Miniature zinc die casting is revolutionizing industries with its unparalleled precision, versatility, and efficiency. Companies requiring minuscule yet intricate components are increasingly turning to this innovative process, and for good reason. Noted for its high dimensional accuracy, zinc die casting enables the production of complex shapes at a fraction of the cost associated with traditional manufacturing methods.
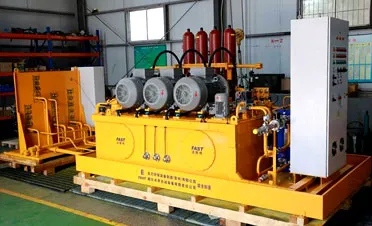
Real-world experience underscores its advantages in applications ranging from consumer electronics to the automotive industry. Seasoned manufacturers extoll the merits of zinc alloy, primarily its excellent mechanical properties and superior finishing capabilities. Confident in its non-corrosive nature, industries appreciate that zinc is a sustainable resource, reassuring stakeholders of its environmental viability.
Expertise in miniature zinc die casting has developed exponentially, drawing attention from engineers keen to meet exacting standards. The process begins by injecting molten zinc into precision-crafted steel molds. As a result, components achieve not only exceptional accuracy but also maintain high ductility and impact resistance, thanks to the alloy's inherent properties. Knowledgeable about the importance of structural integrity, experts emphasize that zinc's low melting point extends mold life, carrying a dual benefit of reducing wear and production costs.
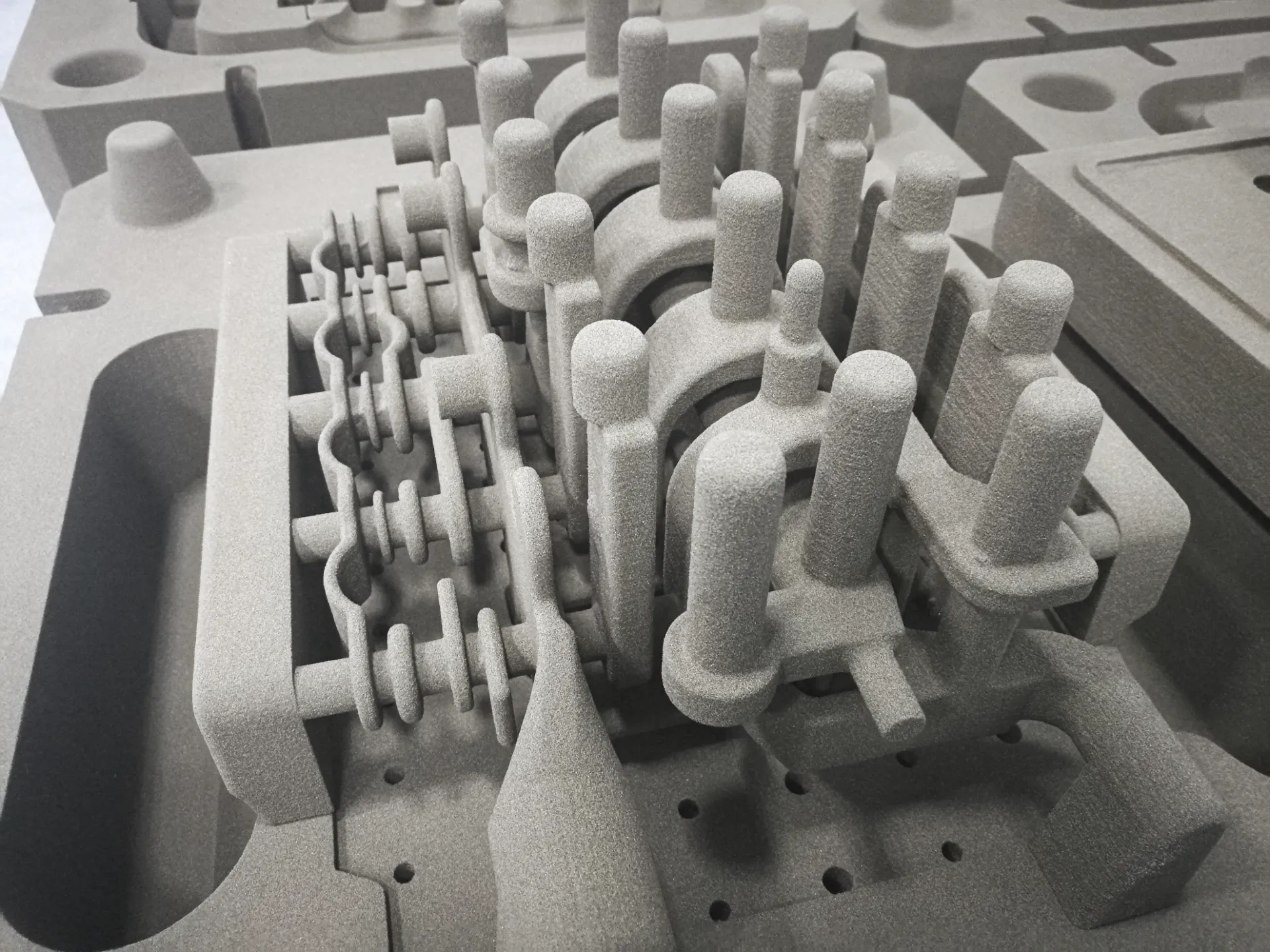
Authoritativeness in the field stems from decades of empirical research and development. Prominent manufacturers, through rigorous testing, have fine-tuned zinc die casting techniques to produce micro-scale parts that consistently deliver on quality and durability. These pioneers underscore the adaptability of zinc over other metals, citing its alloy strength and resistance to high-pressure environments as pivotal to meeting modern engineering challenges.
miniature zinc die casting
Trustworthiness in adopting miniature zinc die casting is further endorsed by stringent compliance with global manufacturing standards. Specialists confirm the reliability of zinc components in critical systems, backed by certifications that ensure safety and consistency. The industry’s transparency in process innovations and quality checks builds confidence among consumers and stakeholders alike. Clinching customer trust, companies offer comprehensive documentation, outlining every stage of production and quality assurance.
In the realm of product development, the advantages of miniature zinc die casting are palpable. Efficiency is realized not only in condensed production timelines but also through minimized material wastage and energy consumption. This aligns with a growing global emphasis on sustainability. Reduced lead times translate to swift market entry, allowing businesses to maintain a competitive edge.
Accompanied by expert guidance, the strategic implementation of miniature zinc die casting can propel products to new heights of functionality and appeal. The seamless integration of bespoke designs into manufacturing processes expands the creative potential for product engineers, charting a clear path from conceptualization to realization.
Conclusively, miniature zinc die casting is not merely a manufacturing method; it's a testament to human ingenuity and advancement in material sciences. Its role is pivotal in a future where demand for precision and efficiency intersects with an unyielding commitment to sustainable practices. As industries continue to evolve, so does the potential of miniature zinc die casting in crafting the many parts that power our world.