Pressure die casting is a pivotal process in the manufacturing of precision metal components, widely used across various industries such as automotive, aerospace, and consumer electronics. Offering unparalleled accuracy and efficiency, the different types of pressure die casting techniques serve unique applications based on material properties, production volume, and specific industry requirements. As an expert in this domain, understanding these various processes not only enhances manufacturing efficiency but also significantly contributes to the production of high-quality components.
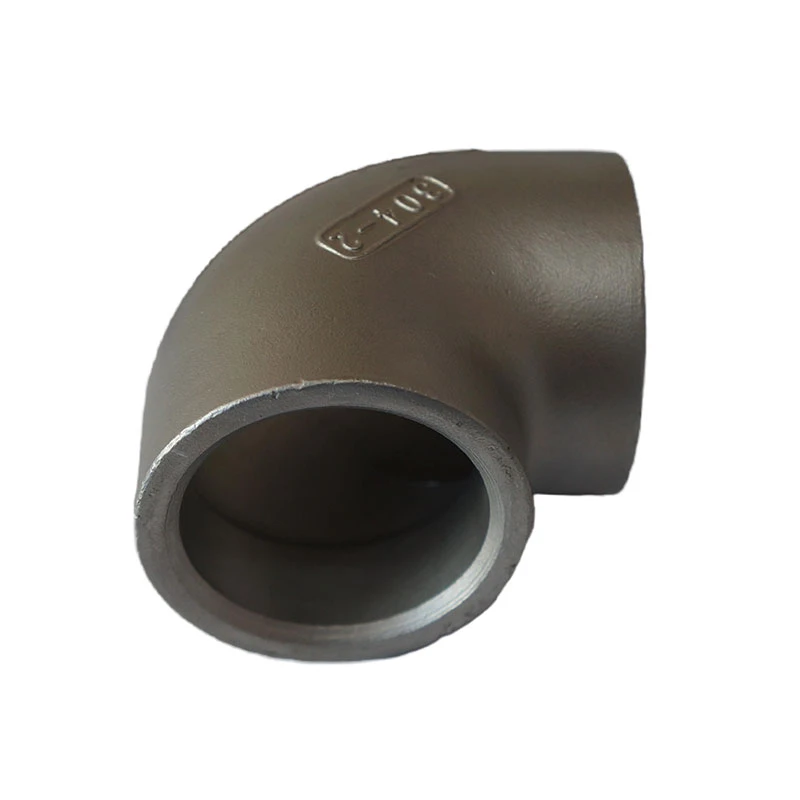
High-Pressure Die Casting (HPDC) is the most prevalent technique and involves injecting molten metal into a die cavity under extreme pressure. This method is ideal for producing intricate and high-strength components at rapid production rates, making it suitable for the automotive sector, which demands both precision and durability. Aluminium and magnesium are commonly used metals in HPDC due to their light weight and structural benefits. The high-pressure approach ensures a smooth surface finish and excellent dimensional accuracy, reducing the need for post-production machining.
On the contrary, Low-Pressure Die Casting (LPDC) involves the upward flow of molten metal into the mold cavity under lower pressure. This method optimizes the filling of the die cavity, minimizing the chances of air entrapment and resulting in components with superior mechanical properties. The LPDC technique is specifically advantageous for larger components requiring robust structural integrity, typically used in wheel manufacturing and large, durable engine parts.
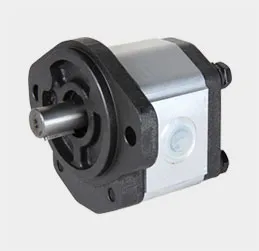
Gravity Die Casting, a traditional method in die casting, relies solely on gravity to fill the mold with molten metal. Although slower than pressure die casting methods, it is favored for producing medium-volume parts and is economically advantageous for small to medium production runs. Components manufactured using gravity die casting are typically less complex and benefit from reduced downtime and tooling costs. This method is especially effective for non-ferrous metals like aluminium and brass, enhancing the production of parts like pump housings and plumbing fixtures.
types of pressure die casting
For scenarios demanding large metal parts without incongruences in structural integrity, Squeeze Casting presents itself as an exceptional choice. Squeeze casting eliminates gas porosity, enhancing the integrity and mechanical properties of the metal component, which is particularly vital in critical applications like aerospace component manufacturing. This process merges the advantages of forging and casting, offering a refined grain structure and tremendous load-bearing capabilities.
Semi-Solid Die Casting, or thixomolding, further pushes the boundaries of precision manufacturing. Using metal in a semi-solid state, it simplifies the production of parts with complex geometries while reducing potential defects typical in conventional casting methods. This approach allows for unmatched precision in small to medium-sized component manufacturing, particularly where weight reduction without compromising strength is critical—like tablet casings and complex electronic enclosures.
Each of these die casting methods showcases unique strengths and is chosen based on the product specifications, desired material property, and economic considerations. Incorporating cutting-edge technology, like simulations and real-time monitoring, advances these processes, enhancing quality control and production efficiency—ultimately aligning product delivery with stringent industry standards.
As a seasoned professional in pressure die casting solutions, leveraging these advancements and understanding the intricate relationship between casting type, material properties, and manufacturing techniques not only ensures optimal product development but also extends one's competitive edge within the industry. Each casting method, with its particular nuance, plays a defining role in achieving precision, performance, and reliability in modern manufacturing landscapes.