Unveiling the Art of Sand Casting Revolutionizing Metal Manufacturing
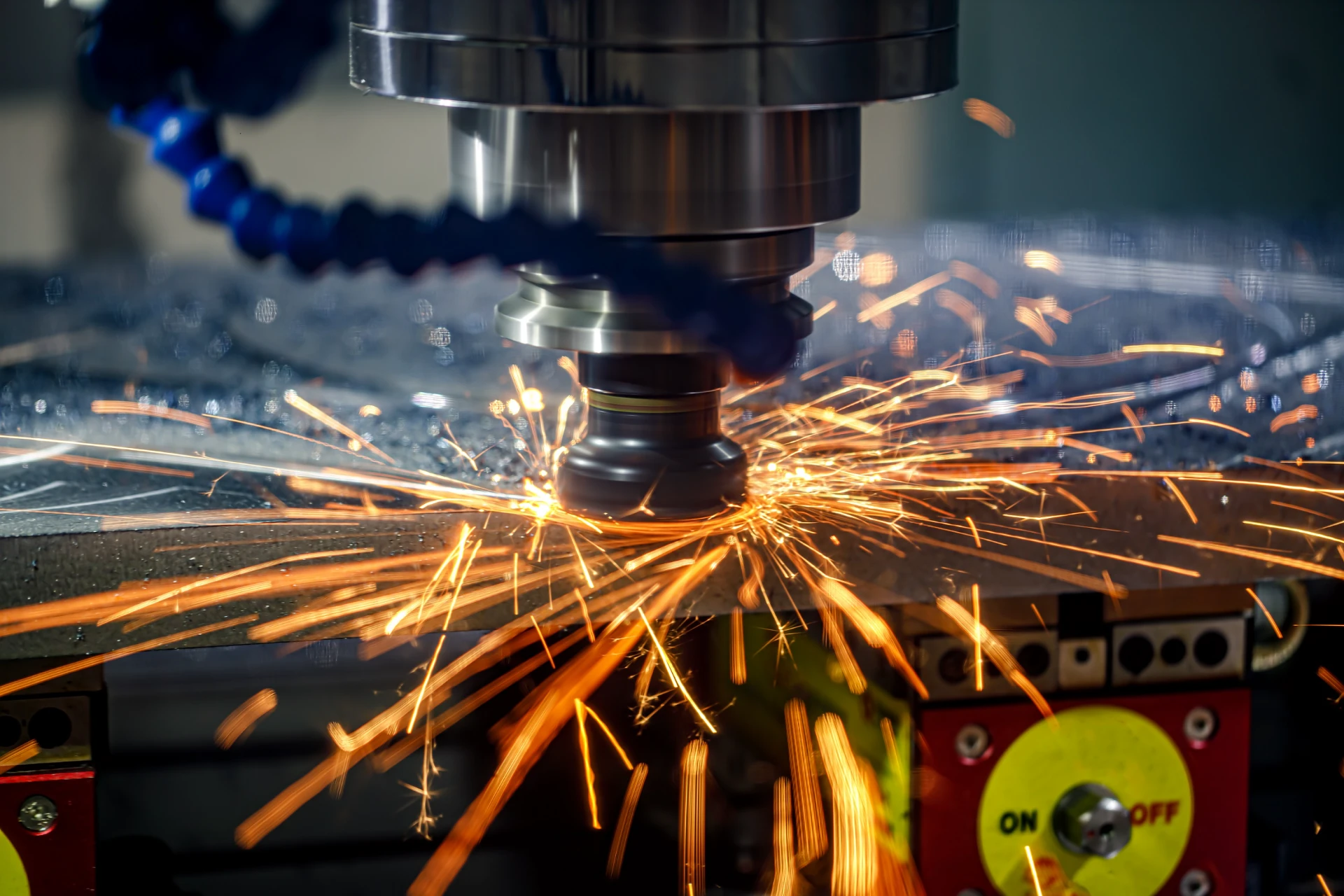
Sand casting, a pivotal method in the metal manufacturing industry, is continuously evolving to meet modern demands. It stands out for its versatility and ability to produce complex shapes with intricate details. This time-honored process, enriched by technological advancements, is a testament to both its reliability and potential for innovation.
