In the intricate world of manufacturing, casting and die casting are pivotal processes that revolutionize the production of complex components required across various industries. As industry demands evolve, the nuances of casting and die casting are becoming more critical, offering manufacturers unparalleled advantages in terms of quality, precision, and scalability.
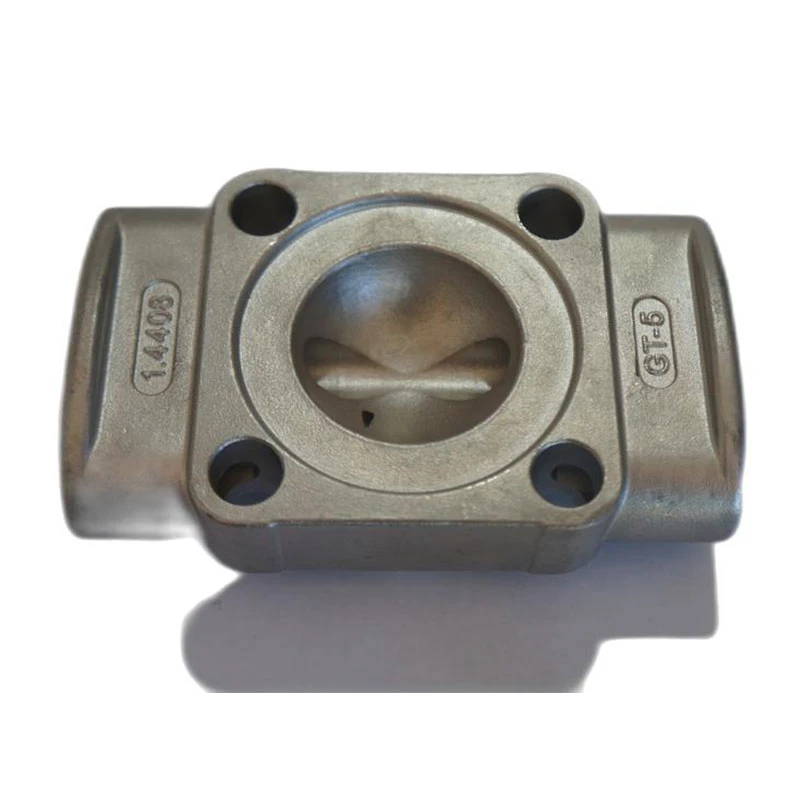
Casting encompasses various processes wherein liquid material is poured into a mold to achieve a desired shape once it solidifies. This ancient technique has gradually transformed with technology, making it indispensable for fabricating large complex parts with enhanced strength and reduced material waste. Particularly in sectors like automotive, aerospace, and heavy machinery, casting is invaluable for creating parts such as engine blocks, transmission cases, and machinery components with intricate geometries and precise specifications.
Die casting, a subset of casting, employs high-pressure techniques to inject molten metal into a mold cavity. Distinguished by its efficiency and ability to produce detailed parts with high dimensional accuracy, die casting is prevalent in the manufacturing of components where a smooth finish and high strength are critical. It offers significant advantages over other methods, including reduced machining, excellent repeatability, and the production of thin-walled parts that are lightweight yet durable. This makes die casting an optimal solution for electric vehicles, consumer electronics, and other sectors requiring high-performance materials.
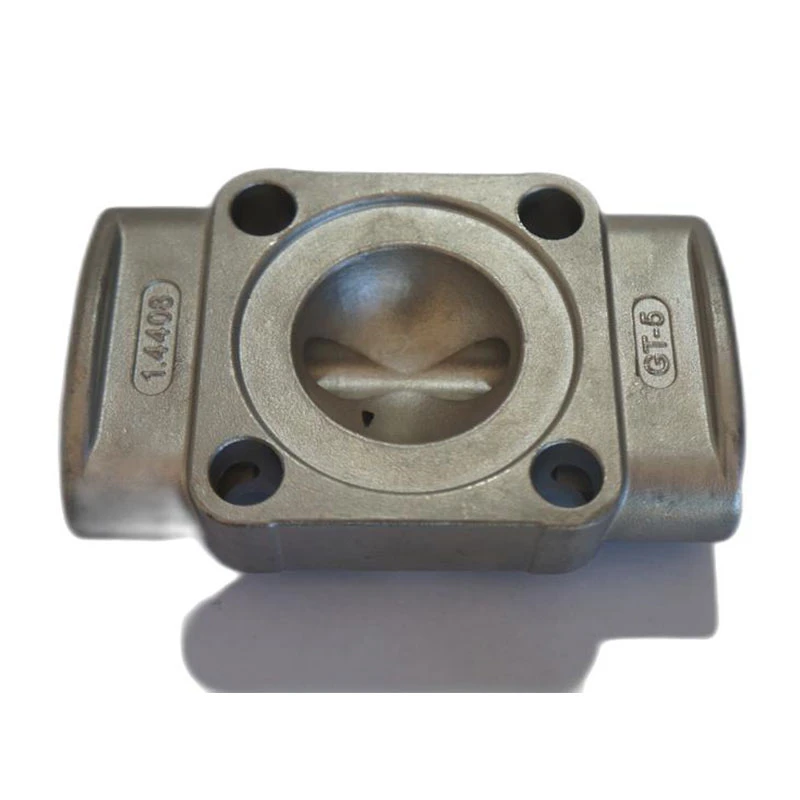
A crucial aspect that enhances the experience of utilizing casting and die casting techniques lies in the expertise of manufacturers. Achieving desired outcomes requires in-depth knowledge of material properties, mold design, and process parameters. Industry experts recommend tailoring each stage of casting to the specific requirements of the final product. By employing advanced simulation and modeling software, it is possible to predict potential defects and optimize the casting process, ensuring superior component quality and performance.
casting and die casting
In-depth specialization in casting and die casting authenticity emphasizes two fundamental elements material selection and mold design. Each application demands a unique combination of metals and alloys that meet specific mechanical and thermal requirements, such as aluminum for its lightweight and conductivity or steel for its strength. Additionally, sophisticated mold design is essential to achieving the desired tolerances and surface finish, which directly impacts the functionality and aesthetic of the final product. Utilizing cutting-edge machining technology, manufacturers can design molds that effectively dissipate heat and withstand the pressures inherent in the die casting process.
Establishing trustworthiness in casting and die casting processes is achieved through adherence to stringent quality assurance protocols.
Leading manufacturers implement robust testing procedures to verify the structural integrity and surface quality of castings. Non-destructive testing methods, such as X-ray inspection and ultrasonic testing, are standard practices to detect subsurface defects, ensuring that every component meets requisite industry standards and specifications.
Moreover, die casting offers environmental benefits as manufacturers strive to create sustainable practices. The ability to recycle metals without losing performance quality significantly reduces material costs and minimizes ecological impact. Additionally, the precision of die casting reduces waste material, contributing to more efficient resource use and aligning with global efforts to promote sustainable manufacturing processes.
As global manufacturing trends shift towards enhanced efficiency and sustainability, casting and die casting remain at the forefront of technological innovation. Through a commitment to continuous improvement, knowledge dissemination, and the adoption of advanced technologies, manufacturers can harness the full potential of these processes, driving industry growth and setting new standards in component manufacturing. This ongoing evolution underscores the relevance and indispensability of casting and die casting in the modern industrial landscape, making them indispensable tools for any forward-thinking manufacturing entity.