Pressure die casting components are integral to numerous industries, offering unparalleled precision, efficiency, and durability. As an experienced professional in the field, I've had the privilege of witnessing firsthand the transformative capabilities of this process in manufacturing high-quality components that meet stringent industry standards.
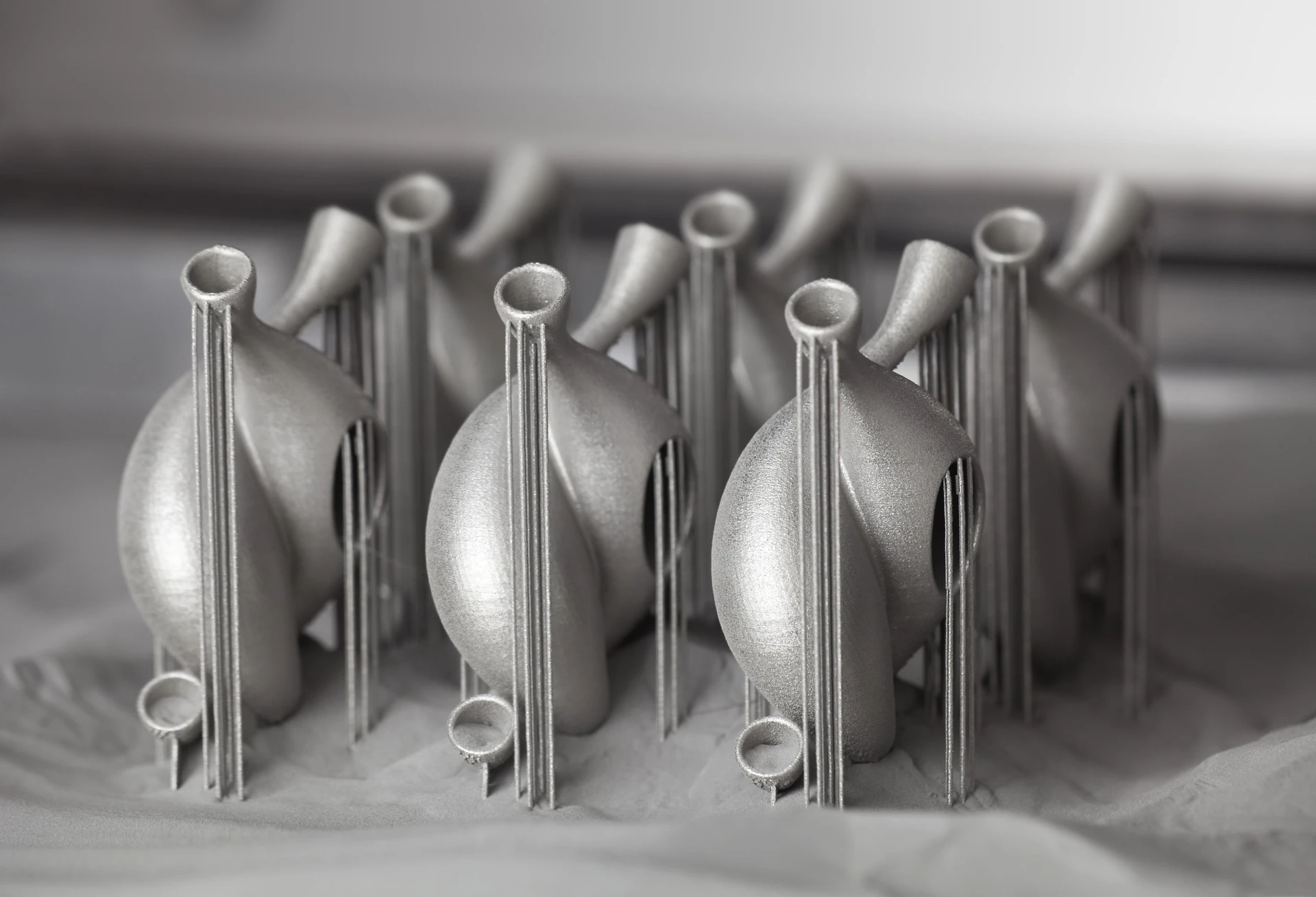
At its core, pressure die casting is a manufacturing process where molten metal is injected into a precisely machined mold cavity under high pressure. This method is particularly advantageous for creating complex shapes with high dimensional accuracy and smooth surface finishes, making it the go-to choice for industries ranging from automotive to electronics.
