In the realm of die casting, porosity is a well-known challenge that manufacturers strive to minimize. Meeting porosity standards is crucial for ensuring high-quality products, performance, and longevity. Drawing from years of industry experience and specialized knowledge, we explore the key aspects of die casting porosity standards, offering insight and guidance.
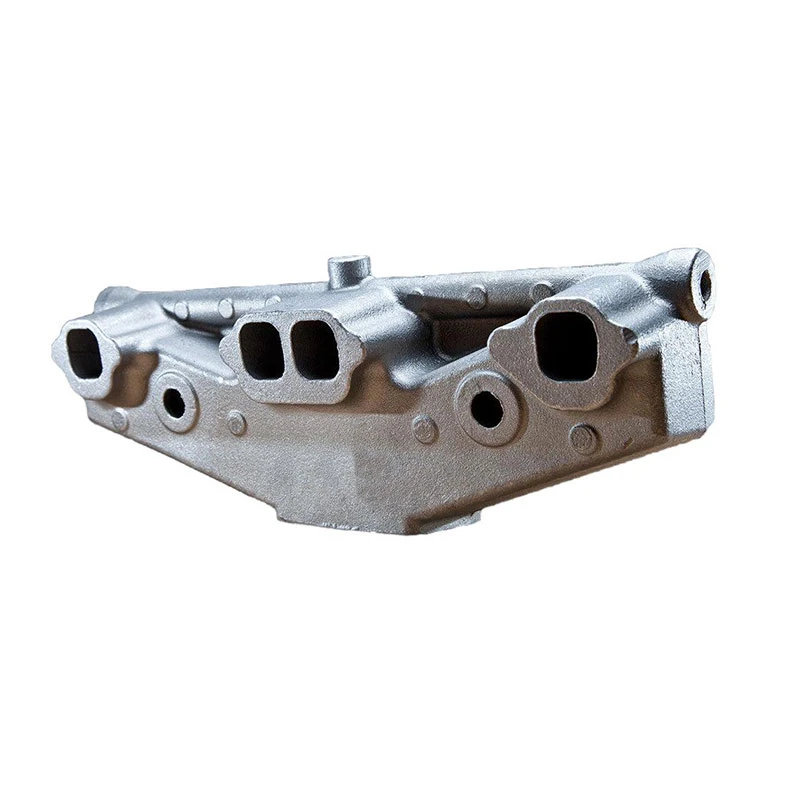
Porosity in die casting refers to small voids or holes within the metal matrix, which can occur due to trapped air, gas formation, or shrinkage during the solidification process. These hidden flaws can significantly impact the mechanical properties of the final product, leading to weakened integrity, reduced performance, and potential failure in application.
Experience has shown that understanding the root causes of porosity is vital. Temperature control during the casting process is a critical factor. Inconsistent temperatures can lead to variations in the solidification rate, promoting porosity. Another noteworthy factor is the design of the mold, which should facilitate adequate air evacuation and proper filling without turbulence.
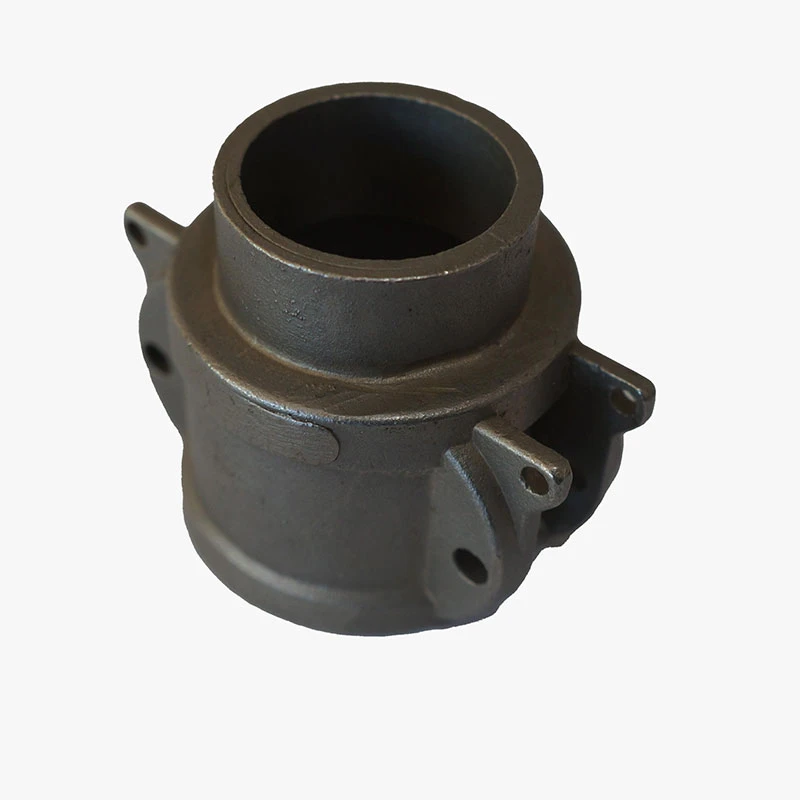
The expertise of a die cast professional involves selecting appropriate materials and adjusting the parameters based on the specific requirements of the part being cast. The choice of alloy, for instance, can influence porosity levels, as different metals have varying tendencies to trap gases. Mastery of the casting environment, equipment calibration, and post-casting treatments all contribute to meeting and exceeding porosity standards.
die casting porosity standards
In terms of authoritativeness, adhering to established porosity standards such as those set by the Society of Automotive Engineers (SAE), the American Society for Testing and Materials (ASTM), or equivalent international bodies, is essential. These standards specify acceptable levels of porosity according to the intended application and the expected load-bearing capacity. For instance, components intended for automotive or aerospace use typically have stricter porosity requirements due to the high performance and safety expectations.
Trustworthiness in addressing die casting porosity involves systematic testing and validation. Non-destructive testing methods, such as X-ray inspection or computed tomography, are critical in detecting internal voids without compromising the part. Implementing a rigorous quality assurance protocol that aligns with industry standards reassures clients of the reliability and durability of the components.
Incorporating customer feedback into the continuous improvement process is another facet of trustworthiness. Engaging with end-users to understand the practical challenges faced in the field can guide refinements in casting techniques and quality control measures. Ultimately, this collaborative approach fosters innovation and enhances the overall quality of die-cast products.
In understanding die casting porosity standards, the blend of experience, expertise, authoritativeness, and trustworthiness forms the backbone of successful practices. Manufacturers who leverage these elements not only achieve compliance with global standards but also set the stage for producing superior, dependable components that meet the rigorous demands of modern applications.