Aluminium high pressure die casting is a pivotal manufacturing process offering a remarkable blend of precision, efficiency, and cost-effectiveness. As industries globally pivot towards lightweight and high-strength components, aluminium has emerged as a preferred material, fulfilling diverse applications from automotive to electronics.
Herein lies the allure and intricacy of its die casting process.

High pressure die casting (HPDC) is renowned for producing intricate and dimensionally accurate metal components. Key to this is its ability to produce high volumes of parts with consistent quality, making it a staple in mass production settings. Aluminium, with its lightweight properties and excellent thermal conductivity, complements HPDC perfectly. This synergy results in components that not only meet stringent operational requirements but also reduce the overall carbon footprint due to reduced energy consumption both in production and end-use phases.
The process begins with the preparation of a steel mold known as a die. This mold is meticulously designed with precision, considering factors like shrinkage and flow dynamics of molten aluminium. A salient feature of HPDC is the use of a cold chamber where aluminium is melted to a precise temperature to ensure optimal fluidity. This molten aluminium is then injected into the die under high pressure, often exceeding 20,000 psi, ensuring that the metal reaches every corner of the mold.
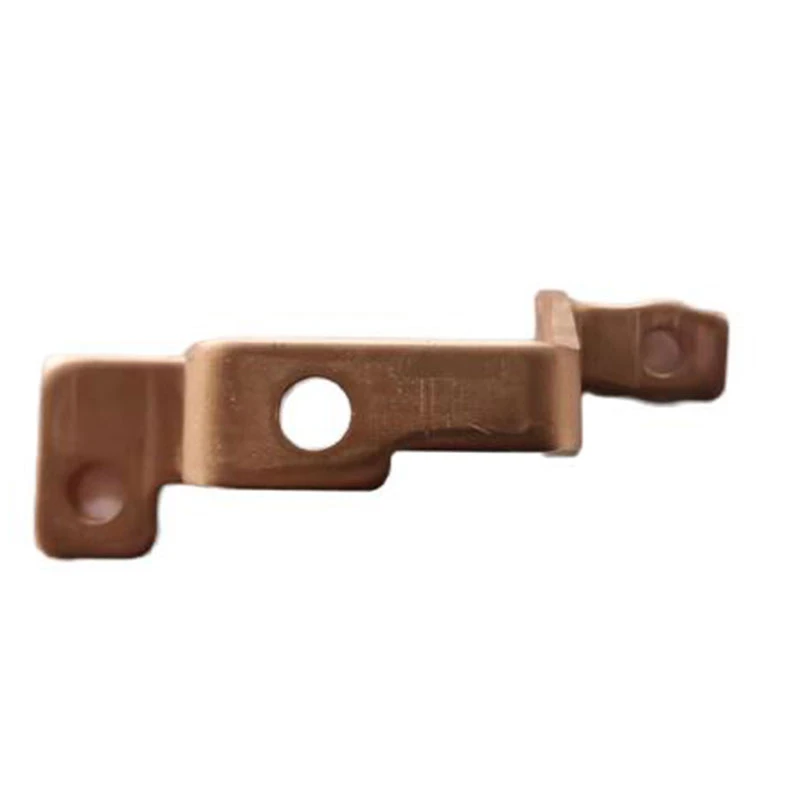
Experience plays a critical role as engineers must monitor key parameters such as temperature, pressure, and injection speed. Deviations could lead to defects like porosity or cold shuts, affecting the component's integrity. Over the years, advancements in simulation software have enhanced predictive maintenance and quality control measures, allowing real-time adjustments and significant reduction in waste.
Once the aluminium has solidified, the die opens, and ejector pins assist in removing the casting. Post-processing involves trimming excess material and undergoing heat treatments to enhance mechanical properties. Plating or painting may be applied depending on the end application, ensuring both functional and aesthetic standards are met.
Expertise in HPDC goes beyond understanding the physical process. It necessitates a comprehensive understanding of material science, thermodynamics, and metallurgy. Industry professionals often undergo rigorous training to grasp these complexities, making them indispensable assets within manufacturing teams.
aluminium high pressure die casting process
In terms of authoritativeness, the adoption of quality certifications such as ISO/TS 16949, specific to the automotive industry, is prevalent. These certifications ensure adherence to stringent international standards, reinforcing the credibility of the manufacturing process and the reliability of the parts produced.
Trustworthiness in aluminium high pressure die casting is built over time through stringent quality checks and consistent product delivery. Manufacturers often establish longstanding relationships with clients, predicated on trust and proven performance.
The automotive industry benefits significantly from aluminium HPDC, where components such as engine blocks, transmission cases, and structural frames are common. The electronics sector also leverages its benefits, particularly in producing enclosures that require complex geometries and superior heat dissipation.
Notably, the sustainability aspect of aluminium die casting stands out. The recycling potential of aluminium is a pivotal factor, contributing to circular economy practices. Aluminium can be recycled multiple times without degradation in quality, significantly reducing the environmental impact.
In conclusion, the aluminium high pressure die casting process is a cornerstone of modern manufacturing, combining efficiency with precision to produce high-quality components. With expert oversight, authoritative practices, and a commitment to sustainability, this process continues to evolve, meeting the ever-growing demands of technological advancement while maintaining the trustworthiness that industries rely upon.