When exploring the complex world of the stamping process in sheet metal fabrication, one delves into a meticulous combination of precision engineering, material science, and cutting-edge machinery. This process, integral to numerous manufacturing industries, is revered for its ability to transform flat metal sheets into precise shapes and components through the application of high-adaptive technologies.
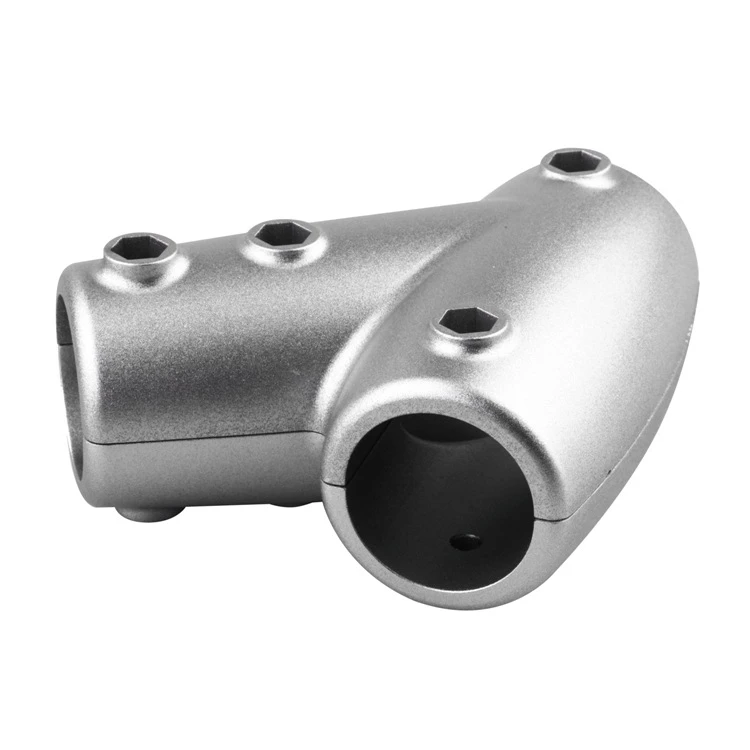
The stamping process in sheet metal fabrication transcends mere mechanical action, involving a spectrum of activities such as punching, blanking, embossing, bending, flanging, and coining. Each of these steps requires a deep understanding of metallurgical principles and machinery capabilities, ensuring not only efficiency but also exceptional product quality.
Punching, a foundational step, involves using a punch press to puncture material, creating precise holes and designs. The choice of tool shape, punch size, and material dictates the final accuracy and aesthetics. An expert in stamping appreciates the punch's role in maintaining structural integrity while achieving high precision.
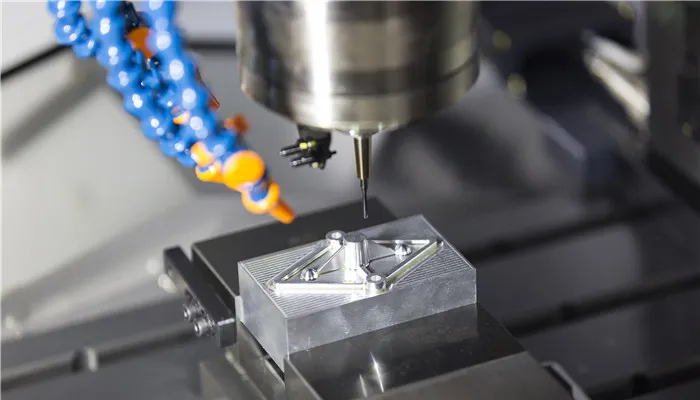
Blanking, closely related to punching, is a process where the desired component is entirely separated from the sheet. Precise die cutting tools ascertain smooth edges and faultless dimensions, which are crucial for assemblies that demand high precision.
Embossing, the art of creating raised or recessed designs, emphasizes aesthetic values alongside functional aspects. Industries leverage embossing to strengthen parts or to enable surface interlocks. Effective embossing necessitates careful calibration of pressure and temperature settings, which can significantly influence material elasticity and final appearance.
Bending and flanging introduce angles and flanges to flat sheets, crafting components that interlock or fit specific design geometries. Experienced metalworkers comprehend the nuances of material springback—when the metal attempts to revert to its original shape post-bending. Mastery of springback compensation ensures that each bend aligns perfectly with design specifications.
what is stamping process in sheet metal
Coining, a process akin to embossing but involving deeper penetration and pressure, is employed not only for marking but also for creating intricate patterns with a heightened degree of detail and precision. It demands a balance of forces to mold the metal without exceeding its yield strength, preventing material failure.
While the stamping process is expansive and robust, its success lies in the symbiotic relationship between human expertise and technology. Advancements such as computer-aided design (CAD) and computer-aided manufacturing (CAM) systems have revolutionized the approach to sheet metal stamping. These technologies enable manufacturers to replicate intricate designs with unparalleled precision and minimal material waste.
Manufacturers also place considerable emphasis on selecting the appropriate materials. The characteristics of aluminum, steel, and brass, among various alloys, influence each stage of stamping. Each metal’s malleability, ductility, and thickness play pivotal roles in deciding the most fitting approach to stamping, ensuring that the end products meet predetermined performance and durability benchmarks.
The stamping process's authority and trustworthiness stem from its widespread application in creating components for automotive, aerospace, electronics, and consumer goods industries. R&D investments continually enhance tooling systems, aiming to extend tool life, improve accuracy, and reduce operational costs.
To align with industry standards, manufacturers adhere to rigorous quality control protocols. Techniques such as finite element analysis (FEA) predict how a material deforms under different conditions. Meanwhile, certifications like ISO 9001 guarantee consistent quality management practices.
In summary,
the stamping process in sheet metal is a confluence of art, science, and engineering. Its practical applications span myriad industries, each demanding precision, durability, and reliability. The combination of expert knowledge, innovative technology, and rigorous quality control solidifies its place as an indispensable part of modern manufacturing.