Die cast components stand at the forefront of manufacturing innovation, offering exceptional durability and precision across a range of applications. These components are crafted using a process that involves injecting molten metal into a mold cavity, a technique renowned for its ability to produce complex shapes with remarkable accuracy and surface finish. This capability makes die casting an indispensable technique in industries such as automotive, aerospace, electronics, and consumer goods.
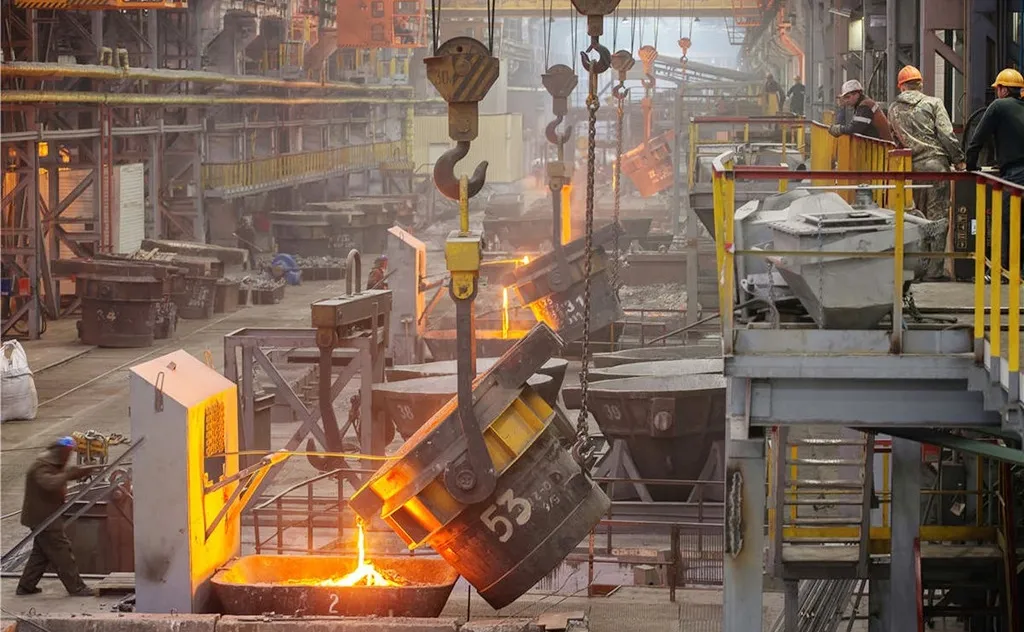
Real-world experience underscores the transformative impact of die cast components on product performance and production efficiency. In the automotive industry, for example, these components contribute to lighter vehicle structures without compromising strength, which translates to better fuel efficiency and reduced emissions. This dual benefit is vital in today’s environmentally conscious market, where manufacturers are under pressure to reduce the carbon footprint of their products.
The expertise involved in producing die cast components cannot be overstated. Skilled engineers and technicians leverage years of mastery in materials science and metallurgical techniques to optimize the die casting process. This expertise ensures that each component meets stringent specifications, with regard to both mechanical properties and dimensional tolerances. Such precision is achieved through meticulous selection of alloys — aluminum, magnesium, zinc, and their respective combinations are chosen based on the specific requirements of the application. Aluminum, for example, is favored for its light weight and high corrosion resistance, while magnesium offers comparable strength with even less weight.
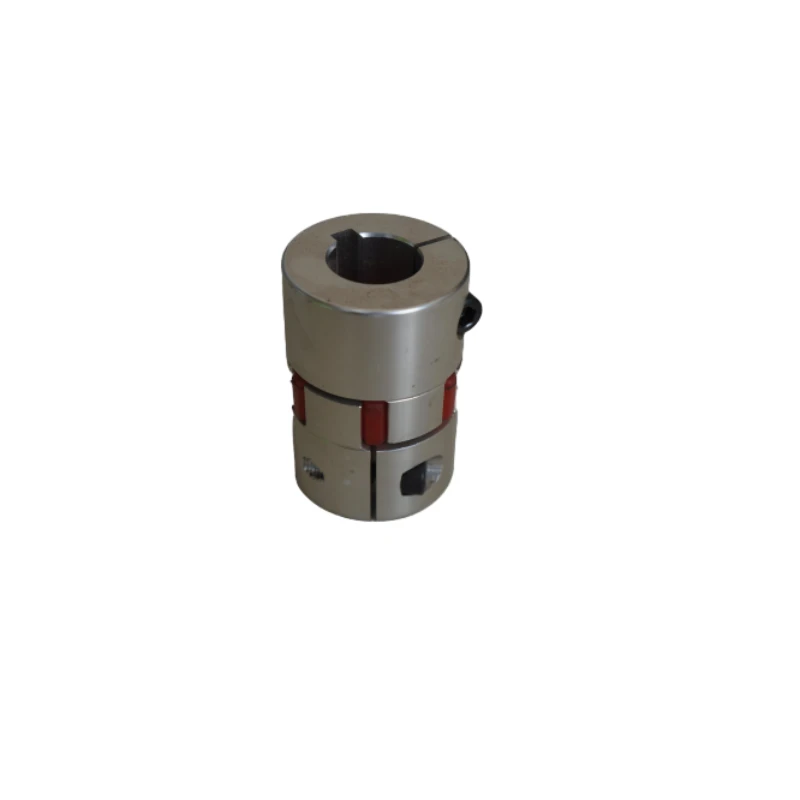
die cast component
The authoritativeness of die cast components in industrial applications is well-established, supported by an ever-growing body of technical literature and case studies. Major corporations frequently publish their findings in peer-reviewed journals, sharing insights into advancements in casting technologies that enhance performance and reduce production costs. This collective body of knowledge not only advances the field but also guides manufacturers in implementing best practices and innovative solutions in their production lines.
Trustworthiness in die cast components stems from the rigorous testing and quality assurance processes they undergo. Each component is subject to a series of non-destructive and destructive testing methods, including x-ray inspections, tensile tests, and fatigue analysis.
This ensures that components will perform reliably over their intended lifespan, even under demanding conditions. Additionally, adherence to international standards such as ISO and ASTM further solidifies the credibility of these components in global markets.
In summary, die cast components embody a union of practical application, technical expertise, industry authority, and reliability. Their role in modern manufacturing continues to expand, driven by ongoing developments that promise improved efficiency, cost-effectiveness, and sustainability. For any manufacturer seeking to innovate and excel, incorporating die cast components is a strategy replete with benefits, ensuring products that are not only superior in performance but also competitive in the marketplace.