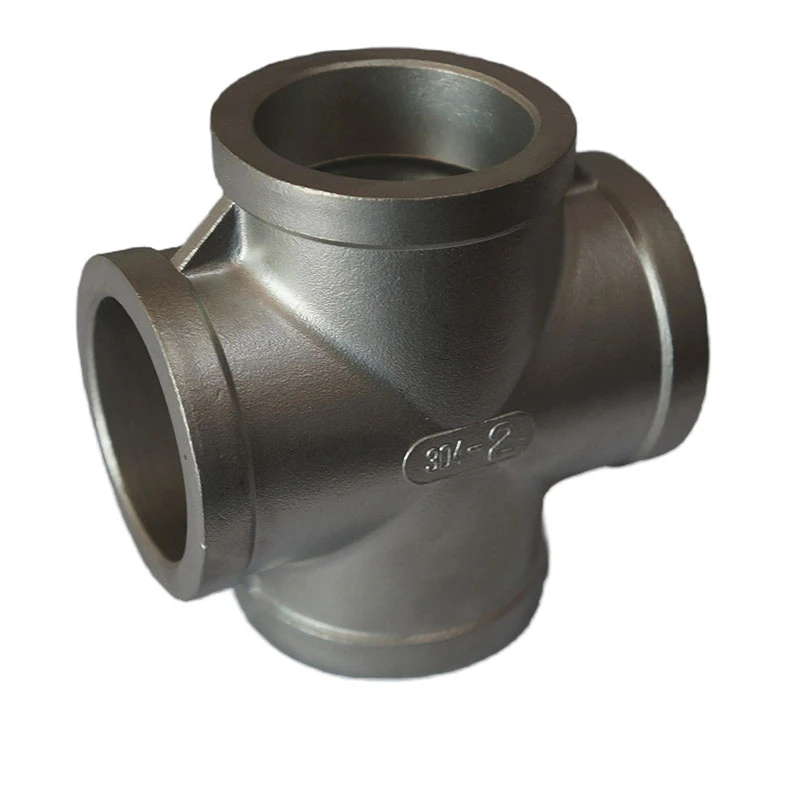
Die casting itself is a process that ensures precision and high production yield. This entails forcing molten metal under high pressure into a mold cavity. The ability to produce parts with complex geometries, tight tolerances, and fine finishes is unmatched by other manufacturing approaches. Therefore, by employing magnesium and aluminium in die casting, manufacturers can optimize parts for weight, strength, and function.
One prominent example of die casting innovation is within the automotive industry.
Vehicles use magnesium and aluminium alloy components in engine blocks, gearboxes, and frames. An embodiment of state-of-the-art engineering is the advent of electric vehicles, which demand efficiency both in weight and power management. Die-cast alloy components contribute significantly to reducing vehicle weight, thereby enhancing fuel efficiency and reducing emissions per kilometer.
Another notable application is in the electronics industry, where heat management is a critical consideration. Die-cast aluminium alloy enclosures serve this purpose effectively, offering both protection and thermal management. Magnesium’s lighter weight also finds its applications in portable electronics, where every gram saved can enhance user experience and portability.
magnesium and aluminium alloy die casting
For companies considering the integration of magnesium and aluminum die casting into their production line, understanding the material properties and potential applications is crucial. Working with trusted suppliers who hold industry certifications and have a proven track record of quality control ensures both material and process reliability. Meticulous design, which takes full advantage of the strengths and compensates for the limitations of these materials, is integral to success.
Choosing the right partner for die casting is essential. Firms should align with manufacturers that emphasize continuous innovation in casting technology, have commitments to sustainable practices, and demonstrate a strong portfolio of client success stories. An ideal partner is one that can tailor solutions to specific industry requirements, offering expertise from product development through to final manufacturing.
Moreover, advancements in technology, such as computer-aided design and simulation, have enhanced the precision of die casting processes. These innovations reduce the trial-and-error traditionally associated with casting, offering smoother transitions from concept to production. Such technological adoptions have made die casting a more appealing choice even for small-batch productions and intricate custom designs.
That said, the environmental implications of using magnesium and aluminium must not be neglected. Both can be recycled efficiently, which contributes to sustainability goals. The recycling potential of these metals fits well with the growing emphasis on environmentally responsible manufacturing practices and reduced carbon footprints.
In essence, magnesium and aluminium alloy die casting offers unmatched benefits for industries demanding light yet strong components. The promise of reduced manufacturing costs, efficient use of materials, and the potential for mass production without compromising quality makes this method highly desirable. As technological advancements continue and the pressure for sustainable practices rises, the significance of these alloys in die casting is likely to escalate further. In the landscape of modern manufacturing, staying at the forefront of alloy innovations not only assures competitive advantage but also aligns with global trends toward efficiency and sustainability.