When it comes to optimizing the process of creating high-quality die cast components, one crucial aspect stands out the die cast draft angle. Not only is this an essential parameter in the casting process, but it is a pivotal determinant in the practicality and functionality of the final product. The draft angle is the slight taper incorporated into the casting die surfaces. This taper facilitates the easy removal of the cast part without causing any damage to its surfaces.
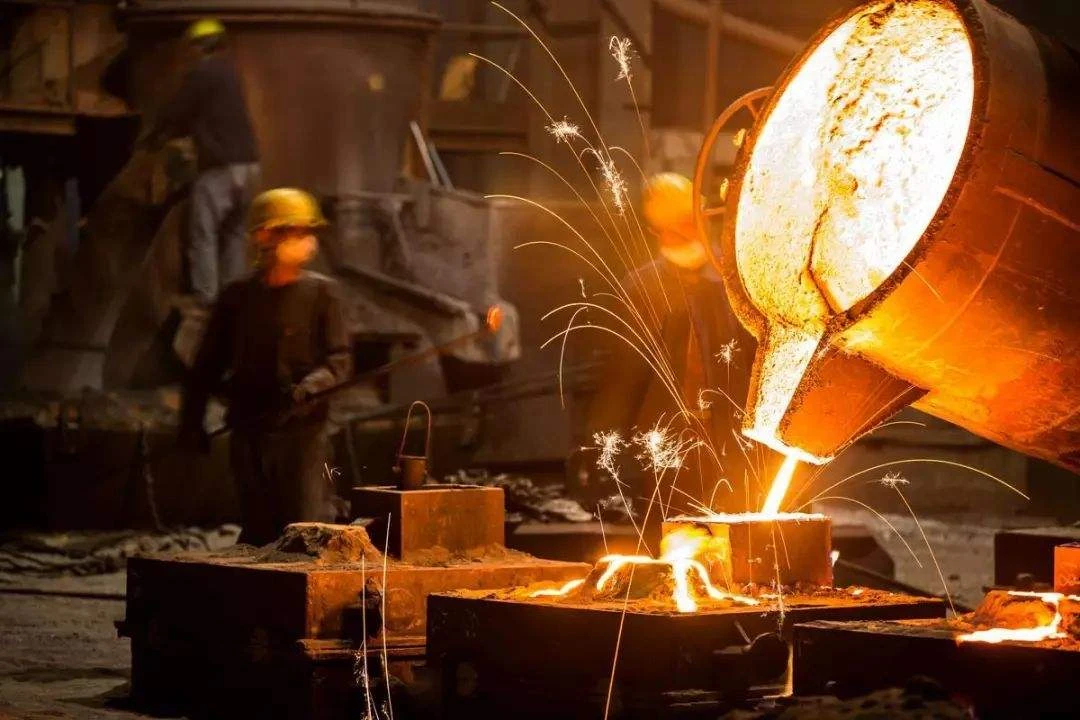
Manufacturers and engineers specializing in die casting understand the immense importance of the draft angle to both the production process and the overall product quality. A well-calculated and applied draft angle ensures that there are minimal issues during demolding, which reduces wear on the die and prolongs its lifespan. This not only cuts costs associated with die maintenance and replacement but also enhances the production efficiency, providing a seamless manufacturing flow.
Experience has shown that much of the expertise in determining the appropriate draft angle comes from understanding the material being cast and the design of the component. Different materials respond differently to the stresses and temperatures of the casting process. For instance, zinc alloys often require different draft angles compared to aluminum alloys due to their inherent properties. Experts often suggest a draft angle range between 1 to 3 degrees, although this can be adjusted based on the complexity and specific requirements of the design. Such expertise ensures the part’s dimensional accuracy while facilitating smooth ejection.
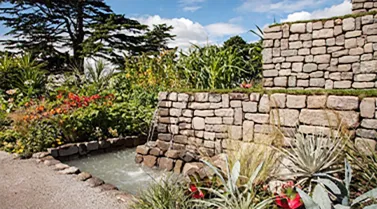
With authoritative guidance, designers should also consider the impact of draft angles on the aesthetic and structural properties of the final product. An incorrect draft angle can result in a part that has poor surface finish or, worse, a compromised structural integrity. Authority in this domain comes from both theoretical knowledge and extensive practical application. Engineering consultants, often with years of experience, bring this authority to projects, ensuring that the draft angle not only meets production requirements but also aligns with the end-use application demands.
die cast draft angle
Trustworthiness in the context of die casting and draft angles is largely about consistency and reliability. Companies known for their expertise in managing draft angles are often those whose products reveal a track record of durability and consistency. Trust is built by delivering components that perform as expected in their specific applications. This is fundamental in industries where precision is non-negotiable, such as automotive, aerospace, and consumer electronics.
Therefore, understanding and implementing the correct die cast draft angle is not merely a matter of following industry norms but is also about integrating a deep understanding of materials, design intricacies, and end-user requirements. As the casting processes evolve with advancements in technology, continual learning and adaptation are necessary to maintain and improve the standards of die casting.
In conclusion, controlling the draft angle efficiently is indispensable in die casting to achieve superior product quality and production efficiency. By harnessing real-world experiences, industry expertise, authoritative insights, and building trust, manufacturers and product designers can significantly optimize their processes, reduce costs, and enhance product lifespans, ultimately leading to greater customer satisfaction and increased market reputation.