The essence of sand casting lies in its simplicity and effectiveness. It begins with creating a mold cavity in the sand by compressing sand around a pattern. This mold serves as a faithful replica of the desired metal object. The patterns are typically made from materials like wood, metal, or plastic, carefully crafted to capture every detail that will translate into the final product. The choice of sand is equally critical, as the grain size, moisture content, and clay mixture influence the mold’s stability and the intricacy of the casting.
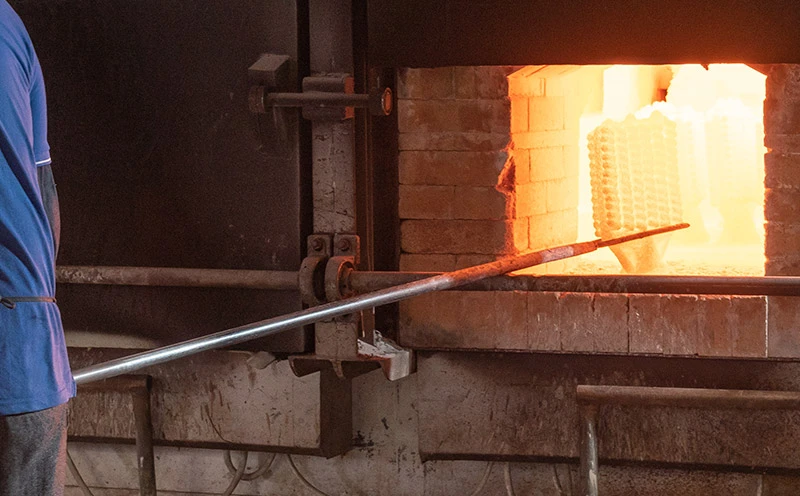
Among various molding sands, silica has been a preferred choice due to its thermal resilience. However, environmental concerns and health considerations have spurred interest in alternative materials like olivine and chromite sands. These not only enhance the safety profile but also improve the quality of the casting surface.
Once the mold is ready, it undergoes a critical phase where molten metal is poured into the cavity. This is where the foundry’s expertise becomes evident. Maintaining the ideal temperature and composition of the molten metal is vital to avoid defects like porosity and warping. The cooling rate is meticulously controlled, often using chills or other auxiliary tools, to ensure that solidification starts uniformly across the casting. This precision minimizes the occurrence of unwanted stress points and preserves the structural integrity of the cast product.
The role of expertise is further highlighted in the post-casting processes. After cooling, the casting is extracted and subjected to secondary operations that refine its surface and dimensions. Techniques like grinding, machining, and blasting are employed to meet stringent specifications. Foundries proficient in these operations are distinguished by their ability to deliver products that marry aesthetic excellence with mechanical robustness.
metal casting in sand
Through continuous research and development, sand casting has embraced automation technologies such as robotic arms and 3D printing. Automated systems enhance efficiency by precisely replicating patterns and managing production sequences, reducing human error, and increasing throughput. In parallel, 3D printing has revolutionized prototype manufacturing and enabled rapid adjustments to design specifications without extensive downtime.
Despite the advancements, the human element remains irreplaceable. Skilled artisans and engineers bring their wealth of experience to problem-solving, often using their intuition to tweak processes for optimal results. This combination of human expertise and technological prowess is what sustains the authority and trustworthiness of companies specializing in sand casting.
In terms of reliability, sand casting continues to outperform many of its peers when it comes to large-scale production. Its capacity to accommodate diverse alloy materials—from aluminum and brass to sophisticated steel grades—provides unmatched flexibility in application across automotive, aerospace, and industrial sectors. This versatility, alongside relative cost-effectiveness, ensures that sand casting remains a sought-after solution for industries aiming for mass production of durable, precision components.
Customers can rely on sand cast products not only for their quality but also for their adherence to environmental standards. Responsible foundries adhere to stringent waste management protocols, recycling sand and minimizing emissions to align with global ecological goals. This commitment to sustainability enhances their credibility and fosters trust among eco-conscious clients.
The future of sand casting is vibrant, with digital integration poised to enhance every facet of the process. By leveraging data analytics and artificial intelligence, foundries can predict potential faults, streamline workflow, and ensure seamless supply chain management. As these advances unfold, they will propel sand casting into an era where quality and efficiency coexist without compromise.
In conclusion, the sustained relevance of sand casting is a testament to its unique blend of tradition and innovation. Whether refining old techniques or embracing cutting-edge technology, this process exemplifies a synthesis of artistry and engineering that's crucial for future-proofing the metal manufacturing industry.