The sand casting process is a centuries-old method of metal casting that continues to hold relevance in today's manufacturing landscape. Its enduring popularity can be attributed to its simplicity, affordability, and effectiveness in producing high-quality metal parts. This intricate process entails crafting molds from sand mixtures, which are then used to form metal parts with precision and detail. Despite its traditional roots, modern advancements have optimized sand casting, integrating cutting-edge technology and engineering expertise to enhance its capabilities.
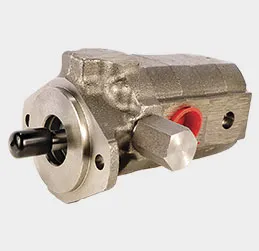
One of the key elements of sand casting is the mold-making stage, where specialized sand is tightly packed around a pattern that resembles the final product. Typically, the sand used comprises silica, due to its fine grains and thermal resistance, combined with bonding agents that provide cohesiveness. It's crucial to balance the sand mixture to achieve the right combination of strength and permeability, ensuring the mold can withstand the flow and heat of molten metal while allowing gases to escape.
Once the mold is ready, the pattern is removed, and cores may be inserted to create internal cavities or complex shapes. This phase demands expert precision, as the slightest imperfections can lead to defects in the final product. An experienced cast technician understands the complexities of pattern design and mold configuration, ensuring the highest level of accuracy in replication.
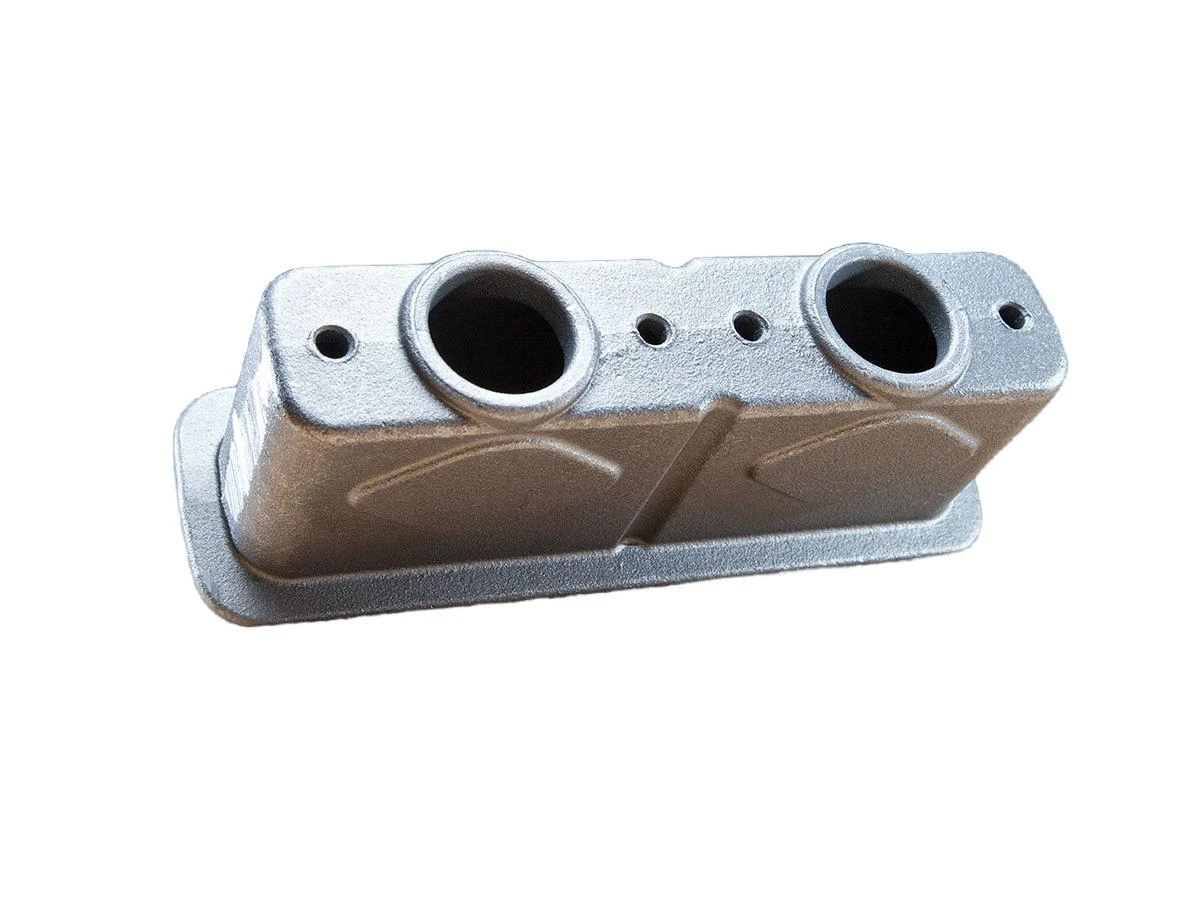
Pouring molten metal into the prepared mold is a pivotal moment in the sand casting process. The temperature, viscosity, and flow rate of the metal must be meticulously controlled to prevent common issues such as turbulence, misruns, or gas entrapment. This requires a deep understanding of metallurgy and thermal dynamics, as each metal alloy behaves differently under heat. Professionals in this field are equipped to anticipate and resolve these issues, ensuring the finished casting meets exact specifications.
Cooling and solidification follow, where the metal gradually cools and hardens within the mold. The cooling rate can significantly affect the mechanical properties of the casting, including grain size, microstructure, and overall strength. Therefore, experts closely monitor cooling conditions to enhance the quality of the final product, sometimes employing techniques such as controlled atmosphere cooling or temperature gradients to refine the metallurgical structure.
what is a sand casting process
After the metal has cooled, the casting is removed from the sand mold and undergoes various finishing processes. These may include trimming, surface cleaning, heat treatment, and quality inspection. Each step contributes to the dimensional accuracy and surface finish of the casting, essential for meeting detailed product specifications. Seasoned professionals utilize advanced tools and techniques to achieve the required tolerances and finishes, emphasizing the importance of expertise and attention to detail.
The sand casting process's versatility is evident in its application across various industries, from automotive to aerospace, and consumer goods to heavy machinery. This adaptability underscores its value in producing small batches of custom parts or large volumes of standardized components. The process's ability to accommodate complex designs and integral shapes without the need for extensive machining also adds to its cost-effectiveness and efficiency.
Moreover, the environmental aspect of sand casting cannot be overlooked. Many facilities have made strides in adopting sustainable practices, such as recycling used sand and minimizing waste. These measures not only reduce environmental impact but also align with industry trends towards eco-friendly manufacturing solutions. Practitioners with environmental expertise can guide organizations in implementing green strategies, thereby enhancing their sustainability credentials.
In conclusion, the sand casting process combines traditional methods with modern innovations to offer a robust and adaptable means of metal production. It requires a delicate balance of experience, expertise, and precision, making the role of skilled professionals indispensable. Whether addressing complex designs, ensuring quality, or enhancing sustainability, experts in sand casting drive the industry forward, demonstrating its enduring relevance and capability in the modern manufacturing realm.