Graphite die casting has emerged as a transformative innovation within the manufacturing sector, particularly for industries demanding precision components with intricate designs. This advanced casting technique uses graphite molds to shape liquid metal into desired forms, offering several advantages over traditional metal casting methods.
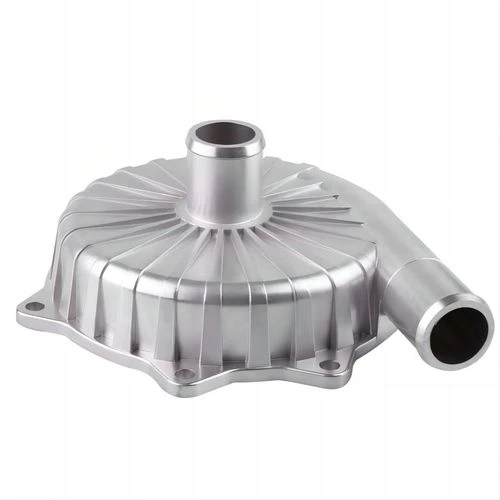
One of the key experiences enhancing the adoption of graphite die casting is its unparalleled thermal conductivity. Graphite's natural ability to dissipate heat more efficiently than metal molds allows for rapid cooling of the casted parts. This accelerated cooling process reduces cycle times, thereby increasing production efficiency and lowering operational costs. Industries such as automotive and aerospace, where large-scale production of engine components and airframe parts is crucial, greatly benefit from these efficiencies.
Expertise in graphite die casting is pivotal for optimizing component design and production. The process is tailored for small to medium-sized production runs, where its flexibility in mold making is most advantageous. Graphite molds are relatively inexpensive and can be easily modified, which is ideal for prototype development and custom components. Unlike steel or iron molds that wear down quickly and require frequent replacements, graphite molds are durable and can withstand multiple casting cycles. This attribute is particularly beneficial for projects requiring high precision and repeatability, as it ensures consistency across large batches.
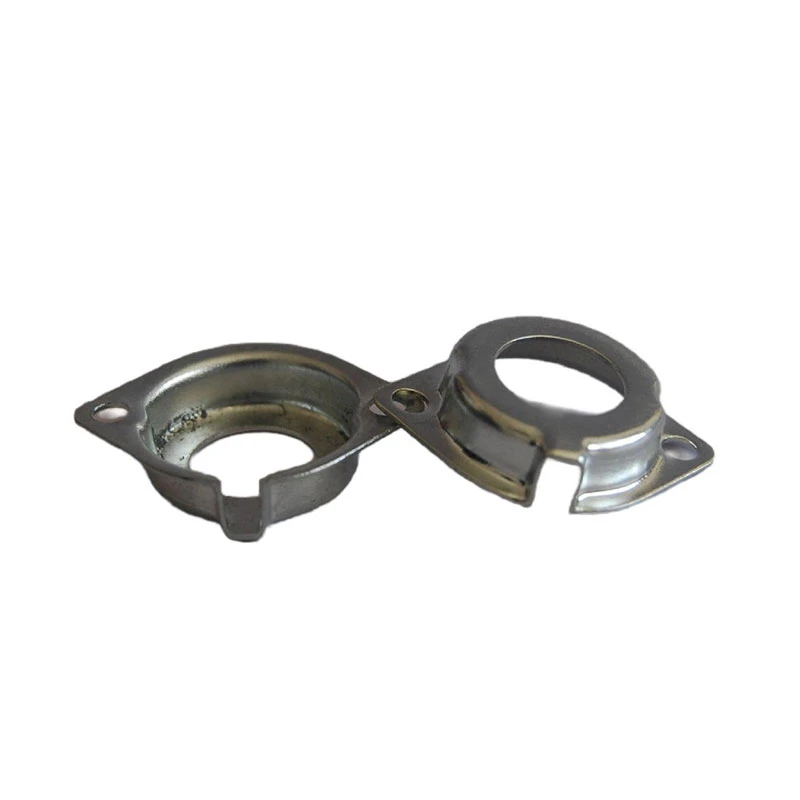
The authoritativeness of graphite die casting is further reinforced by its eco-friendly approach. Traditional metal casting processes often involve energy-intensive procedures and generate significant waste.
Graphite, being a carbon-based material, is more environmentally friendly. It can be recycled, reducing the carbon footprint associated with manufacturing. By adopting graphite die casting, companies can align themselves with sustainable practices that are increasingly demanded by regulatory bodies and environmentally conscious consumers.
graphite die casting
Trustworthiness in graphite die casting is proven by its application in sectors where quality and reliability are non-negotiable. For instance, the electronics industry uses graphite casting for producing components that require high dimensional accuracy and intricate detailing. The process's ability to maintain tight tolerances ensures that even the most complex geometries are achieved without compromising on structural integrity. The medical field also leverages these capabilities, utilizing graphite die casting for creating precise surgical instruments and devices.
Moreover, the advancements in graphite materials science provide additional reliability. Enhanced formulations of graphite composites have been developed to further improve mold life and casting outcomes, making the process even more robust and trustworthy. The collaborative efforts between industrial chemists and material scientists continue to push the boundaries of what can be achieved with graphite die casting, promising exciting future developments.
As technology evolves, the potential applications of graphite die casting are set to expand. Its role in the burgeoning field of additive manufacturing is particularly noteworthy. By combining graphite die casting with 3D printing technologies, manufacturers can potentially streamline production processes and reduce lead times for custom components.
In conclusion, graphite die casting stands out as a leading technology in the die-casting arena due to its efficiency, cost-effectiveness, and environmental benefits. Its extensive application across various demanding industries speaks volumes about its capability to deliver high-quality results. As businesses continue to strive for innovation and sustainability, graphite die casting offers a credible and authoritative solution for modern manufacturing challenges. For companies looking to enhance their manufacturing processes, embracing graphite die casting can lead to significant competitive advantages in today's fast-paced industrial landscape.