Die casting stands as a pivotal process in the manufacturing sector, offering unmatched versatility and precision. This intricate method involves forcing molten metal into a mold cavity under high pressure. It’s most commonly associated with nonferrous metals, including aluminum, zinc, and magnesium, which are favored for their fluidity and mechanical properties. Understanding the foundational aspects of die casting not only enhances product quality but also boosts efficiency, making it an essential skill in the modern industrial landscape.
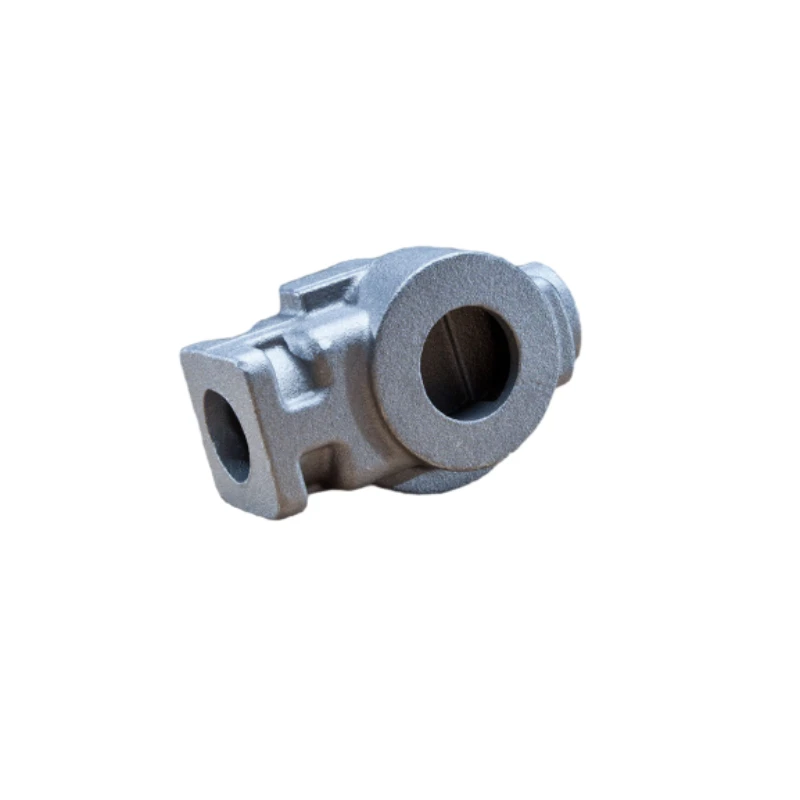
Professional expertise in die casting begins with a deep comprehension of the process's core components. At the heart of die casting lies the mold, typically crafted from hardened tool steel. The molds, or dies, are intricately designed to shape the molten metal into the desired product and can be engineered for complex geometries, allowing for the creation of parts with intricate features and high dimensional accuracy.
Critical to die casting is the control over temperature and pressure. These parameters must be meticulously managed to ensure the molten metal flows into every part of the mold, preserving the integrity of the finished product. The solidification process happens rapidly, often within seconds, allowing for quick production cycles. This accelerated cycle is a significant advantage for high-volume production, reducing costs and time from design to finished product.
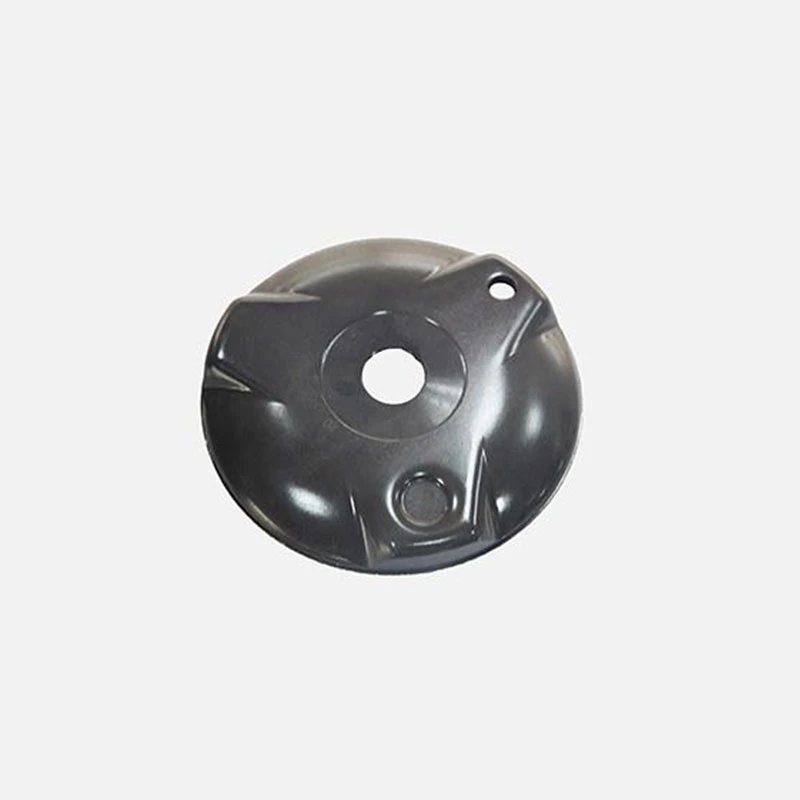
Experience in die casting reveals that choice of material plays a crucial role in the outcome of the process. Aluminum, for instance, is lightweight yet strong, making it ideal for automotive and aerospace components. Zinc, on the other hand, offers superior precision and is perfect for intricate designs, while magnesium is often chosen for its combination of light weight and strength, particularly in consumer electronics.
die casting basics
Maintaining the die casting equipment is another pillar of a reliable operation. Regular maintenance ensures that molds do not succumb to wear and tear that can lead to defects or production downtime. Experienced technicians inspect molds, clean equipment, and replace parts as needed to keep machines running efficiently.
An authoritative figure in die casting will emphasize the importance of continuous improvement and innovation. Techniques such as vacuum-assisted die casting and the use of high-pressure technologies have revolutionized the industry, allowing for even greater precision and reduced waste. These cutting-edge methods not only enhance the strength and appearance of the final product but also promote sustainability by minimizing excess material use.
Trust in die casting is fortified through rigorous quality assurance protocols. Every product must undergo thorough inspections to identify any potential defects or inconsistencies. Advanced technologies, including computerized inspections and real-time monitoring, have become invaluable, assuring that each part meets the stringent demands of today's competitive markets.
Ultimately, die casting excellence is achieved through a blend of technical skill, innovative application, and an unwavering commitment to quality. As the manufacturing landscape evolves, the ability to leverage these elements will determine a company's success in delivering both reliable products and exceptional service to their clients. By prioritizing these foundational aspects, businesses position themselves at the forefront of the industry, meeting the exacting standards of precision and durability required in today's market.