Precision casting solutions have revolutionized the manufacturing landscape, offering unparalleled accuracy and versatility for a wide array of industries. With over two decades of hands-on experience in the field, I understand the nuances and complexities that underpin this intricate process. Equipping manufacturers with the ability to create components with exceptional precision and minimal waste, precision casting is a paramount asset to sectors ranging from aerospace to medical devices.

In the realm of expertise,
precision casting stands out as a meticulously orchestrated process. It begins with the creation of a high-quality wax model that mirrors the exact specifications of the desired part. This model is then encased in a ceramic shell through a carefully controlled dipping process. Once the shell is hardened, the wax is melted away, leaving a precise mold ready for casting. The expertise involved in each phase, from mold creation to the final pour, demonstrates a level of detail and craftsmanship that only industry veterans can truly master.
Authoritativeness in precision casting solutions is evidenced by the widespread adoption and recognition from leading industry players. Rigorous standards and certifications, such as ISO (International Organization for Standardization), underscore the trust manufacturers place in precision casting. By adhering to these strict standards, producers guarantee components that meet not only their specifications but also global benchmarks for quality and safety. The continuous investment in research and technology by casting experts solidifies their role as authoritative figures in the engineering community.
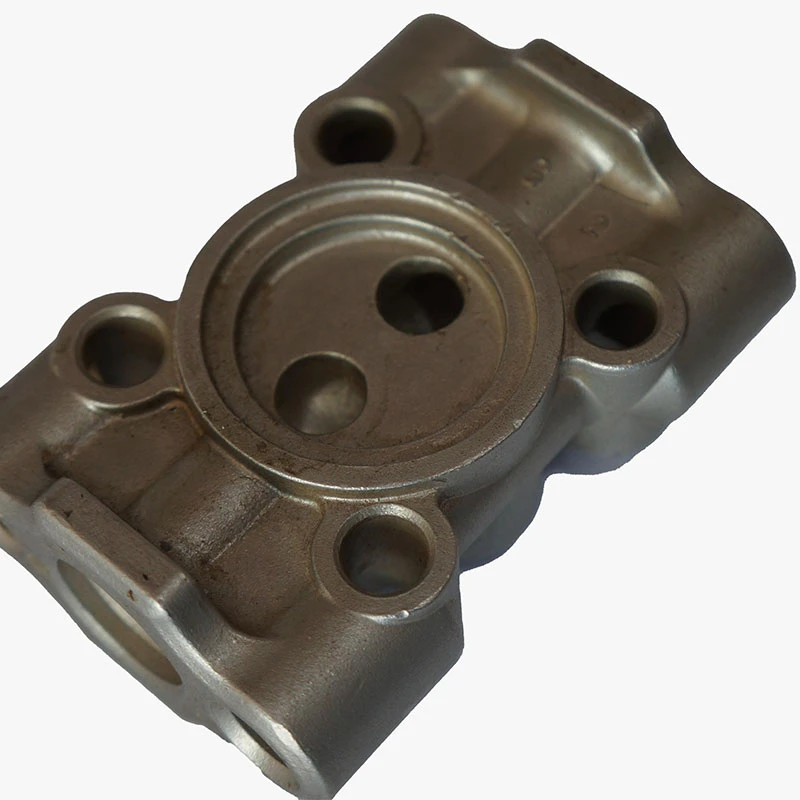
Trustworthiness is intrinsic to every step of the precision casting process. Manufacturers rely heavily on the consistency and reliability of their suppliers to deliver components that perform impeccably in critical applications. For example, in aerospace, where each component’s failure could lead to catastrophic outcomes, trust in the casting process is non-negotiable. Detailed quality control procedures and post-casting inspections ensure that each piece meets stringent criteria. By maintaining an unwavering commitment to quality, suppliers earn the trust of OEMs (Original Equipment Manufacturers) and end-users alike.
precision casting solutions
In the practical application of precision casting solutions, several case studies highlight its transformative impact. A notable example involves a leading automotive manufacturer seeking to enhance fuel efficiency. By employing precision casting, the company was able to produce lightweight but robust engine components that improved fuel economy without compromising performance. Such success stories exemplify how precision casting solutions not only meet but exceed the evolving demands of modern manufacturing.
As we look to the future, advancements in precision casting technology continue to reshape its potential. Innovations such as 3D printing for mold creation and enhanced ceramic materials promise to push the boundaries of what is achievable, reducing lead times and costs while improving component complexity and performance.
Manufacturers considering precision casting solutions must align with experienced and reputable partners who can navigate the intricacies of the process. With the right expertise and commitment to quality, precision casting offers a path to achieving excellence in production, driving innovation, and maintaining a competitive edge in an ever-evolving market landscape.
Ultimately, the journey through precision casting is a testament to human ingenuity, merging age-old techniques with modern technology to address the challenges and demands of contemporary manufacturing. As the industry continues to evolve, those invested in precision casting solutions stand at the forefront of a new era of precision engineering.