PDC die casting, an efficient process utilized globally, stands at the forefront of modern manufacturing due to its precision and cost-effectiveness. Companies worldwide integrate PDC die casting in producing complex geometries with smooth surface finishes, which are essential in numerous industries such as automotive, aerospace, and electronics.
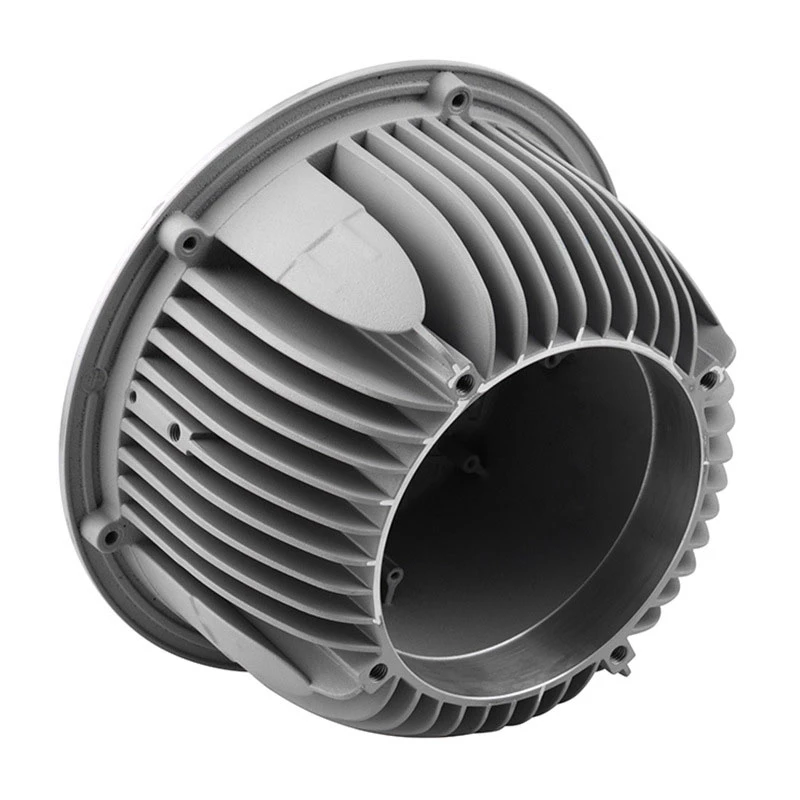
The journey of PDC die casting begins with its ability to produce highly detailed products. The method involves injecting molten metal into a mold cavity under high pressure. This technique allows for the creation of parts that are not only geometrically complex but also possess superior dimensional accuracy. Experts in the field emphasize that its precision significantly reduces the need for further machining, thus cutting down production costs and time.
A critical component of PDC die casting is the use of non-ferrous metals like aluminum, magnesium, and zinc. These materials are chosen for their lightweight properties, high thermal and electrical conductivity, and excellent corrosion resistance. For instance, aluminum's ability to withstand high temperatures and maintain structural integrity makes it a favored choice in producing automotive parts. It effectively enhances fuel efficiency by reducing the overall weight of vehicles. Professionals in the automotive industry acknowledge the expertise of die cast engineers in optimizing material properties to meet specific design requirements.
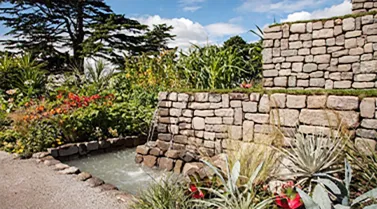
Trustworthiness in PDC die casting is fortified by adhering to stringent quality control measures. Advanced techniques like X-ray inspection and spectroscopy are employed to ensure each cast adheres to exacting industry standards. Manufacturing experts advocate the necessity of employing real-time monitoring systems that track the process parameters – such as die temperature, metal composition, and pressure consistency – to predict and rectify potential defects. This unwavering commitment to quality assurance is a testament to the reliability of PDC die casting products.
pdc die casting
Environmental sustainability is another advantage where PDC die casting excels. The process's efficiency ensures minimal waste, and the ability to recycle materials exemplifies its eco-friendly nature. As industries push towards greener production methods, PDC die casting aligns with these goals by minimizing environmental impact while maintaining production efficiency. Sustainable practices, such as using eco-friendly lubricants and optimizing energy consumption during the process, showcase the industry's expertise in balancing productivity with ecological responsibility.
Authoritativeness in this domain is further enhanced by continuous innovation and research. The introduction of technologies such as computer-aided design (CAD) and computer-aided manufacturing (CAM) has revolutionized the design and production phases, enabling the simulation of casting processes for identifying and mitigating potential issues before they arise. Industry leaders invest in research to uncover new alloys and enhance existing processes, ensuring PDC die casting remains at the cutting edge of manufacturing technology.
Brands utilizing PDC die casting benefit from a profound blend of expertise, trust, and authority, ensuring their products meet the highest quality and performance standards. As manufacturing demands evolve, the adaptability and technological prowess of PDC die casting underscore its indispensable role in creating the products of tomorrow.