Foundry silica sand is a pivotal component in metal casting processes across various industries. The significance of this material cannot be overstated for those who value precision, quality, and efficiency. With years of expertise in the field, this article delves into foundry silica sand's critical role in casting, its benefits, application techniques, and industry-specific experiences to empower you with authoritative insights.
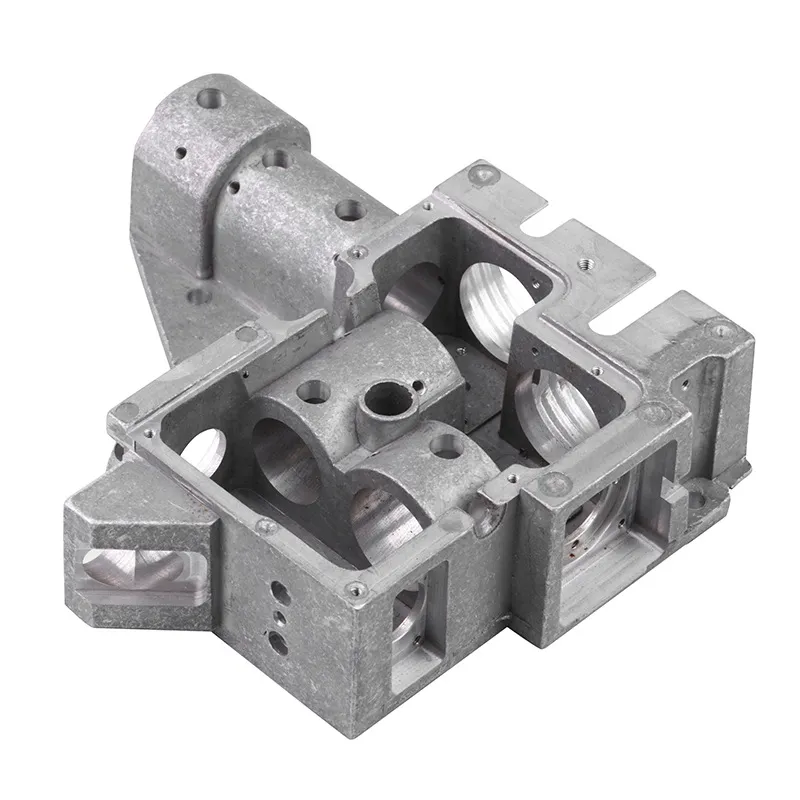
Foundry silica sand ranks as an unparalleled material in metal casting due to its high thermal resistance, permeability, and superior formability. These properties allow it to withstand the high temperatures necessary for melting and casting metals, especially iron and steel. Silica sand's ability to maintain its structural integrity under extreme conditions ensures the production of metals with impeccable surface finishes and exacting details.
The benefits of utilizing foundry silica sand extend beyond its physical properties. Its availability and affordability make it an attractive choice for foundries across the globe. The cost-effectiveness of silica sand doesn't compromise its efficiency—it contributes significantly to reducing the incidence of casting defects, thereby minimizing waste and refining production processes. Experience from seasoned professionals in the industry has demonstrated how strategic selection and application of suitable sand types can markedly optimize output quality.
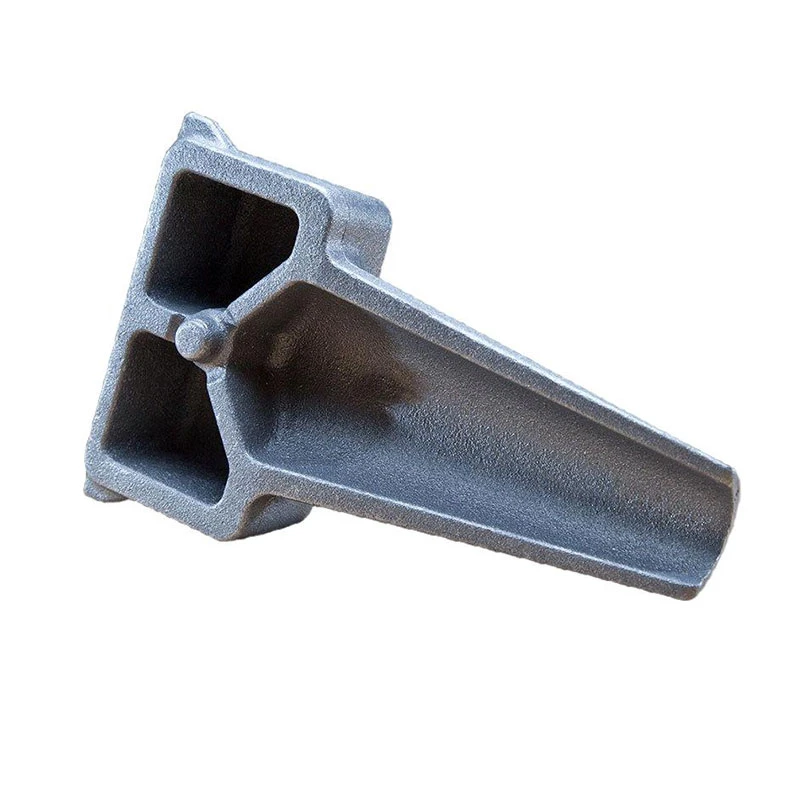
Expert handling of silica sand involves a nuanced understanding of factors like grain size, distribution, and chemical composition. For high-quality castings, the uniformity of sand grains is essential. This makes the bonding process more consistent, which directly influences the mold's durability and precision. The permeability of sand allows gases to escape during casting, reducing the risk of cavities or defects common in denser materials.
foundry silica sand
In practice, the adaptability of foundry silica sand is evident in various innovations across industries. Automotive manufacturers rely on silica sand for precision-engineered components that meet stringent safety and performance standards. Similarly, the aerospace sector benefits from its properties in producing parts that require meticulous detail and structural integrity.
To ensure optimal utilization, experts recommend regular testing of the sand’s properties and adjusting the compositions according to the specific metal to be cast and desired product attributes. Technological advancements have led to innovations in sand conditioning and recycling techniques, underlining the importance of sustainable practices within the industry. Modern foundries employ sophisticated foundry sand reclamation systems, reducing environmental impact and conserving resources, enhancing trust and legacy in sustainable practices.
Trustworthiness in foundry silica sand usage also hinges on compliance with industry standards and regulations. Material safety data sheets (MSDS) provide guidelines on safe handling practices, emphasizing the impact of regulatory frameworks like OSHA and environmental protection standards. Adhering to these norms protects workers and ensures the product's reliability, reinforcing client confidence and industry reputation.
In conclusion, foundry silica sand remains indispensable in the metal casting landscape. Its multifaceted benefits, when expertly applied, drive efficiencies and high-quality production across sectors. By fostering continuous learning and adherence to best practices, professionals can harness the full potential of this foundational material, ensuring sustainable growth and technological advancement in metal casting processes. Whether in automotive or aerospace industries, the conscientious application of foundry silica sand can catalyze next-generation innovations and profits.