Sand casting foundries play a pivotal role in the manufacturing sector, transforming basic raw materials into complex components essential for various industries. With decades of evolution, these foundries have refined a process that balances traditional craftsmanship with cutting-edge technology. Such a dual approach ensures the production of high-quality castings, which cater to diverse sectors, including automotive, aerospace, and heavy machinery.
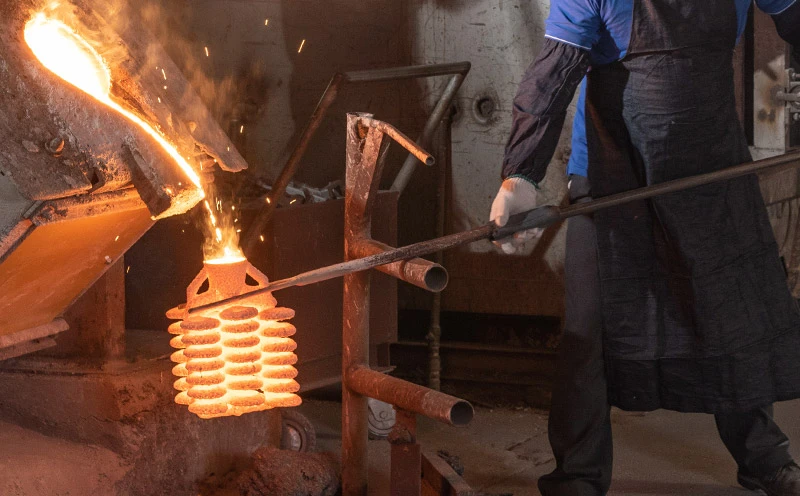
The sand casting process begins with the creation of a mold, typically utilizing a mixture of sand, clay, and water.
This mold acts as the blueprint for the final product. Sand is chosen for its ability to retain intricate details, making it an ideal material for complex geometries. The expertise required to mix and compact the sand to achieve the perfect mold consistency is immense, often calling for skilled artisans with years of hands-on experience. This discerning craftsmanship ensures each casting meets exacting industry standards.
Once the mold is ready, the foundry pours molten metal into the cavity. This step demands meticulous control of temperature and pouring speed, factors that heavily influence the quality of the final product. Foundries use various metals, such as iron, aluminum, and copper alloys, tailoring each pour to the specific needs of the component being manufactured. The expertise gained from years of practice allows foundry operators to anticipate potential issues, ensuring that each casting is free from defects such as porosity or shrinkage.
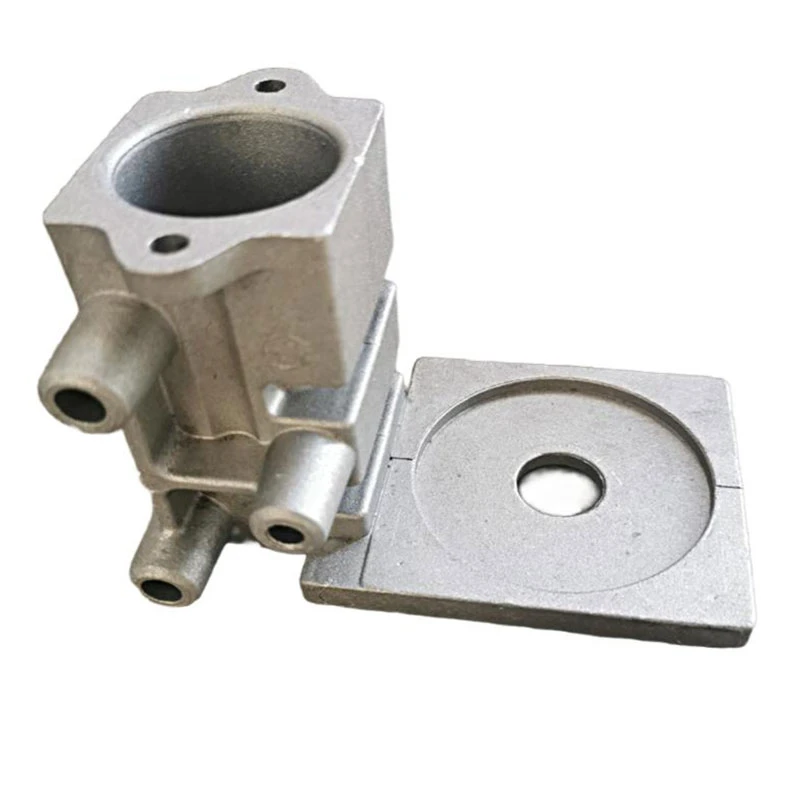
After cooling, the casting is separated from the sand mold, a stage known for its labor-intensive nature. This is where the foundry’s commitment to quality assurance shines. Each casting undergoes rigorous inspection and finishing processes. Technologies like X-ray inspection and computerized tomography are employed to detect internal defects, demonstrating the industry's embrace of innovative solutions to maintain their authority on quality.
sand cast foundry
The environmental impact of sand casting has come under scrutiny, pushing foundries to adopt sustainable practices. Recycling sand from broken molds, reducing emissions, and optimizing energy consumption exemplify the industry's dedication to environmental stewardship. By doing so, they assure clients and stakeholders of their commitment to sustainable manufacturing, enhancing their trustworthiness.
In an ever-evolving market, product customization has become crucial. Sand cast foundries exhibit remarkable adaptability, designing bespoke solutions for clients with unique requirements. This agility not only demonstrates their authoritative command over the craft but also cements their status as indispensable partners in product innovation.
The growth of digital technology has further revolutionized foundry operations. Many have integrated computer-aided design (CAD) and 3D modeling into their workflow, leading to more precise mold creation and reducing lead times. This technological prowess underscores their expertise, offering clients detailed visualizations and accurate prototypes.
In conclusion, sand cast foundries stand as paragons of Experience, Expertise, Authoritativeness, and Trustworthiness. Their blend of skilled artisanship, technological innovation, and an unwavering commitment to quality and sustainability form the bedrock of their operations. As industries advance, these foundries continue to push boundaries, crafting components that meet the ever-changing needs of global markets. Their enduring legacy is a testament to their unparalleled mastery and dedication to the craft of sand casting.