Die casting, an advanced metal casting process, is indispensable in producing intricately shaped metal parts with precision and consistency. For those unacquainted with this critical industrial method, understanding its multifaceted nature is essential for appreciating its importance in manufacturing products ranging from automotive components to electronic housings.
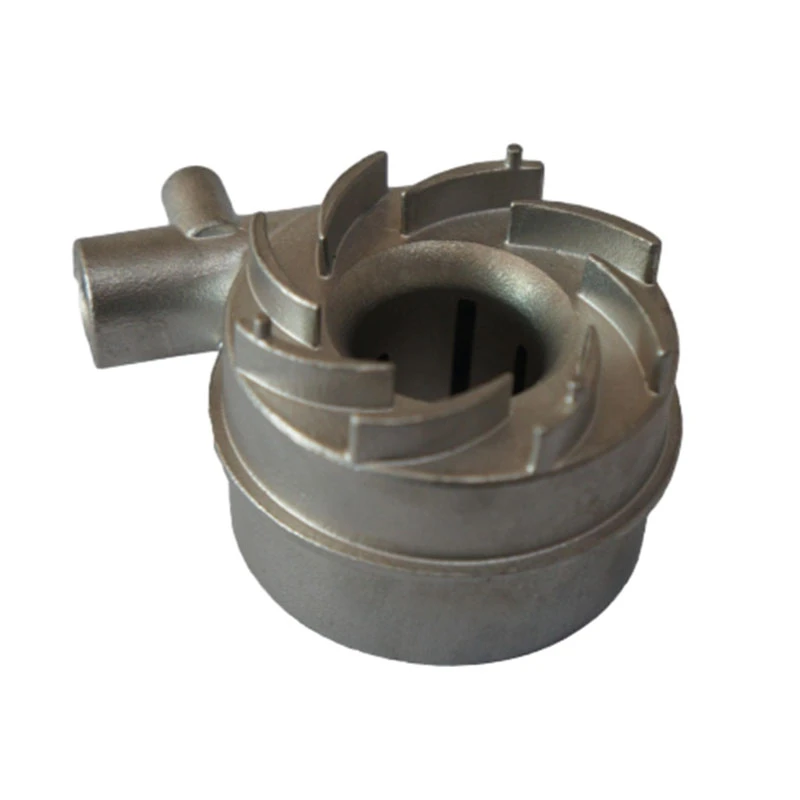
Die casting utilizes a mold or die to shape molten metal into precise dimensions and complex shapes. The process involves injecting molten metal under high pressure into these steel molds, and once the metal solidifies, the die is opened to remove the casted part. One of its foremost advantages is the ability to produce components with tighter tolerances that require little to no post-production machining.
The selection of the metal is a crucial factor in die casting. Common metals include aluminum, zinc, magnesium, and copper. The choice depends on the specific needs of the product, determined by factors such as metal properties, cost, and application requirements. Aluminum, for example, is known for its lightweight yet durable characteristics, making it ideal for automotive and aerospace industries. Zinc offers ease of casting, high ductility, and good finishing attributes, suitable for complex shapes and high-volume production.
