In the world of manufacturing, casting pressure holds a pivotal role in the quality and integrity of metal and plastic castings. This critical process not only ensures the durability of the product but also significantly affects its performance and appearance. As manufacturers continue to innovate and demand higher standards, understanding and optimizing casting pressure becomes essential for producing superior products.
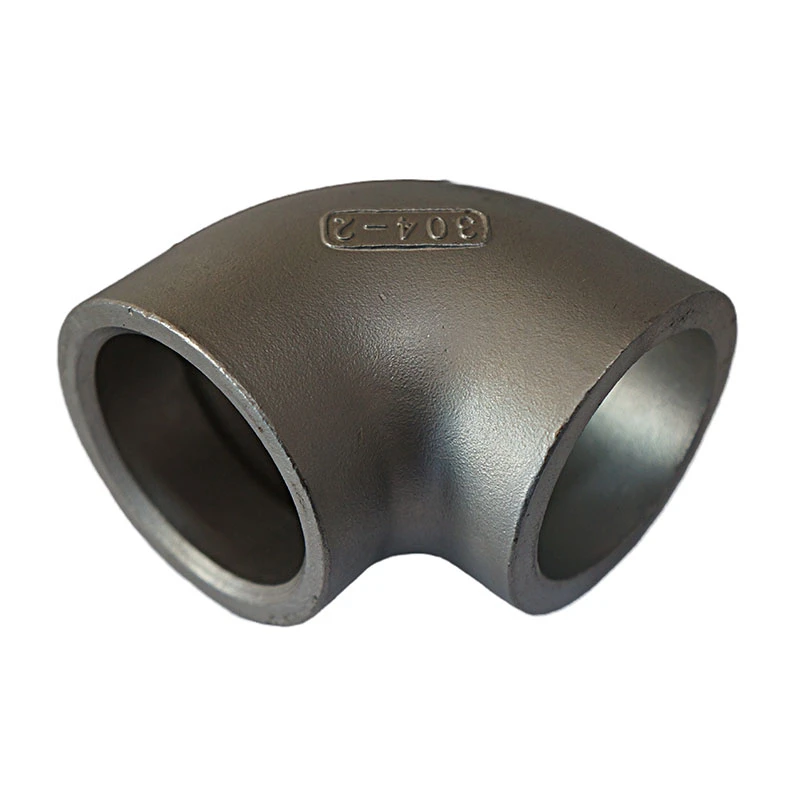
Casting pressure refers to the force applied to mold material into a desired shape. It is a balancing act of applying sufficient force to ensure complete mold filling and solidification while preventing defects such as air entrapment or uneven surfaces. The experience of seasoned professionals tells us that achieving the perfect casting pressure is an art as much as it is a science.
From an expert standpoint, the exact pressure required can vary greatly depending on the material being used. For instance, aluminum and plastics demand different pressure settings due to their distinct melting points and flow characteristics. Expertise in material properties allows manufacturers to fine-tune the casting pressure, ensuring uniformity and strength in the final product. Professionals emphasize the importance of continuous monitoring and adjustments throughout the casting process, as fluctuations in temperature and material consistency can significantly impact the final outcome.
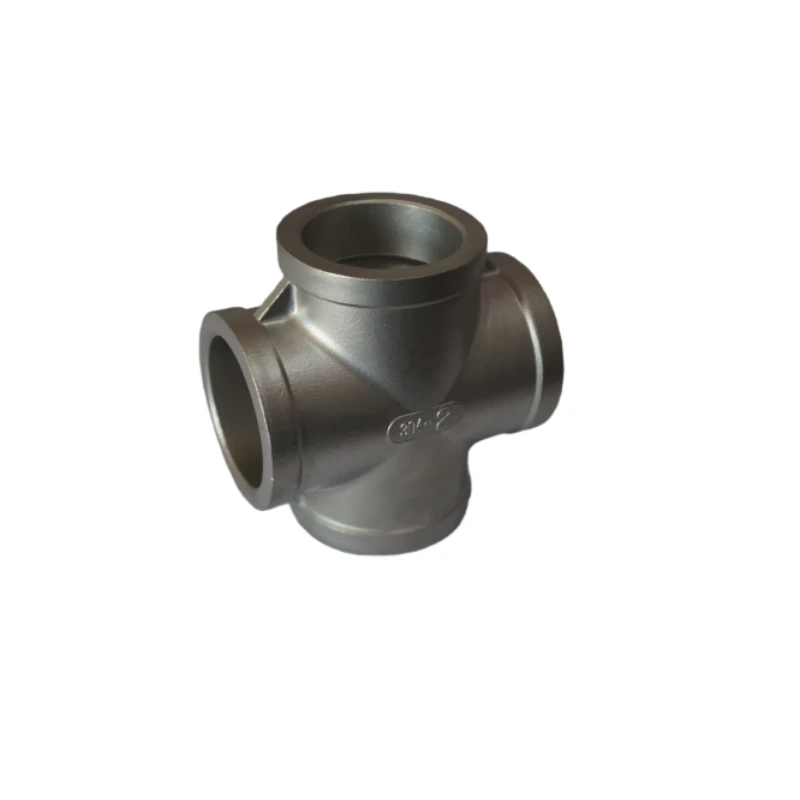
Moreover, authoritativeness in casting pressure optimization is demonstrated through the development and adherence to standardized protocols. These protocols are often the result of extensive research and experimentation, designed to tackle the specific challenges posed by different materials and product designs. Trust in these processes is reinforced by data-driven analysis and empirical evidence, which validate the efficacy of specific pressure settings and techniques.
casting pressure
Incorporating cutting-edge technology, such as computer-aided design and simulation tools, further enhances the ability to predict and adjust casting pressure parameters with precision. These technologies provide a virtual platform to test and refine casting processes before physical implementation, reducing trial-and-error and streamlining production. As a result, manufacturers are better equipped to meet stringent quality standards, reduce material waste, and enhance the overall efficiency of their operations.
Trustworthiness in the context of casting pressure derives from transparency and continuous improvement. Manufacturers who openly share their methodologies, results, and improvements foster confidence among stakeholders. Regular audits and certifications from reputable bodies also play a crucial role, providing external validation of a manufacturer’s commitment to quality and precision.
In conclusion, mastering casting pressure is not merely about achieving perfect molds; it is about embracing a culture of precision, innovation, and accountability. By leveraging experience, expertise, authoritative processes, and building trust through transparency and continuous improvement, manufacturers can significantly enhance product quality and reliability. For those involved in the production of metal and plastic castings, investing in understanding and optimizing casting pressure is paramount for staying competitive and meeting the ever-evolving demands of the marketplace.