One of the greatest benefits of pressure die casting components is their ability to maintain consistency across large production runs. The repeatability of the die casting process ensures that each part meets the exact specifications required, reducing the risk of product failure and enhancing overall reliability. This level of precision is crucial, especially in automotive and aerospace sectors where safety and performance are paramount.
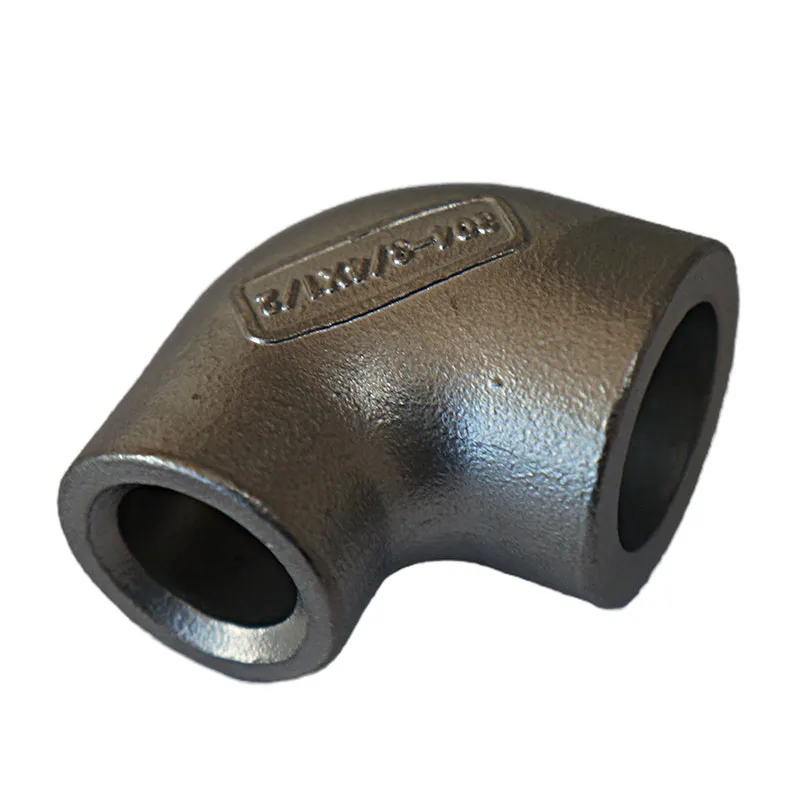
Moreover,
pressure die casting offers superior strength-to-weight ratios. This is achieved by using alloys such as aluminum, magnesium, and zinc that provide robust mechanical properties while remaining lightweight. For instance, in the automotive industry, the use of aluminum die cast components has significantly contributed to the development of lighter vehicles that are more fuel-efficient, without compromising on safety or performance.
Expertise in the design and engineering of die casting components is vital to maximizing the process's benefits. Designing for manufacturability, considering factors such as wall thickness, draft angles, and ribbing, ensures that the components are not only feasible to produce but also perform optimally in their intended applications. Collaboration with experienced die casting engineers during the design phase can lead to innovative solutions that further enhance performance and reduce costs.
pressure die casting components
Trustworthiness in the supply of pressure die casting components is another critical aspect. Collaborating with reputable manufacturers who adhere to international quality standards such as ISO 9001 can assure businesses of component reliability and consistency. The manufacturers' commitment to quality control processes, from raw material inspection to final product testing, builds confidence and long-term partnerships.
Sustainability is a growing concern in manufacturing, and pressure die casting is increasingly recognized as an environmentally friendly process. The ability to recycle and reuse die casting alloys significantly reduces waste. Moreover, advancements in technology have led to energy-efficient casting processes, further minimizing the environmental footprint.
To ensure authoritative content, it's important to highlight the continuous innovations in die casting technology. Recent advancements in simulation software, for instance, allow engineers to predict potential issues in the die casting process, such as porosity or incomplete fills, before physical trials. This capability not only speeds up the development cycle but also cuts down prototyping costs, making it a significant breakthrough in pressure die casting.
In conclusion, pressure die casting components are not just manufactured parts but crucial elements that drive progress and innovation in multiple industries. By aligning with experienced professionals, leveraging state-of-the-art technology, and adhering to robust quality standards, businesses can fully harness the potential of pressure die casting to create products that are efficient, reliable, and sustainable. Understanding these facets is what ultimately distinguishes a knowledgeable expert in the die casting industry from the rest.