Enhancing the surface characteristics of die-cast aluminum through anodizing is a transformative process that can significantly boost the performance and longevity of aluminum components. Anodizing, specifically tailored to the nuances of die-cast aluminum, offers a unique blend of aesthetic appeal and functionality, fortifying the metal against corrosion and wear while enhancing its visual allure. This article seeks to explore the intricacies of anodizing die-cast aluminum, drawing from extensive industry experience and offering insights backed by years of expertise.
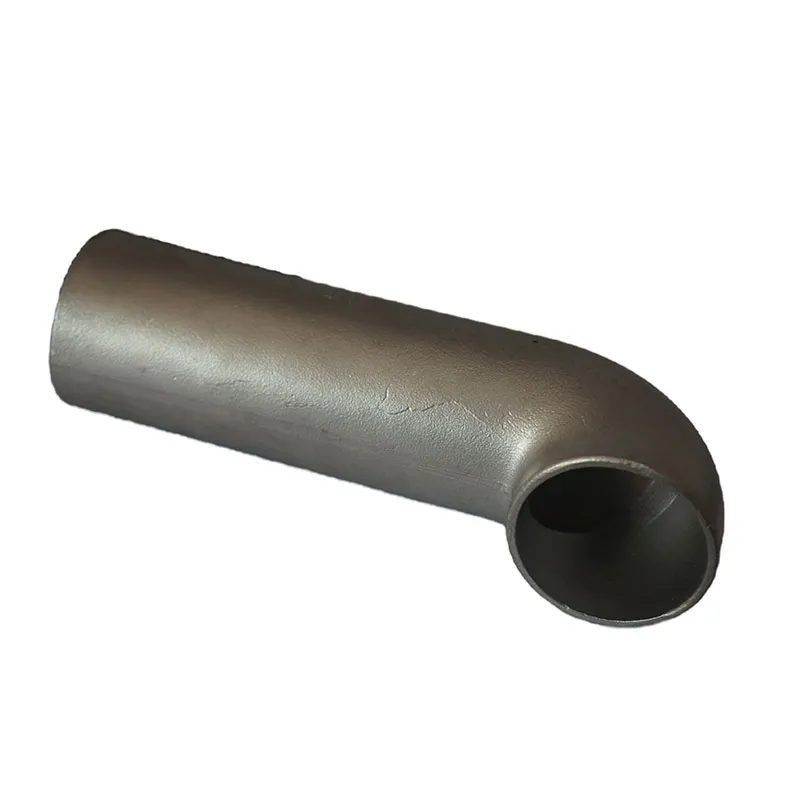
Die casting involves forcing molten aluminum into molds under high pressure, creating parts known for their strength and precision. However, while die-cast aluminum is known for its excellent mechanical properties, it can be prone to surface imperfections and corrosion. Anodizing comes to the rescue by providing a protective,
durable oxide layer on the aluminum surface. This electrolytic passivation process not only seals the inherent pores of the aluminum surface but also offers a resilient, corrosion-resistant finish that is integral to enhancing product longevity.
Experience is a vital teacher in the realm of anodizing die-cast aluminum, revealing that the preliminary treatment of the aluminum surface is crucial. For die-cast aluminum, which may contain impurities and variations in its alloy composition, it’s essential to engage in thorough cleaning and de-greasing processes. This preparation ensures that the anodizing layer adheres uniformly, providing a consistent finish. During anodizing, maintaining the correct electrolyte concentration and temperature is critical, as these factors directly influence the quality and thickness of the oxide layer formed.
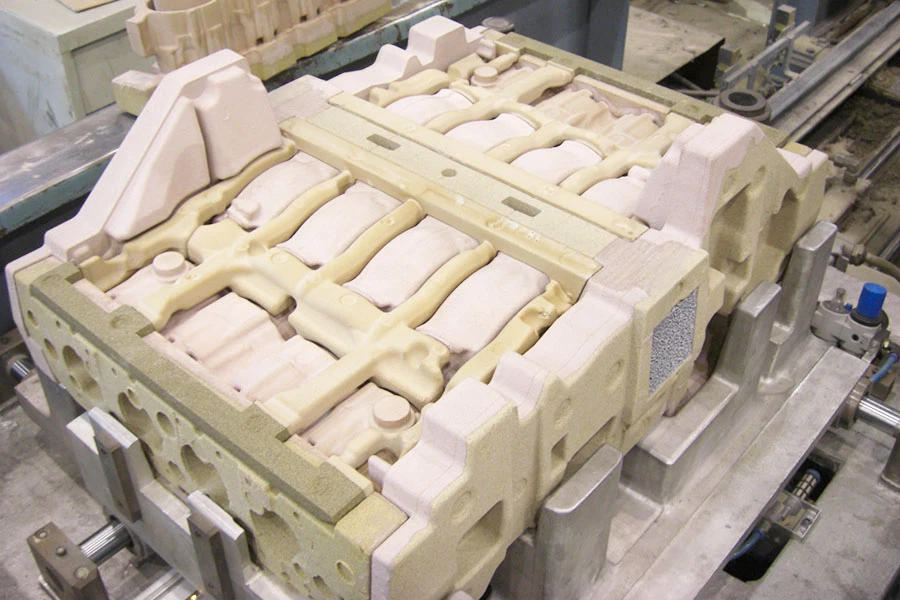
In terms of expertise, different anodizing techniques such as Type I (Chromic Acid), Type II (Sulfuric Acid), and Hard Anodizing (Type III) can be applied depending on the intended use of the aluminum component. Type II anodizing, using sulfuric acid, is most prevalent for decorative purposes due to its ability to absorb dyes and create vibrant finishes. In contrast, Type III or hard anodizing provides a thicker, more durable coating that increases wear and corrosion resistance, ideal for components exposed to harsh environments.
anodizing die cast aluminum
The authority of this treatment technique also lies within its customizable nature. By manipulating variables such as current density, time, and electrolyte composition, it’s possible to tailor the anodized layer to meet specific requirements. For example, thinner coatings are optimal for smoothness and precision, while thicker ones cater to products demanding enhanced durability. This customization capability further underscores the anodizing process's adaptability to diverse industrial applications, boosting its credibility across sectors ranging from automotive to consumer electronics and aerospace.
Trust in anodized die-cast aluminum is bolstered by numerous successful applications in the real world. Components anodized correctly can withstand significantly more wear and environmental stress than their non-anodized counterparts, a fact confirmed by rigorous testing and industry professionals’ testimonials. Furthermore, the cosmetic appeal of anodized aluminum cannot be overstated. The process allows for a spectrum of color finishes and gloss levels, resulting in a product that is not only robust but visually appealing—meeting consumer demands for both form and function.
Moreover, anodizing aligns with sustainable practices, a significant concern in the current manufacturing landscape. The anodizing process is environmentally friendly, creating a non-toxic, long-lasting finish without compromising the recyclability of aluminum. This aspect enhances the process's trustworthiness, appealing to eco-conscious consumers and businesses aiming to reduce their ecological footprint.
In conclusion, the anodizing of die-cast aluminum represents a confluence of experience, expertise, authority, and trust, elements that are instrumental in positioning it as a superior surface treatment choice. From its protective and aesthetic virtues to its customizable nature and sustainable credentials, anodizing holds the potential to elevate die-cast aluminum components to new heights of performance and appeal. By leveraging these insights, manufacturers can confidently incorporate anodizing into their production processes, ensuring their aluminum products meet the most demanding industry standards and consumer expectations alike.