3D sand casting is revolutionizing the manufacturing industry by blending traditional foundry practices with advanced technology. This innovative process is opening up new avenues for creating complex and precise metal parts with efficiency and precision.
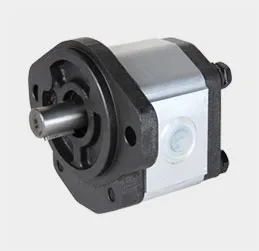
The integration of 3D sand casting within manufacturing practices showcases a synergy between human expertise and technological advancements. This process begins by using 3D printing technology to create sand molds from digital models. These molds are then used to cast metal components, offering unmatched flexibility in design and significant cost savings over conventional methods. One of the main advantages is the ability to produce highly intricate geometries that were previously unattainable with traditional casting methods. As a result, manufacturers experience reduced lead times, lower tooling costs, and the ability to create complex parts in a single operation.
Our experience with 3D sand casting has highlighted its transformative impact across various industries, including aerospace, automotive, and even art sculpture. In aerospace, for example, the precision and accuracy in casting turbine blades have improved engine efficiencies and reduced weight, substantially lowering fuel consumption. Similarly, the automotive industry has seen benefits in terms of enhanced performance components and faster prototyping capabilities. By using 3D sand casting, manufacturers have minimized flaws typically associated with complex castings, improving the overall quality and durability of cast parts.
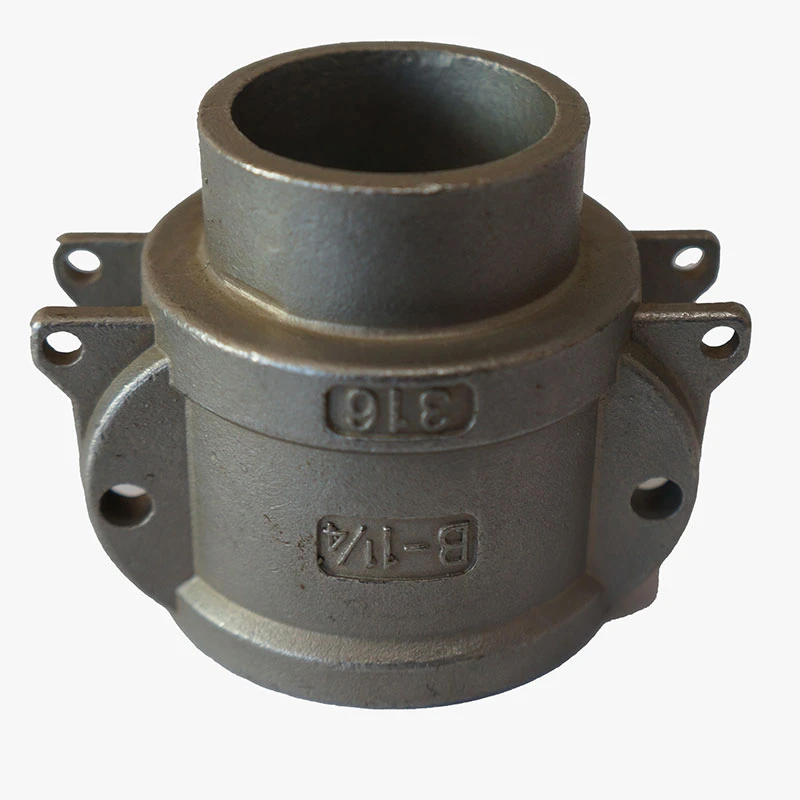
Expertise in 3D sand casting requires a deep understanding of both traditional foundry techniques and modern 3D printing technologies. The process involves specialists in mold making, metal casting, and finishing operations. Professionals within this field are skilled at assessing material properties, understanding thermal expansion, interpreting CAD designs accurately, and refining the casting process to ensure optimal outcomes. Innovative software tools that specialize in mold design are also integral, allowing precise simulation and analysis before actual production begins, thus reducing errors and improving the final product.
3d sand casting
This method’s authoritativeness in the market stems from demonstrable successes and widespread adaptation among leading enterprises. Noteworthy case studies abound, where manufacturers have transitioned from traditional casting methods to 3D sand casting, observing tangible improvements in both the production process and end product quality. For instance, a leading automotive manufacturer reduced production time by 25% while simultaneously enhancing structural integrity and achieving greater freedom in part design.
Such outcomes establish 3D sand casting as a trustworthy technique for modern manufacturing challenges.
Trustworthiness in 3D sand casting is also evidenced through its stringent quality assurance processes. Each stage of manufacturing is meticulously monitored, from initial design to final product evaluation. Testing often involves non-destructive techniques such as X-ray and ultrasonic scanning to ensure that each cast component adheres to precise specifications. The elimination of traditional pattern making reduces human error, further cementing the reliability of this method. Moreover, the regulatory compliance in producing components—especially in the aerospace and medical industries—ensures adherence to stringent safety and quality standards.
In conclusion, 3D sand casting offers manufacturing industries an unprecedented combination of flexibility, precision, and efficiency. By integrating technological prowess with traditional foundry knowledge, it stands as a reliable and authoritative choice for producing top-tier metal components. As industries increasingly lean towards innovation and sustainability, adopting 3D sand casting will be instrumental in meeting the complexities of modern manufacturing demands while maintaining the highest levels of quality and performance.