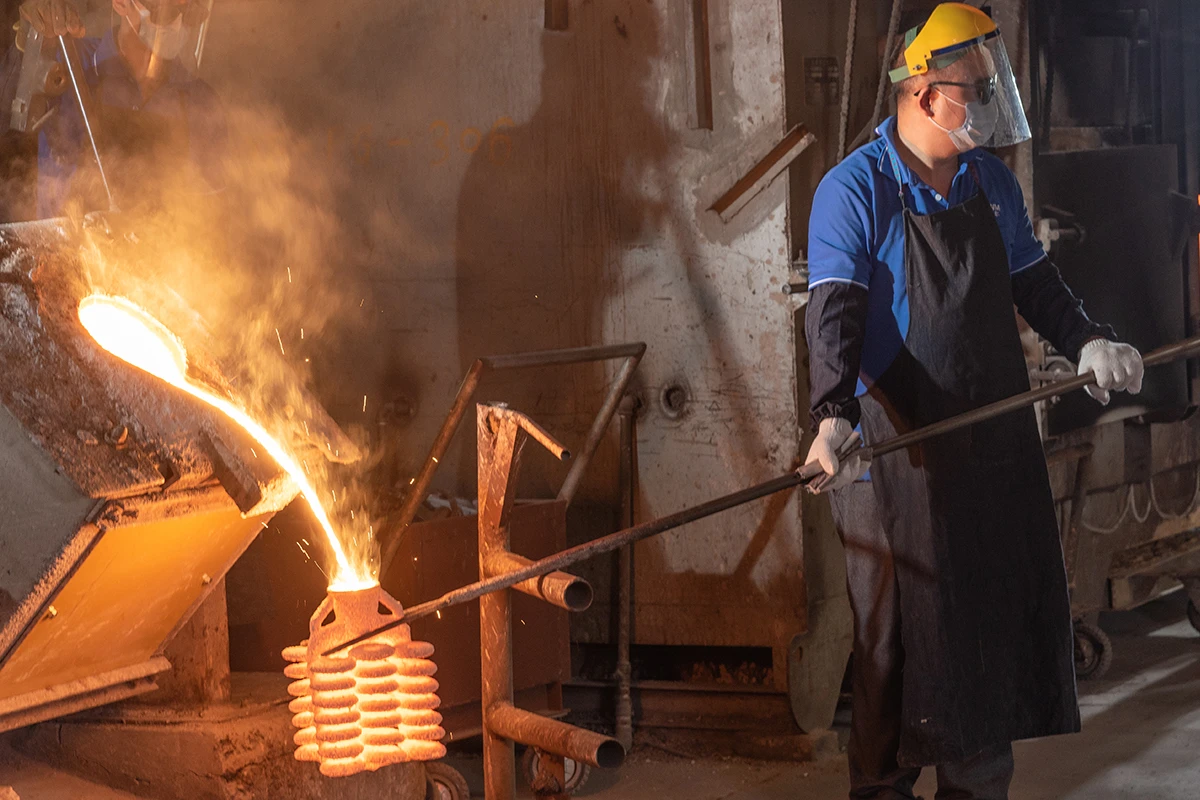
It's important to note the difference between hot chamber and cold chamber die casting processes. In the hot chamber die casting, also known as gooseneck casting, the injection mechanism is submerged in molten metal. This method is fast and economical, best suited for metals with low melting points like zinc and magnesium alloys. Cold chamber die casting, on the other hand, involves transferring molten metal into the chamber through a hopper or injection system. This method often deals with metals like aluminum and copper alloys, which are better for higher temperature casting.
Quality control in die casting is another advisory principle. Proper mold design, precision in metal temperature and pressure, and consistent quality checks are paramount for ensuring the integrity of the final product. Advanced techniques like real-time x-ray inspections or dye penetrant examinations are used to detect voids, inclusions, or other imperfections in the casted parts.
die for casting
Sustainability in die casting is garnering increased attention due to growing environmental concerns. From reducing energy usage during melting and casting processes to recycling scrap metal, the industry is increasingly focusing on eco-friendly practices. Technologies enabling efficient energy consumption, such as regenerative burner systems, alongside strategies to enhance the recyclability of metals without compromising product quality, are pivotal.
Additionally, the expertise brought by automation in die casting cannot be overstated. Modern die casting facilities increasingly use automated systems for increased cycle times, improved process repeatability, and reduced human error. Robotics have been implemented for tasks such as loading metal, spraying release agents on molds, and extracting finished products, ensuring a higher throughput and consistency in quality.
As die casting technology evolves, expertise remains critical in optimizing the process outcomes. With this in mind, training and experience in this field continue to be of utmost importance. Professionals skilled in areas such as mold design, material science, and automated systems bring a wealth of knowledge, enhancing the casting reliability and opening new avenues in complex part design.
Finally, trust and collaboration between die casters and their clients result in improved product development, where ideas are synergized to meet specific customization and performance goals. Consistent and open communication in understanding the nuanced aspects of die casting and addressing any technical blockers is part and parcel of maintaining a robust manufacturing relationship.
The reality is, mastering the art and science of die casting offers immense benefits – from yielding high-quality products with excellent surface finishes to enhancing productivity through automation. By focusing on innovation, sustainable practices, and quality assurance, die casting plays a pivotal role in shaping the future landscape of manufacturing. With its blend of experience and cutting-edge technology, the industry is poised to meet the ever-evolving demands of modern production while maintaining a commitment to excellence and precision.