Die casting stands as a pivotal method in the manufacturing industry, merging the realms of speed, precision, and durability. Over the years, this intricate process has become integral in producing complex metal parts, widely used in automotive, aerospace, and consumer products sectors. The art of die casting entails injecting molten metal into molds to create parts with exceptional accuracy and smooth surface finishes. Mastery in this domain is built on the pillars of expertise, experience, trust, and authoritative knowledge.
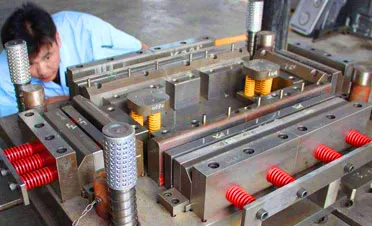
The die casting method revolves around two primary types hot-chamber and cold-chamber processes. The hot-chamber method is usually employed for metals with low melting points, such as zinc and magnesium alloys.
This technique allows for rapid cycling and high production rates. On the other end, the cold-chamber method is preferred for metals like aluminum and copper alloys, where higher melting points are involved. Each method provides unique benefits tailored to specific material requirements, highlighting the method's adaptability.
Expertise in die casting lies in understanding the nuances of mold design—a core component influencing the quality and integrity of the final product. Advanced mold design ensures that the molten metal flows optimally, minimizing defects and ensuring uniformity. Utilizing cutting-edge CAD software, experienced engineers design molds that not only accommodate the contraction and cooling of metals but also facilitate efficient production cycles. Such expertise reduces material waste and maximizes the economic efficiency of manufacturing operations.
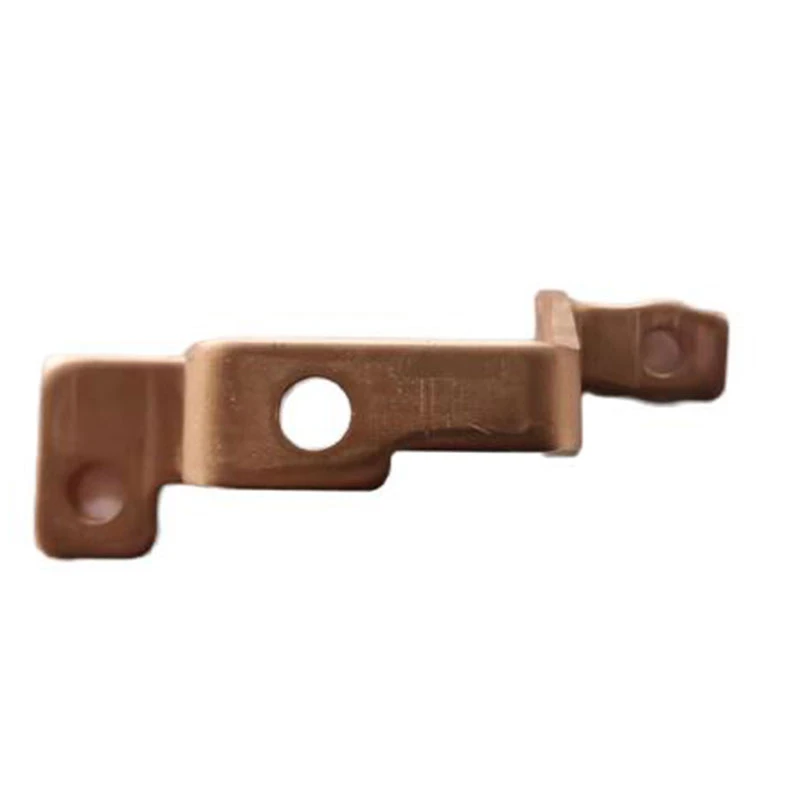
Experience in die casting additionally informs the selection of the appropriate alloy, a decision critical to meeting the demanding specifications of diverse industries. Each alloy offers distinct properties aluminum boasts corrosion resistance and lightweight attributes, ideal for automotive frames; zinc, with its excellent dimensional stability, is preferred for intricate components; magnesium, being the lightest structural metal, finds relevance in applications where weight is a critical factor. Professionals informed by extensive experience efficiently match material properties with client requirements to deliver superior solutions.
die casting method
Authoritativeness in the die casting field is underscored by strict adherence to international quality standards, such as ISO and ASTM specifications, which guarantee that the final products meet precise safety and performance criteria. Manufacturers demonstrating thorough compliance earn certifications that act as benchmarks of their dedication to quality. Partnering with authoritative organizations for regular audits further solidifies a company's reputation, assuring clients of their unwavering commitment to excellence.
Trustworthiness is cultivated through transparent, client-focused practices. In the die casting industry, reliable manufacturers prioritize open communication, furnishing clients with detailed insights into production processes, timelines, and potential challenges. By establishing clear channels of communication and setting realistic expectations, manufacturers nurture robust relationships with their clients, fostering trust and repeated collaborations.
As industries continue to evolve and demand greater customization and higher performance, die casting remains at the forefront of technological advancements. Innovations, such as vacuum-assisted die casting and semi-solid metal casting, are pushing the boundaries of what is achievable, offering enhancements in strength and surface finish. By staying ahead of the curve, manufacturers not only meet current client needs but also anticipate future industry trends, delivering groundbreaking solutions tailored to an ever-changing market landscape.
In conclusion, die casting is more than just a manufacturing technique; it's a discipline that requires a blend of technical knowledge, precision, reliability, and foresight. Whether producing small, intricate components or large structural parts, those who master the die casting method continue to provide vital products essential across a multitude of industries, reaffirming the method's indispensable role in modern manufacturing.