Deep drawn stamping parts are ubiquitous in numerous industries, playing pivotal roles in sectors ranging from automotive to aerospace, and even medical devices. Despite their prevalence, the precision and expertise involved in creating these components remain vastly underappreciated. With an unparalleled combination of advanced technology and skilled craftsmanship, deep drawn stamping parts exemplify the forefront of metal shaping techniques.
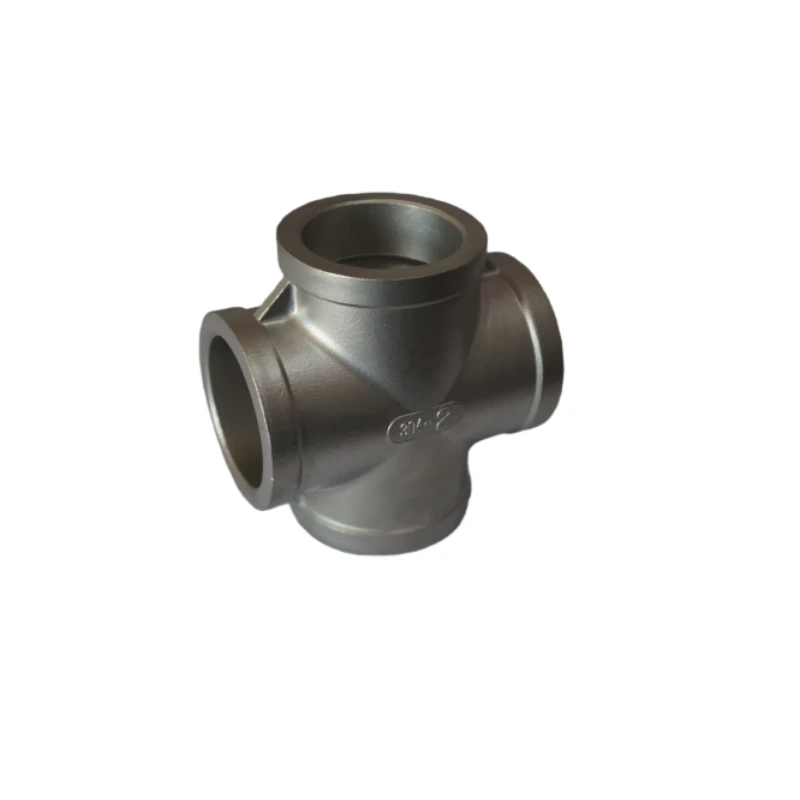
Precision and Expertise in Manufacturing
The process of deep drawing involves elongating a metal blank into a desired shape through a punch and die mechanism. This intricate process requires not only state-of-the-art equipment but also an acute understanding of material properties and design intricacies. Each component begins as a flat sheet of metal, which undergoes a transformation that demands exact precision. The ability to predict material flow and control deformation is paramount, where minute miscalculations can lead to structural weaknesses, necessitating a depth of expertise that few possess.
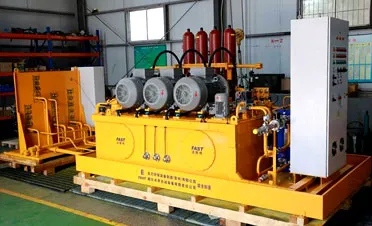
Critical Role in Key Industries
In the automotive sector, deep drawn stamping parts are integral to the production of durable, lightweight components essential for vehicle safety and efficiency. Fuel tanks, transmission components, and even intricate parts of airbag systems rely heavily on this technique. The aerospace industry similarly benefits from the high strength-to-weight ratio achieved through deep drawing, using these parts in countless critical applications including engine components and structural elements.
On a more microscopic scale, the medical field depends on deep drawn stamping for creating complex, precision components used in surgical tools and implantable devices. The high precision required in this sector underscores the critical need for expertise in the deep drawing process, as the margin for error is exceptionally slim.
Innovative Techniques and Material Evolution
Continuous advancements in technology have significantly refined the deep drawn stamping process. Today's manufacturing often incorporates computer-aided design (CAD) and finite element analysis (FEA) to simulate and predict outcomes, reducing the trial-and-error approach traditionally associated with the development of these parts. This not only enhances efficiency but also ensures the reliability of the components produced.
deep drawn stamping parts
Moreover, with the advent of new metal alloys and composites, manufacturers have greater flexibility in choosing materials that optimize performance for specific applications. The expertise required to handle these diverse materials is substantial, demanding a thorough understanding of their properties and how they behave under the stress of the deep drawing process.
Authoritativeness and Trustworthiness
In a market saturated with manufacturers, choosing a provider with verified industry credentials and experience is crucial. Trust is built through a proven track record of compliance with industry standards, rigorous testing protocols, and robust quality assurance measures. Leading manufacturers are certified under ISO and other relevant standards, ensuring that the components meet the highest benchmarks of quality and safety.
The trustworthiness of a manufacturer is further solidified by their transparency in operations and client relationships. Reliable providers offer comprehensive documentation and open channels for customer feedback, continuously improving upon the services delivered.
Sustainability and Future Directions
Sustainable practices in manufacturing have become increasingly important, and the deep drawn stamping industry is no exception. Innovations aimed at resource efficiency, such as minimizing scrap material and recycling excess metals, play a crucial role in reducing the environmental impact. Additionally, investment in energy-efficient machinery and processes demonstrates a commitment to sustainable practice.
Looking ahead, the future of deep drawn stamping parts lies in further integration of digital technologies. With Industry 4.0, smart factories equipped with interconnected machines utilizing IoT technologies will facilitate real-time data exchange, improving productivity while maintaining the precision that defines deep drawn stamping excellence. As manufacturers continue to innovate, the reliance on knowledgeable professionals will remain an indispensable aspect of this evolving field.
Deep drawn stamping parts are not merely components; they are engineering triumphs that embody the pinnacle of precision and expertise. Whether you are an engineer seeking a reliable partner or an industry analyst exploring technological evolutions, understanding the complexity and skill involved in producing these parts is essential. With advancements continually pushing boundaries,
the future of deep drawn stamping is as promising as it is fascinating.