Die casting, a versatile and efficient process, has found its way into various industries due to its ability to produce complex shapes with high precision and excellent surface finish. Its applications are diverse, demonstrating its critical role in modern manufacturing. Delving into the many uses of die casting reveals its impact and versatility in product creation, making it an indispensable technique in industries such as automotive, aerospace, electronics, and consumer goods.
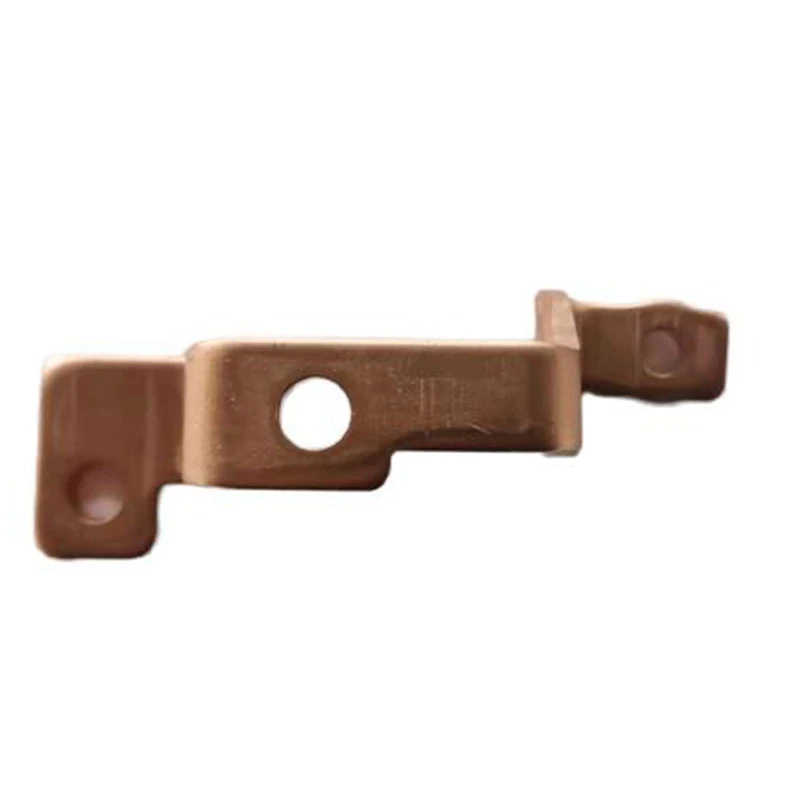
In the automotive industry, die casting is primarily utilized to produce robust and lightweight components that are vital for enhancing vehicle performance and fuel efficiency. This process is pivotal in manufacturing engine blocks, transmission cases, and components of the structural frame. Aluminum, a material frequently used in die casting, is prized for its lightweight and corrosion-resistant characteristics, making it ideal for achieving the automotive industry's evolving standards for lightweighting. An expert in automotive manufacturing would attest to the significance of die casting in improving the overall efficiency and longevity of vehicles.
In aerospace, where precision and material integrity are paramount, die casting offers a cost-effective solution for producing parts that meet stringent specifications. From components for aircraft engines to structural parts of the fuselage, die cast parts possess the strength and reliability necessary for high-stakes applications. Die casting's ability to produce intricate and durable components aligns with the aerospace sector's need for parts that can withstand extreme conditions without compromising safety or performance.
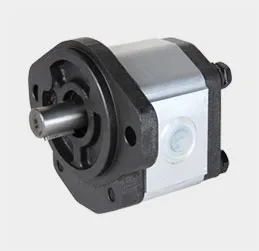
The electronics industry also benefits significantly from die casting. As devices become increasingly compact and complex, the need for precise and reliable components has surged. Die castings provide excellent thermal conductivity, essential for heat dissipation in electronics like smartphones, laptops, and LED lighting. The seamless production of thin-walled enclosures and heatsinks demonstrates die casting's capacity to meet the electronics industry's fast-paced innovation demands.
Consumer goods manufacturers leverage die casting to deliver products that balance aesthetics and functionality. Whether it’s hardware for home fittings, such as handles and light fixtures, or components within appliances, the versatility in design and the smooth finish achievable through die casting are unmatched. Die casting allows for significant customization, meeting consumer expectations for quality and variety in an increasingly competitive market. Experts emphasize the role die casting plays in producing durable and appealing products that enhance consumer satisfaction and brand loyalty.
die casting uses
Moreover, environmentally conscious production is an intrinsic advantage of die casting that aligns with global sustainability goals. The process itself is efficient in material usage, and the prevalent use of recyclable metals like aluminum and zinc further supports eco-friendly manufacturing paradigms. This sustainable aspect of die casting makes it a preferred choice among industries that are steering towards reducing their carbon footprint, without sacrificing product integrity.
In the realm of medical devices, die casting is an unmissable technology, contributing to the production of intricate and reliable components used in diagnostic and surgical equipment. Its capacity for precision production ensures that medical devices meet stringent safety standards critical for patient health. An authoritative voice in medical manufacturing would highlight die casting's pivotal role in advancing healthcare technologies through dependable and affordable medical equipment production.
Die casting is a testament to manufacturing innovation, proven by its widespread application across critical industries. Its ability to deliver precision, durability, and aesthetic value, combined with cost efficiency, fortifies its status as a go-to manufacturing process. The adaptability of die casting to embrace new materials and technologies ensures that it remains at the forefront of manufacturing techniques.
In summary, the importance of die casting across so many domains underscores its diverse utility and profound impact on modern production practices. Its applications are not just limited to current usage but also extend to future possibilities as industries continue to evolve and demand more from their production processes. An authoritative understanding of die casting’s benefits and capabilities ensures that industries can make informed decisions that lead to enhanced product quality and performance, paving the way for groundbreaking advancements.