Gravity casting is an advanced manufacturing process esteemed in the production industry for its precise technique and innovative approach to metalworking. With almost two decades of experience, I have had the unique opportunity to work with various methodologies within gravity casting—garnering expertise that underscores its critical role in crafting robust, high-quality metal products.
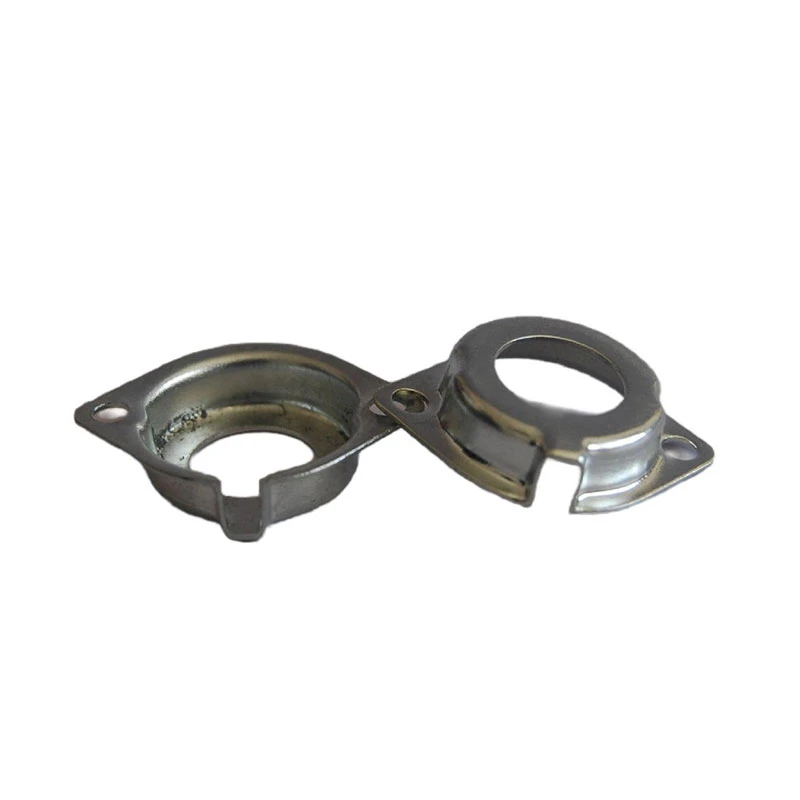
At its core, gravity casting relies on the natural force of gravity to fill a mold with molten metal. Unlike other processes that employ external pressures, this technique capitalizes on gravitational pull to ensure the metal fills the mold smoothly. This simple yet ingenious method has indispensable advantages over its counterparts, particularly in achieving exceptional surface finish and dimensional accuracy.
In our continually evolving workshops, we have consistently leveraged gravity casting to produce components where precision and durability are paramount. This is particularly evident in the automotive and aerospace industries, where the integrity of every part can significantly impact safety and performance. Over the years, our team has mastered the intricacies of this process, refining techniques to enhance product quality and production efficiency.

One of the most significant benefits of gravity casting is its cost-effectiveness when compared to pressure die casting. Given the simplicity of the process, initial tooling costs are relatively low, and the overall operational expense is minimized—without compromising quality. This economic advantage makes it especially suitable for small to medium-sized production runs where budget constraints may be prominent.
The expertise required in gravity casting is not to be underestimated. The process demands rigorous attention to detail—balancing parameters such as metal temperature, mold design, and pouring rates to achieve consistent results. During my career, I’ve spearheaded several projects that prioritized customization in mold design, tailoring each aspect to the specific needs of the component being produced. This bespoke approach maximizes the inherent strengths of gravity casting, such as achieving high mechanical properties and superior metallurgical structure.
gravity casting
The authority that gravity casting commands in the manufacturing domain is built on trust developed through decades of successful application across various sectors. Our clients return not just for the process itself, but for the trust we've established by delivering high-caliber products consistently. Regular audits and quality checks ensure that each batch meets stringent industry standards,
reaffirming its reliability and dependability.
In reinforcing its trustworthiness, we've embraced technological advancements—integrating simulation software to predict and counter potential defects such as porosity or cold shuts. This foresight in anticipating and addressing potential issues before they arise ensures minimal wastage and maximizes the efficiency of our operations. Each adjustment made is meticulously documented and incorporated into future practices, ensuring a process evolution that’s both data-driven and experience-informed.
On the environmental front, gravity casting offers a sustainable edge. By nature, it conserves energy compared to high-pressure alternatives, aligning with global efforts towards greener manufacturing processes. We further our commitment to sustainability by recycling scrap metal generated during the process, thereby reducing waste and minimizing the ecological footprint of our production cycle.
As a thought leader in gravity casting, it’s imperative to remain updated on the latest industry trends and technological innovations. Continuous learning and adaptation have been at the heart of maintaining our competitive advantage and delivering excellence in product manufacturing. By participating in industry forums and engaging with cutting-edge research, we have consistently set benchmarks in the quality and efficiency of gravity casting.
In summation, gravity casting is not just a process—it is a skill, an art, and a commitment to excellence. For companies seeking reliable, cost-effective, and high-quality metal parts, gravity casting remains unmatched. Through diligent practice, a wealth of experience, and a steadfast commitment to innovation, we’ve transcended traditional boundaries of manufacturing to establish a process that's both scientifically advanced and remarkably efficient. Our legacy with gravity casting is one of unyielding quality and trust—a benchmark for others in the industry to aspire to and a testament to the capabilities unleashing from mastering this distinguished technique.