Precision bullet casting is an art that merges skill, science, and a passion for excellence. For anyone looking to master this craft, understanding its nuances is vital. Unlike mass-produced bullets, precision bullets are crafted to exact specifications, ensuring unparalleled accuracy and performance. This meticulous process is not only about creating ammunition but also about enhancing the overall shooting experience.
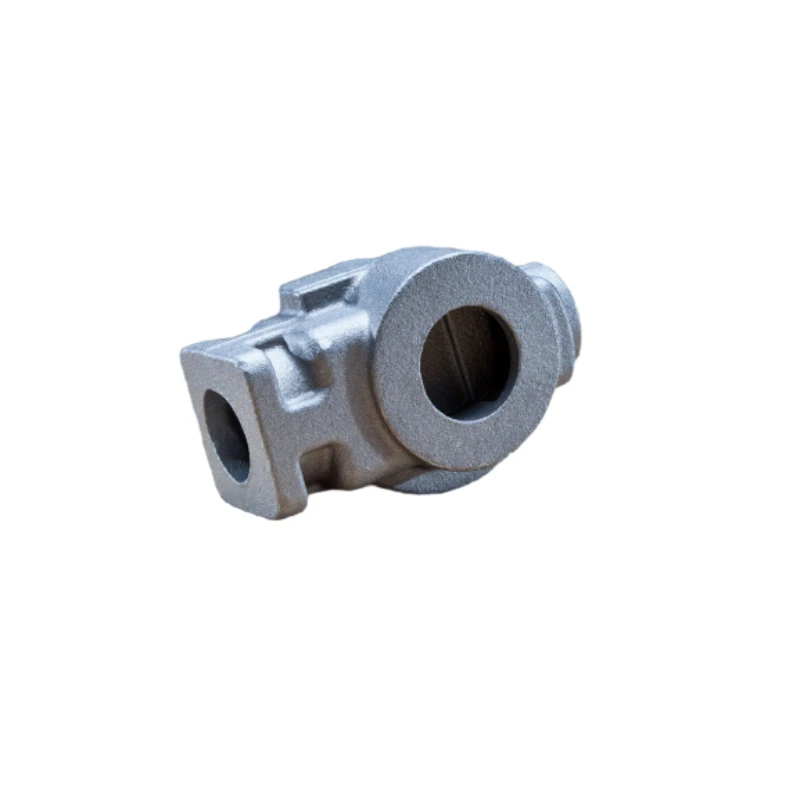
The journey of casting precision bullets begins with selecting the right materials. Typically, lead is the preferred choice, given its malleability and density. However, achieving precision requires more than just basic lead. Alloys combining lead with antimony or tin enhance hardness without sacrificing weight, crucial for consistent performance. Enthusiasts often experiment with different ratios to find a personalized blend that meets their specific needs.
The next critical step is the mold selection. Precision bullet casters invest in high-quality molds, often made from steel or brass, which offer durability and produce consistent results. A superbly designed mold, often custom-made, ensures that each bullet exits with its intended shape and size, minimizing the need for subsequent refinements. The mold's intricacies, such as the shape, grain, and lubrication grooves, dictate the bullet's final performance.
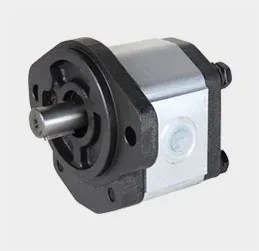
Temperature control during casting is an essential factor often overlooked by novices. Molten metal temperatures must be meticulously monitored, as variances can lead to imperfections, affecting balance and accuracy. Experienced casters utilize thermometers and maintain a steady heat source, ensuring each pour is consistent. Some even use digital induction furnaces that provide precise temperature regulation, which is essential for achieving uniformity.
Once cast, each bullet is carefully inspected and measured. A successful caster knows that even the slightest discrepancy in weight or shape can dramatically influence a bullet's flight path. Using micrometers and specialized scales, bullets are checked against tight tolerances, often within one-tenth of a grain, to guarantee uniformity. Those that fall short of these standards are re-melted and recast, ensuring only the highest quality products are used.
cast precision bullets
Lubrication is the next phase, critical for maintaining the bullet's integrity during firing. The right lubricant reduces friction and prevents lead fouling in the gun barrel, enhancing both accuracy and lifespan of the firearm. Cast bullet enthusiasts often craft their own lubes, combining beeswax, paraffin, and natural oils, to create a custom solution tailored to their specific shooting conditions.
Finally, load development is where precision bullet casting truly becomes personalized. It involves creating the perfect marriage between the bullet and the firearm. Hand loaders meticulously adjust powder charges and seating depths to match the bullet's characteristics, often spending hours at the range fine-tuning their loads. Data collected from each round fired informs adjustments, and iterative testing continues until peak performance is achieved.
Safety during casting cannot be overstressed. Proper ventilation and protective gear are necessary to prevent exposure to lead fumes, which can be hazardous. Precision casters adhere to strict safety protocols, underscoring their commitment not just to excellence in casting, but to responsible and safe practices.
Bullets cast with precision are not merely projectiles; they are a testament to the shooter's dedication to excellence. While the process is time-consuming and requires a significant investment in equipment and skill, the rewards are immense. Shooters who cast their own bullets enjoy improved accuracy, consistency, and the satisfaction of firing a product they crafted with their own hands. In an age of mass production, the tradition of casting precision bullets continues to thrive, embodying a blend of tradition, innovation, and a perpetual quest for perfection.