The world of sand casting materials is vast, offering numerous options for manufacturers and hobbyists dedicated to creating intricate metal components. This age-old technique remains relevant today because of its versatility, precision, and cost-effectiveness. Yet,
achieving superior results in sand casting is heavily dependent on the material chosen for the mold-making process.
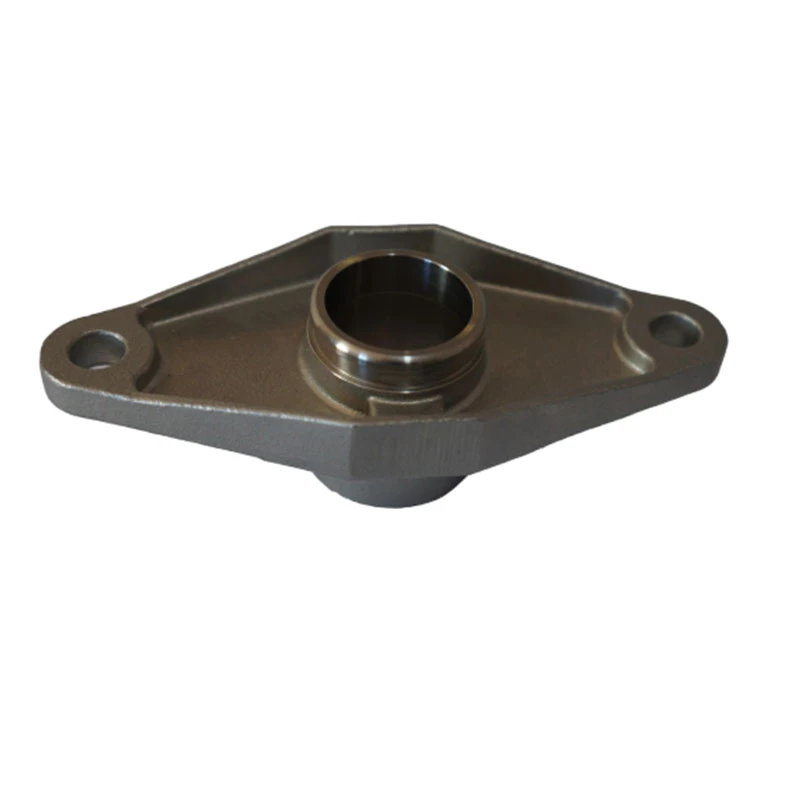
Sand casting involves creating a mold from a sand mixture that can withstand the extreme temperatures of molten metal. Choosing the right sand is crucial, and green sand, the most commonly used, remains a top choice. Comprising silica sand mixed with clay and water, it provides an ideal balance of permeability, cohesiveness, and flexibility. The moisture content ensures the sand adheres well, maintaining the shape when the pattern is removed. Following pouring, the mold's collapsible nature facilitates easy extraction of the final product without damaging it.
Another fundamental material is the bonding agent, which ensures the sand holds its form under the molten metal's weight and temperature. Besides clay, modern casting experts explore synthetic binders that offer enhanced properties such as increased strength and thermal stability. These innovations derive from in-depth studies of sand casting processes, aimed at optimizing efficiency and precision while reducing production costs.
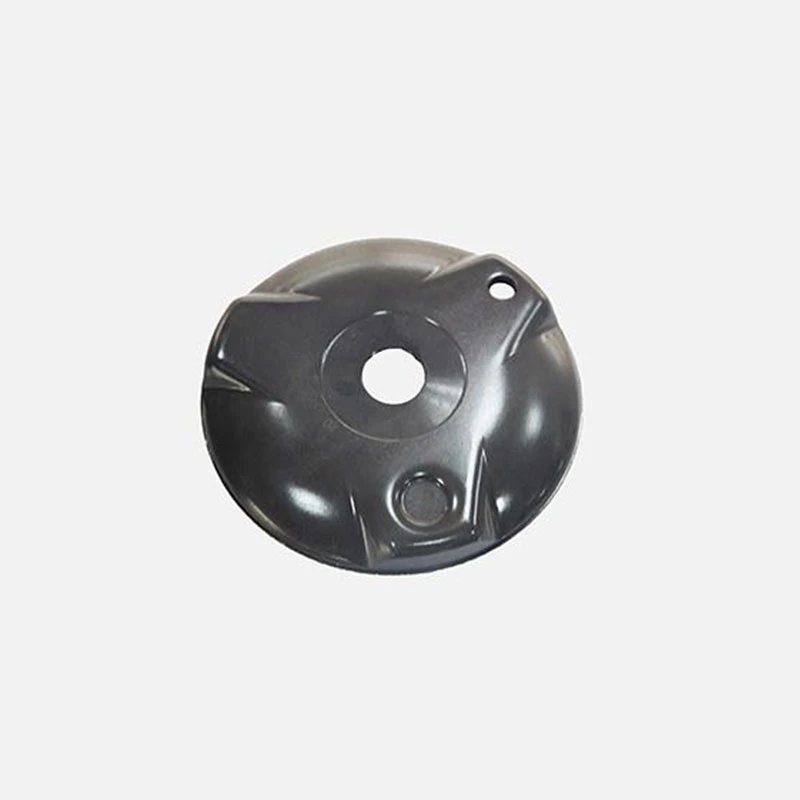
While silica sand is prevalent, it's not the sole option. Industries dealing with higher temperature metals often turn to zircon or chromite sands, known for their superior refractoriness and thermal conductivity. Using these sands improves surface finish and reduces casting defects by maintaining consistent mold temperatures and minimizing thermal expansion.
Furthermore, for those prioritizing environmental and health impacts, choosing non-silica alternatives can be pivotal. Olivine sand, devoid of free silica, offers a safer working environment, reducing concerns about silicosis without compromising on quality. This conscientious effort aligns with modern manufacturing's shift towards sustainable practices.
sand casting material
Crafting the perfect mold isn't just about the sand. Advanced sand casting incorporates additional materials, like core sands with specific compositions tailored to create internal cavities. The selection often depends on the alloy being cast, as different metals impose varying demands on the mold. Technical understanding of these aspects showcases the intricate balance between science and craftsmanship in sand casting.
Experienced foundry professionals constantly evolve by integrating technological enhancements into traditional methods. They adopt computerized simulations to predict casting outcomes, refining material choices and optimizing designs before any physical production begins. This blend of expertise signifies a remarkable leap from traditional trial-and-error approaches to data-driven precision.
In an industry where trust and reliability are paramount, establishing alliances with reputable suppliers ensures a steady flow of high-quality materials. These robust partnerships facilitate innovation, allowing foundries to access the latest materials and insights. The credibility that stems from using reliable sand casting materials underpins the industry's foundations, driving continuous development and excellence.
Sand casting, inherently tactile and profound, thrives through the knowledgeable application of the right materials, paired with a commitment to ongoing learning and improvement. In a constantly evolving sector, expertise and trustworthiness remain the cornerstones of success, ensuring that the products meet and exceed industry standards while pushing the boundaries of what's possible.