Sand die casting is a pivotal manufacturing process that melds centuries-old craftsmanship with modern technological advancements. This technique forms a crucial cornerstone in the fabrication of metal components, contributing significantly to industries ranging from automotive to aerospace. Delve into the intricate world of sand die casting, a process celebrated for its unparalleled ability to produce highly detailed and complex metal parts with remarkable efficiency and precision.
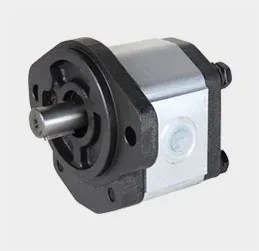
Sand die casting capitalizes on a unique combination of sand and a binding agent to create a mold that is both robust and malleable. The choice of sand is paramount, as its quality directly influences the final product’s accuracy and surface finish.
Typically, high-quality silica sand is used due to its ability to withstand the intense heat of molten metal. This characteristic, coupled with its fine grain structure, enables the creation of intricate designs and smooth finishes, ensuring products meet exacting industry standards.
The professional expertise required in sand die casting cannot be overstated. Mastery of this art necessitates a deep understanding of material properties, mold design, and thermal dynamics. Prior to commencing the casting process, experts meticulously design the mold using advanced software to simulate fluid flow and thermal gradients. Such simulations are critical in anticipating potential defects like air entrapment or shrinkage, thus ensuring optimal results. The collaboration of skilled engineers, metallurgists, and craftsmen is essential in translating these digital designs into physical molds that can sustain repeated cycles of metal pouring without significant wear.
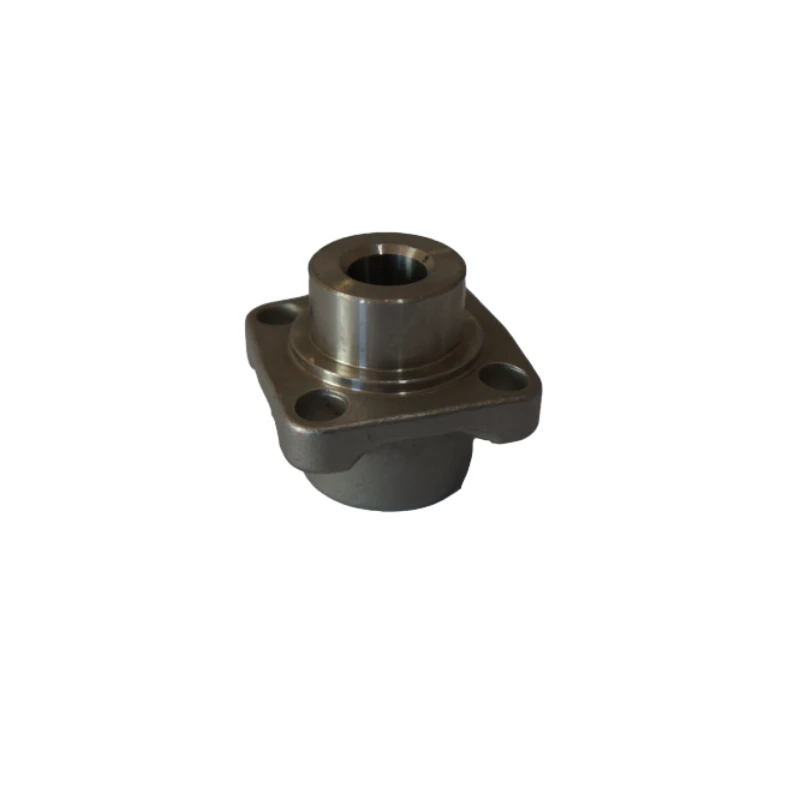
Authoritativeness in sand die casting comes not only from technical acumen but also from adherence to rigorous quality standards. The process adheres to international norms, including ASTM and ISO benchmarks, which govern aspects ranging from mold permeability to thermal expansion allowances. Organizations known for their expertise in sand die casting are typically certified and demonstrate a commitment to continuous process improvements. This dedication to quality affirms the credibility of products manufactured using this technique, instilling confidence among end-users across diverse sectors.
sand die casting
The trustworthiness of sand die casting as a manufacturing method is exemplified by its widespread adoption and the longevity of its applications. Its ability to cater to both large-scale industrial requirements and bespoke, artisanal crafting makes it a versatile solution. Industries that demand reliability and durability, like automotive manufacturing, routinely turn to sand die casting for its ability to produce strong, lightweight components that enhance vehicle performance without compromising safety. The repeatability of the process, combined with the environmental friendliness of using recyclable sand, further solidifies its reputation as a trustworthy manufacturing solution.
On the frontier of innovation, sand die casting continuously evolves, integrating new technologies to enhance accuracy and efficiency. The latest advancements include the use of 3D printing to create sand molds and cores, reducing lead times and enabling even more complex geometries. This innovation not only places sand die casting at the forefront of modern manufacturing but also affirms its relevance in an ever-evolving technological landscape.
Industries leveraging sand die casting benefit from a process steeped in historical tradition yet infused with cutting-edge advancements. The reliability, precision, and sustainability of this methodology underscore its position as a preferred choice for manufacturers aiming to balance cost-effectiveness with superior quality. Consequently, products manufactured through sand die casting are not only a testament to meticulous engineering but also to a process that inspires confidence through its proven track record of excellence.
In conclusion, the intricate dance of thermal physics and material science inherent in sand die casting is what endows it with a distinguished reputation. As industries demand increasingly complex and durable components, understanding this process and its wealth of nuances provides a significant competitive edge. The future of sand die casting lies in its adaptability, ensuring its enduring presence in the global manufacturing landscape, symbolizing a profound intertwining of tradition and innovation.